Welding cast iron presents unique challenges due to its composition and characteristics. When selecting a rod for welding this commonly used engineering material, it's critical to understand the nuances that contribute to a successful outcome.
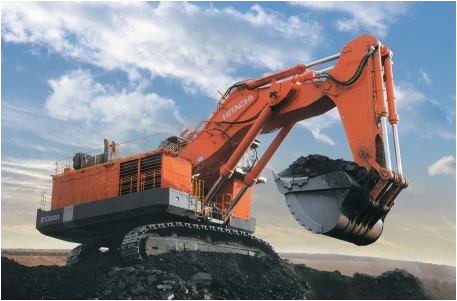
Experience counts significantly in working with cast iron. Several years ago, during a rigorous workshop repair project, I encountered the task of welding a broken cast iron lathe stand – a valuable lesson in material temperament and rod selection. Each type of cast iron rod offers distinct advantages and disadvantages, and selecting the right one is vital for durability and integrity in the weld.
Nickel alloy rods stand out as a preferred choice among professionals due to their flexibility and compatibility with cast iron. Nickel alloys, particularly AWS (American Welding Society) ENi-CI or ENiFe-CI electrodes, possess high levels of conformity with cast iron. The elasticity of nickel accommodates the base metal's thermal expansion and contraction, reducing the risk of cracks during cooling.

On the other hand, steel rods, though less costly, pose more complexity. Steel tends to have a different cooling rate and can induce stress within the iron, leading to brittleness or cracking. Preheating the cast iron is essential when using steel rods, but the risk may outweigh the cost benefits for those without extensive expertise.
Some practical tips for welding cast iron with nickel rods include the necessity to keep the joint size minimal. Small beads minimize heat input, reducing stress and the risk of cracking. Also, maintaining a consistent preheat and post-heat can further stabilize the weld. An experienced welder focuses on controlling both heat application and dissipation which helps maintain the structural integrity of the iron.
From an uncertainty standpoint, there's a distinct challenge in welding cast iron due to its graphite structure. Cast iron's carbon content increases its brittleness while welding. Therefore, it’s essential to adopt a technique that respects its inherent characteristics. Choosing the right rod is critical, but equally so is the procedure itself. Always grind out a slot in the crack, allowing for penetration and a sturdier bond.
what rod to use to weld cast iron
Cost is another consideration. Nickel rods are typically more expensive than basic steel or iron rods. However, considering the potential cost of a failed project, investing in premium quality rods offers long-term savings. People frequently underestimate the importance of quality materials in weld projects, especially with something as finicky as cast iron.
Expertise grows from observation and repetition; meticulous preparation, correct rod selection, and precise heat management form the core practices recommended by experts. While welders may occasionally opt for cheaper alternatives with mixed success, the consensus leans towards nickel for reliable results.
Trustworthiness in product performance derives from an understanding of the rod's properties in relation to the base material. Supplier reputation also plays a critical role.
Seek rods from manufacturers with a proven history of success in cast iron products. Through testing and field application, reliable recommendations often surface within industry circles, favoring suppliers with consistent quality assurances.
The deployment of cast iron components spans countless applications, from machinery parts to antique restorations. Therefore, experience in selecting the proper rod contributes fundamentally to project success and longevity. Avoiding shortcuts in material quality and preparation can determine the difference between an effective repair and a repetitive failure.
In summary, choosing what rod to use for welding cast iron demands consideration of various factors material characteristics, project specifications, and skill level. Embracing nickel alloy rods offers an edge in both flexibility and dependability, fostering crack resistance and weld integrity. As technology and methodologies evolve, so too does our understanding of optimizing welding procedures for cast iron – broadening opportunities for application and innovation. Thus, the wisdom of experience, combined with expert product knowledge, yields the most reliable results in cast iron welding.