Selecting the appropriate welding rod is critical for ensuring the durability and strength of welded joints. The plethora of options available can be overwhelming, but focusing on key factors helps narrow down the choices effectively. Let's delve into the elements that influence this crucial decision, drawing from both expert insights and practical experience.
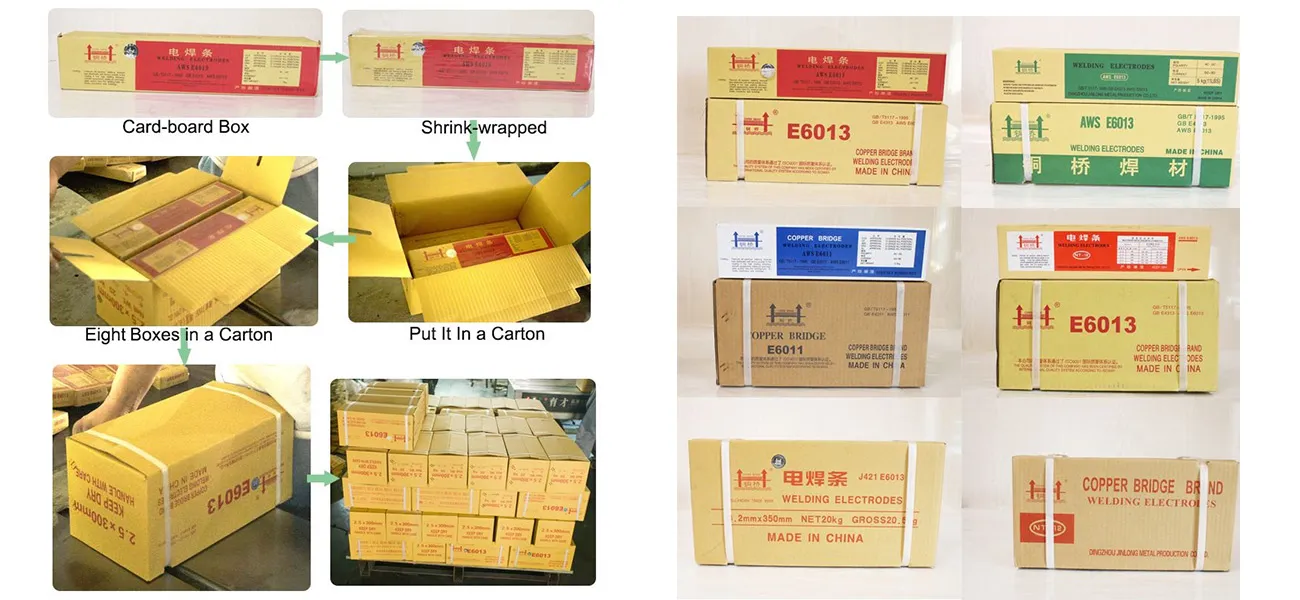
Material Compatibility The first step in selecting the right welding rod involves assessing the base material. Different rods are designed for specific metals such as steel, aluminum, and cast iron. For example, if working with mild steel, E7018 is a popular choice due to its versatility and strong weld deposits. Understanding the chemical composition and properties of the base metal ensures a compatible welding rod is chosen, which minimizes risks of weak welds or material failure.
Type of Weld Consider the type of weld you need, as different rods offer varied penetration levels and deposition rates. Whether it's a fillet weld or a groove weld, specific rods are tailored to meet these welding requirements. For thick sections where deep penetration is necessary, a rod like E6010 may be suitable, given its rapid freezing characteristic and deep penetration ability.
It’s crucial to match the rod to the welding task for optimal results.
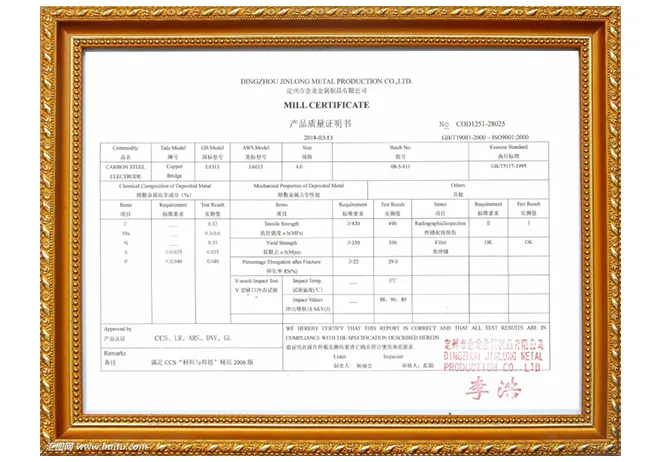
Welding Position Different rods perform better in certain positions. Some rods, like E6011, are all-position rods, meaning they can be used flat, horizontal, vertical, and overhead. This versatility can be particularly beneficial if the welding project involves complex geometries. Selecting a rod inappropriate for the position can lead to poor bead shape and increased defects, compromising the integrity of the project.
choosing the right welding rod
Electrical Characteristics The welding machine and its settings also play a critical role. Rods have specific amperage settings they operate best within. For instance, welding rods such as E7024 require high amperage and work well for flat and horizontal welding positions. Aligning the rod selection with the welding machine's capabilities ensures efficient energy use and minimizes electrode waste.
Environmental Conditions The working environment cannot be overlooked. Moisture, temperature, and even wind can affect welding outcomes. Some rods are designed to tolerate specific environmental challenges. For example, low-hydrogen electrodes like E7018 are used to prevent hydrogen-induced cracking in challenging environments but require storage in a dry, controlled condition to maintain low-moisture levels.
Skill Level The welder’s expertise significantly influences the rod choice. More experienced welders might prefer rods that require advanced techniques to achieve high-quality results. Conversely, for beginners or those seeking ease of use, selecting user-friendly, forgiving rods can enhance the learning experience, improve safety, and result in satisfactory welds with minimal imperfections. For ease of use and a smooth learning curve, E6013 rods are commendably forgiving and versatile for both novices and seasoned welders.
By focusing on these factors, welders can make informed decisions that not only match the project requirements but also enhance the quality and safety of their work. Companies supplying welding materials and training programs should continually update their offerings to reflect the latest industry standards and technological advancements, establishing themselves as trusted authorities in the welding sector. As welding technologies and materials evolve, staying informed and adaptable remains paramount for achieving professional excellence in welding projects.