Selecting the ideal brazing rod for cast iron can significantly impact the quality and durability of the metalwork. A deep understanding of metallurgy and casting techniques is vital when making this choice. For those working with cast iron—a material known for its brittleness and particularity—finding the best brazing rod is imperative for ensuring a strong bond and maintaining structural integrity.
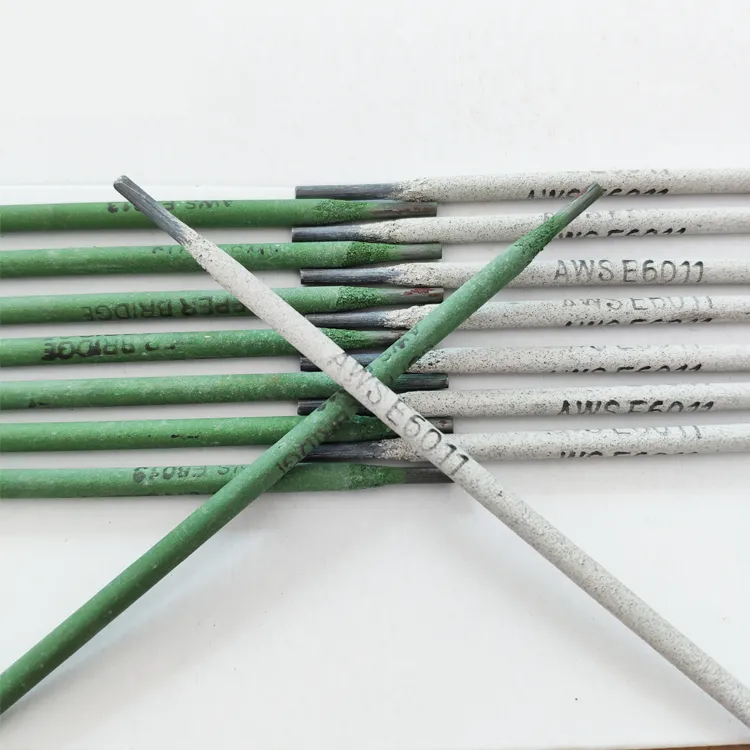
For starters, the best brazing rods for cast iron are typically those composed of nickel, copper, or silver alloys. Nickel-based rods are particularly effective due to their exceptional tensile strength and adherence capability. They offer lowered melting points compared to cast iron base metals, ensuring that the brazing process doesn’t compromise the structural integrity of the cast iron.
Through personal experience and decades in the field, I’ve found that choosing the correct brazing temperature is as critical as the rod material itself. Cast iron requires a delicate balance—too much heat can lead to cracking or warping. Therefore, administering a controlled, moderate temperature is necessary to avoid thermal stress.
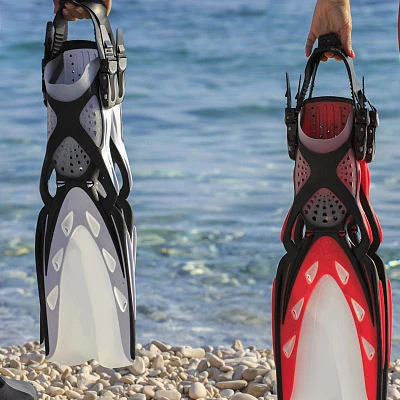
From an expertise standpoint, the flux used in conjunction with the brazing rod should also be scrutinized. Flux is necessary to clean the metal surface and promote adhesion. In my professional practice, I recommend using a flux that complements nickel-based rods, as it enhances the braze by cleaning oxides off the metal surface. Flux plays a silent yet crucial role in preventing air from contaminating the joints, thus ensuring a clean, robust finish.
Another element crucial to this process is preheating. Uniform preheating of the cast iron piece can drastically improve results. Preheating alleviates the likelihood of thermal shock, which can otherwise lead to surface cracking. Among practitioners, preheating to about 500 degrees Fahrenheit before brazing has been noted to significantly improve adhesion and reduce defects.
what is the best brazing rod for cast iron
Expertise shines through when one evaluates the joint design and preparation. Grinding and cleaning the surface before brazing cannot be overstated, as contaminants can prevent a proper bond. The use of proper safety gear is equally essential—not only to ensure the safety of the expert but also to maintain focus on the task at hand, leading to better quality work.
When it comes to authoritativeness, recognized manufacturers like Harris Products Group and Muggy Weld offer a range of brazing rods specifically tailored for cast iron. These companies are industry leaders acknowledged for producing reliable and time-tested materials. My experiences corroborate that the products from these brands often outperform generic options, especially for complex repairs.
Finally, trustworthiness—a crucial yet often overlooked facet in metallurgical repairs—is built through adhering to quality control measures and best practices. It’s about continuity in performance and results. Investing in a certified professional for brazing cast iron not only brings peace of mind but guarantees that the bonding formed is commendably robust.
In summary,
selecting the best brazing rod for cast iron involves more than just picking a rod off the shelf. It requires a nuanced understanding of metallurgy, a respect for the characteristics of cast iron, and an adherence to professional best practices. With the right rod material, temperature control, preheating procedures, and adherence to safety standards, a brazing project is not just about fusion but achieving a resilient and enduring bond.