Understanding common welding rod sizes is crucial for achieving optimal welding results in both professional and DIY projects. Welding rods, also known as filler metals, vary in size and composition, directly affecting the quality and strength of a weld. This article delves into the significance of choosing the right welding rod size, providing insights based on extensive experience and expertise in the welding industry.
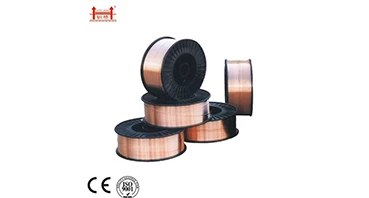
Welding rods are classified by numbers that denote their characteristics, such as tensile strength, position suitability, and flux type. Among these classifications, the diameter of the rod is a key parameter that influences the penetration and strength of the weld. Common sizes include 1/16-inch, 3/32-inch, 1/8-inch, 5/32-inch, and 3/16-inch, each serving specific welding needs.
The 1/16-inch rod, often used in applications requiring minimal penetration, is ideal for thin materials where excessive penetration could lead to warping or structural weakness. Its precision makes it suitable for delicate work on thin sheets where control and finesse are paramount.
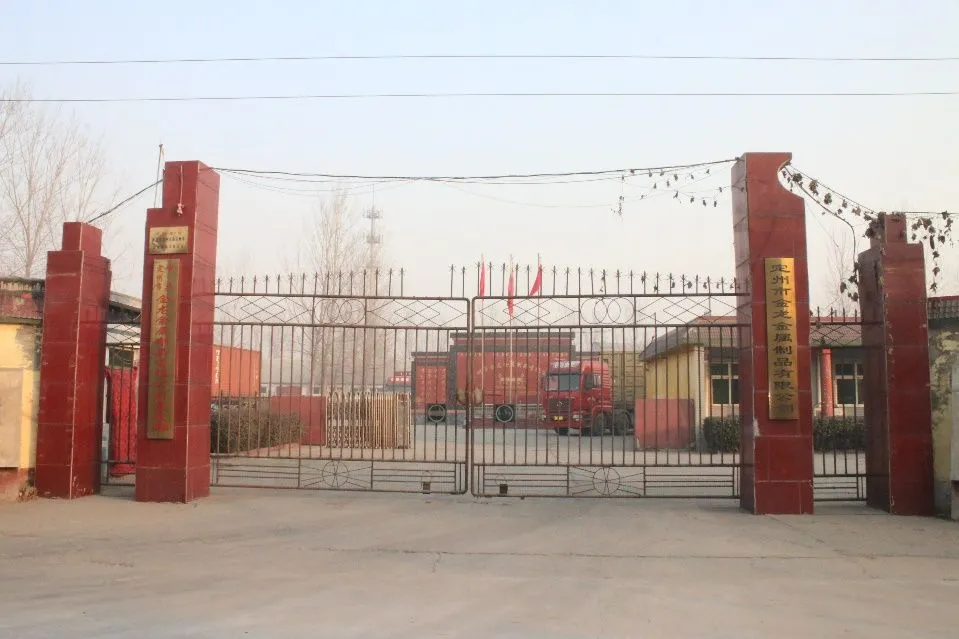
3/32-inch rods provide versatility, balancing penetration and deposition rates, making them a favorite among welders for standard jobs. These rods are frequently used in general-purpose applications, including maintenance and repair tasks, due to their ease of control and adaptability across various metals.
For those dealing with midsize projects, the 1/8-inch welding rod is a workhorse capable of deep penetration and robust joints. Its strength is well-suited for medium-thickness metals, delivering durability and resilience in structural welds. This size strikes a perfect balance for home users and professionals working on non-critical structural components.
common welding rod sizes
The 5/32-inch size is preferred for heavy-duty welding tasks, providing deeper penetration and a broader weld pool. Its capacity to handle thicker metals without compromising the weld's integrity makes it suitable for industrial applications and heavy machinery repair. This rod size ensures stable welds required to withstand significant stress and weight.
Finally, the 3/16-inch rod is reserved for the most demanding industrial tasks involving substantial metal thickness, where maximum penetration and deposition rates are essential. These rods facilitate high-productivity welding in environments that require heavy metal joins, like shipbuilding and high-pressure pipelines.
Selecting the right rod size is not merely about matching it to the metal thickness; it also involves understanding the welding position and electrical current compatibility. Experienced welders appreciate that while larger diameter rods deliver stronger welds, they also demand more power and control. Additionally, the quality of the weld bead, appearance, and mechanical properties of the weld joint depend significantly on the chosen rod size, flux composition, and welding technique.
Trust in authentic and authoritative sources for guidance on welding processes and rod selection ensures not only operational efficiency but also safety in welding practices. Leveraging professional expertise and adhering to manufacturer specifications can significantly enhance the welding outcome, reducing the likelihood of defects and structural failures.
To summarize, selecting the appropriate welding rod size is a critical decision that impacts the success of a welding project. Whether for everyday maintenance or complex industrial applications, aligning rod choice with project requirements and environmental conditions is essential. This approach guarantees not only strong and reliable welds but also fosters safety and precision in every welding endeavor.