Welding rods, also known as welding electrodes, are vital components in the welding process, serving as a mediator that connects the welding machine and the base material.
They come in various types and sizes, tailored to meet the demands of different welding projects. Choosing the right welding rod is crucial for achieving strong and dependable welds, reducing defective welds, and increasing overall productivity.
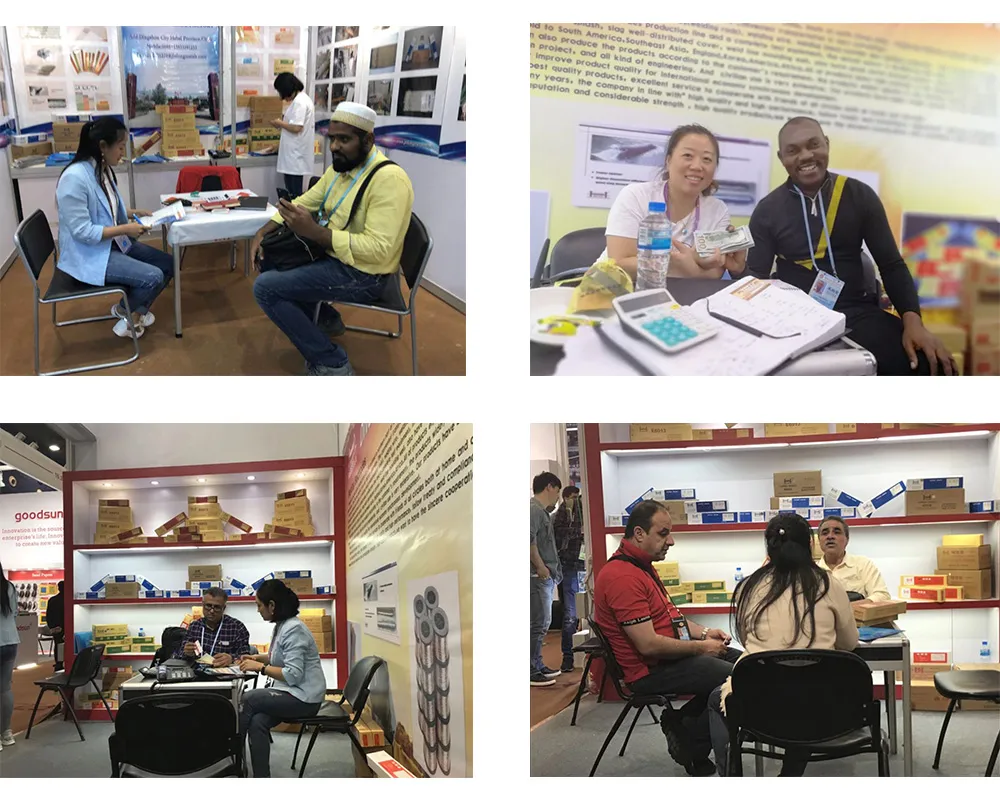
Understanding the different types of welding rods begins with discerning their suitability for specific metals and applications. There are several types of welding rods, each coded for their unique properties. The most commonly used type, for instance, is the E6010 rod. This electrode is renowned for its high cellulose sodium coating, providing deep penetration that works excellently on dirty, rusty, and painted surfaces. It's ideal for open root welding and is often the preferred choice in pipe welding projects.
Another prevalent type is the E6011, which, like the E6010, offers deep penetration but comes with the added advantage of being suitable for AC and DC polarity. This versatility makes it a go-to choice for many beginner welders. Meanwhile, E6013 electrodes are known for their all-position welding capability and smooth arc performance, making them suitable for welding sheet metals and light-duty fabrication projects.
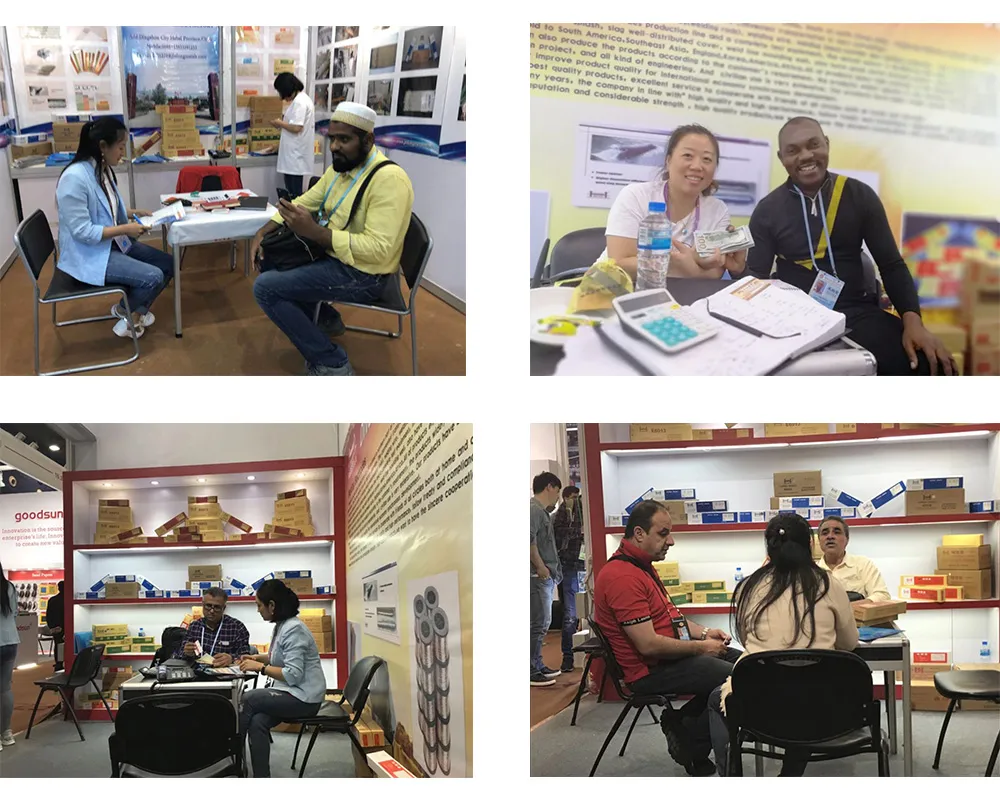
For heavy-duty and industrial applications, the E7018 rod stands out due to its low-hydrogen iron powder coating. This electrode is specially designed to weld high-strength steels and provides welds with minimal spatter and superior crack resistance. It's highly favored in structural and high-pressure welding projects.
welding rod types and sizes
The sizes of welding rods also play a critical role in welding operations. The diameter of the rod affects the amount of filler material deposited and the overall heat input into the weld joint. Common diameters include 1/16 inch, 5/64 inch, 3/32 inch, and 1/8 inch, each catering to different thicknesses of base materials and welding positions. For instance, a thinner rod such as 1/16 inch is ideal for thin gauge sheet metal, allowing for better control and reduced burn-through. On the other hand, a thicker rod like 1/8 inch is better suited for heavy plate welding, providing deeper penetration and greater weld deposition.
Selecting the appropriate type and size of welding rod is not just about knowing their individual properties but also understanding the welding environment and requirements. Temperature conditions, base metal thickness, welding position, and power source are all factors that must be considered to ensure optimal welding performance. Utilizing the correct rod type and size can greatly influence the mechanical properties of the weld, dictating its strength, ductility, and longevity.
Moreover, employing the right storage techniques for welding rods is paramount. Moisture can significantly alter the performance characteristics of a rod, especially low-hydrogen varieties like the E7018. Therefore, maintaining rods in a dry environment, ideally through the use of rod ovens, will prevent them from absorbing moisture, ensuring they perform correctly and safely.
Whether you are a novice looking to start a hobby or a seasoned professional executing industrial projects, understanding the nuances of welding rod types and sizes is indispensable. It's a domain where expertise not only minimizes risks and resource usage but also delivers superior results that stand the test of time. This knowledge extends beyond theory, drawing from the experiences of expert welders and authoritative sources, fortifying its credibility within the welding community.