Welding cast iron is a task that requires precision, expertise, and the right equipment. The unique properties of cast iron—a material known for its brittleness and complex microstructure—demand careful selection of welding rods to ensure a quality weld. In this comprehensive exploration, we'll delve into the factors and nuances that define the choice of welding rods for cast iron, based on both seasoned experience and authoritative insights.
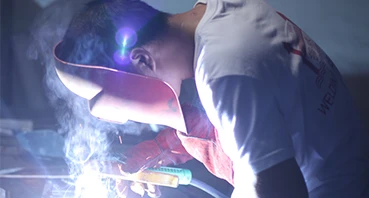
Choosing the appropriate welding rod for cast iron hinges on several critical factors the type of cast iron, the nature of the repair, and the anticipated stress on the final weld. Among the most trusted options in the welding community are nickel-based and steel-based rods, each offering distinct advantages.
Nickel rods stand out as the preferred choice for many professional welders when working with cast iron. They are celebrated for their high ductility and compatibility with the expansive nature of cast iron. In particular, the ENiFe-CI rods, which comprise a blend of nickel and iron, are recommended for their ability to manage thermal expansion and contraction, reducing the risk of cracking in the final weld. This characteristic is crucial when dealing with complex projects where the integrity of the weld is of paramount importance.
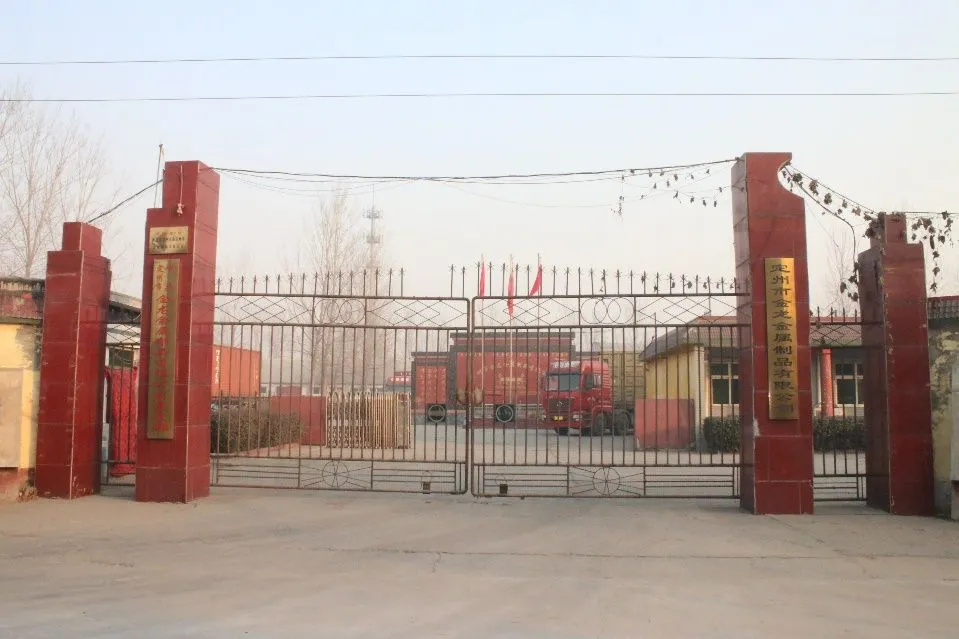
Anecdotal evidence from experienced welders supports the efficacy of nickel rods. For example, veteran welder James Thompson recalls a challenging repair on an antique cast iron engine block where nickel rods not only provided strength but were also easy to machine post-welding. This illustrates the practical benefits of these rods beyond theoretical advantages.
On the other hand, steel-based rods, though less common, can be a viable option for certain applications. Low-carbon steel rods are known to be cost-effective and can be useful in low-stress, non-critical welds where post-weld machining is not a concern. However, caution must be exercised as steel rods are less forgiving, and improper application can lead to severe cracking due to their limited ductility.
what rod do you use to weld cast iron
Understanding the project at hand is crucial. For instance, repairs on cast iron that will be subject to dynamic stresses or those requiring high structural integrity are better suited to nickel rods. They allow for a degree of flexibility and strength that steel rods might not provide. Also, detailed pre-weld preparation, such as controlled heating and cooling, is essential regardless of the rod choice to minimize stress concentration.
Professionals emphasize the importance of technique when welding cast iron with any rod. A practiced hand can ameliorate many potential issues, as seen in craftsmanship where consistent preheat and controlled cooling regimes are employed. These methods mitigate the thermal shock and stress that cast iron suffers from during welding.
Moreover, the process of arc welding cast iron is not just a matter of selecting the right rod but also involves mastering the correct weld sequence. Short, intermittent passes are advised to prevent warping and to distribute heat evenly. This approach, combined with the right choice of rod and conditions, ensures the highest success rate in welding cast iron.
In conclusion, the question of what rod to use to weld cast iron finds its answer in a combination of expertise, material compatibility, and situational judgment. Nickel rods, particularly, offer remarkable adaptability and are widely endorsed by professionals for their reliability across a broad range of cast iron projects. The insights from experts and seasoned welders underscore the significance of both the choice of rod and the holistic approach to the welding process. This delicate balance between science and craft establishes the foundation for successful cast iron welding, fostering trust and authority in industry practices.