Choosing the right welding rod for cast iron projects is pivotal for ensuring a durable and robust weld. Cast iron is known for being notorious in the welding field due to its high carbon content, which makes it prone to cracking and difficult to manipulate. However, with the right expertise and products, you can achieve reliable results.
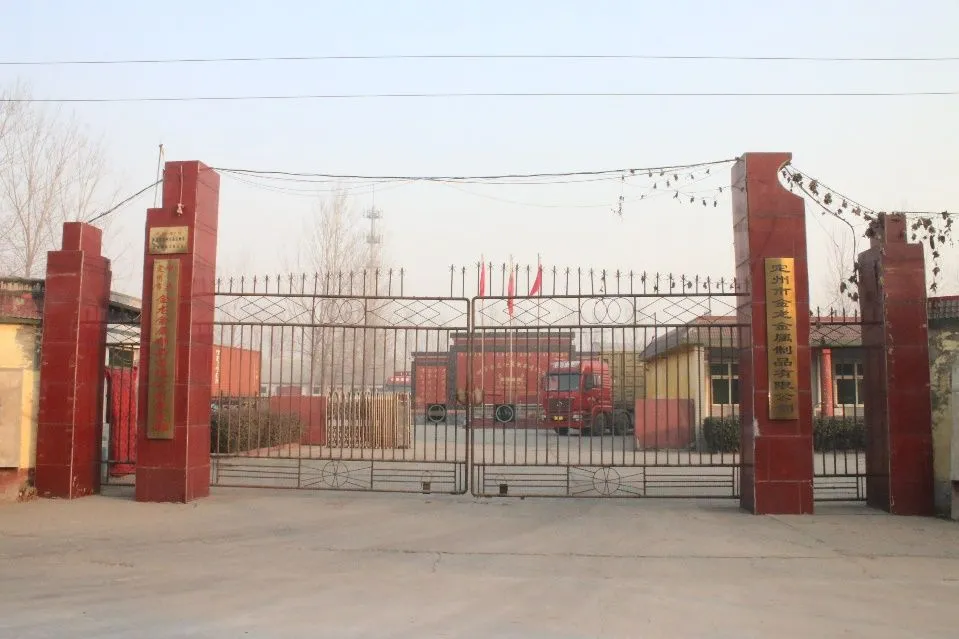
Understanding the unique properties of cast iron is the first step to successful welding. Cast iron is generally brittle and exhibits different expansion characteristics when heated, contributing to the challenges faced during welding. Therefore, using a welding rod tailored to these conditions can be the difference between a successful and a compromised weld.
Typically, nickel-based electrodes are favored for cast iron welding due to their ability to create strong and machinable joints. There are primarily two categories of these electrodes pure nickel rods and nickel-iron rods. Each type has specific advantages that suit different project needs.
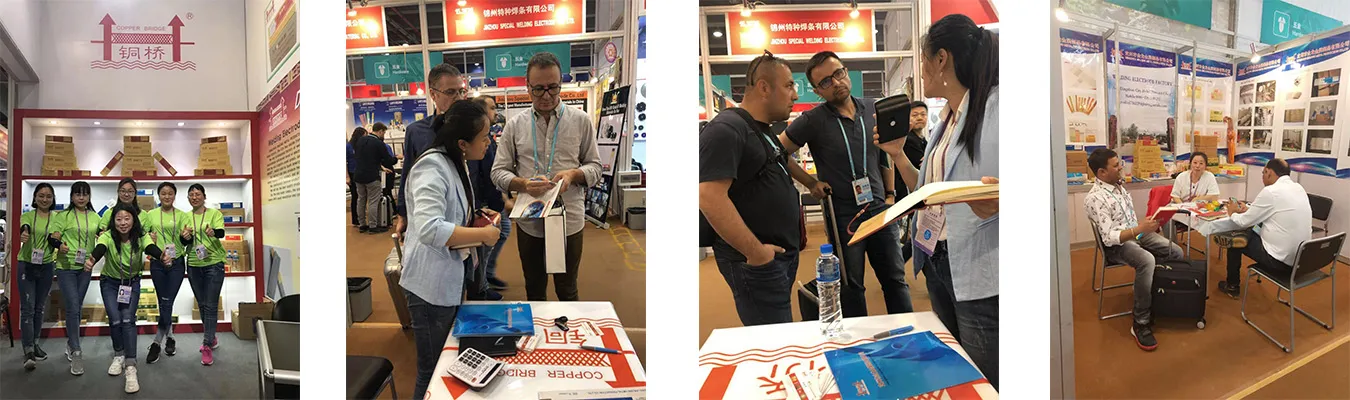
Pure nickel rods, such as the ENi-CI, are ideal for welding cast iron because they offer excellent machinability and result in a softer weld, making them less likely to crack during the cooling process. These rods are often recommended for critical applications involving the repair of broken cast iron components such as engine blocks or heavy machinery.
On the other hand, nickel-iron rods, labeled as ENiFe-CI, contain a composition of nickel and iron, which not only helps in achieving a strong weld but also reduces the cost compared to pure nickel rods. This blend assumes higher tensile strength and is suitable for large-scale applications where cost efficiency is paramount. For example, when working on thick cast iron structures that don’t require the fine finish a pure nickel rod would provide, a nickel-iron rod offers an excellent balance between performance and cost.
For those exploring an economical option, steel electrodes can also be employed with preheated and post-heated cast iron sections. However, this method demands a greater level of skill and experience, given the higher risk of immediate cracks if handled improperly.
what is the best welding rod for cast iron
Expert tips for achieving the best results include adequate preheating of cast iron components to reduce thermal stress. Maintaining a temperature between 500 to 1200 degrees Fahrenheit is often suggested before commencing the welding process. Slow cooling is just as critical. Some artisans bury welded parts in sand or wrap them in insulating blankets to control the cooling rate, thus minimizing the risk of cracking.
Furthermore, using a consistent and controlled welding technique can significantly impact the integrity of the weld. Short, intermittent welds with controlled electrode angles allow for precision, reducing stress on the brittle cast iron.
Availability of products and guidance from authoritative suppliers is also essential. Trusted brands like Lincoln Electric and ESAB offer reliable welding rods supported by extensive user guidelines and technical support to assist both novice and experienced welders.
Lastly, entrusting your projects to welders with proven expertise in working with cast iron can enhance outcomes considerably. Their on-the-ground experience with different rods and conditions can guide you towards the best materials and practices for specific situations.
In conclusion, choosing the best welding rod for cast iron involves considering the specific demands of the project, understanding the nuances of cast iron, and leveraging expert advice and authoritative resources. Whether prioritizing machinability with nickel rods, opting for cost-effective nickel-iron alternatives, or engaging expert services, these strategies ensure longevity and effectiveness in welding cast iron.