Selecting the right size of welding rods can significantly impact the quality and strength of a welding project. Working with different sizes offers unique experiences, requiring expertise to ensure the best results. While choosing welding rods, it is essential to consider factors such as the material thickness, joint configuration, welding position, and the end-use of the welded structure.
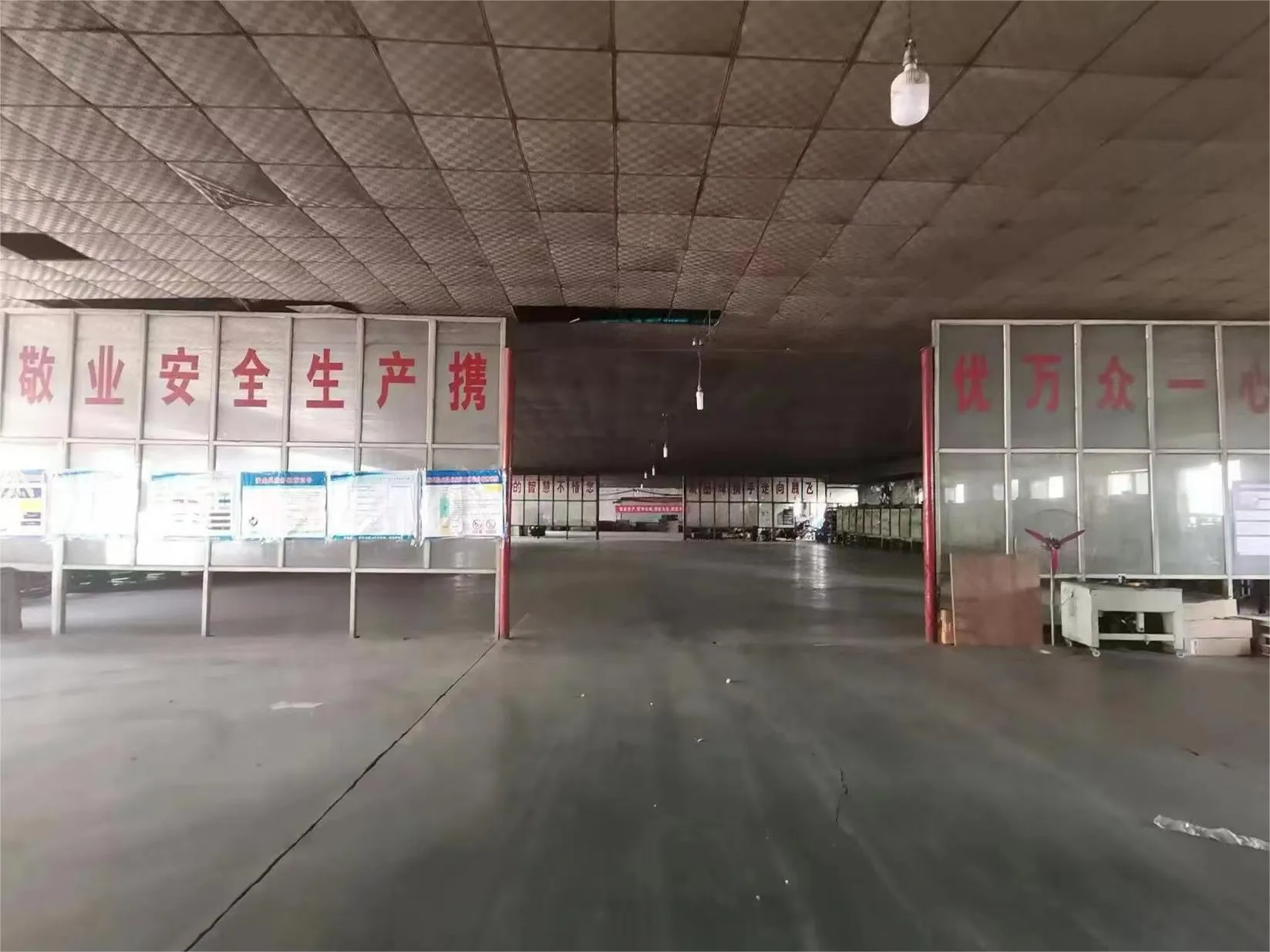
Welding rods, also known as electrodes, are available in a variety of sizes, typically ranging from as thin as 1/16 inch to as thick as 1/4 inch or more. Each size serves a distinctive purpose and is suited for specific types of welding tasks. For instance, thinner rods are ideal for light gauge metals due to their ability to create precise, controlled welds without risking burn-through. On the other hand, thicker welding rods can handle heavier materials and create stronger welds, essential for structural applications.
The expertise involved in choosing the correct welding rod size cannot be overstated. A skilled welder understands that the rod size directly correlates with the amperage range required to achieve optimal penetration and fusion. For example, thin electrodes such as 1/16 inch might require lower amperage settings to avoid warping or overheating thin materials like sheet metal. Conversely, a 1/8 inch rod would need a higher amperage to ensure sufficient heat input for thicker metals, ensuring a robust weld bead.
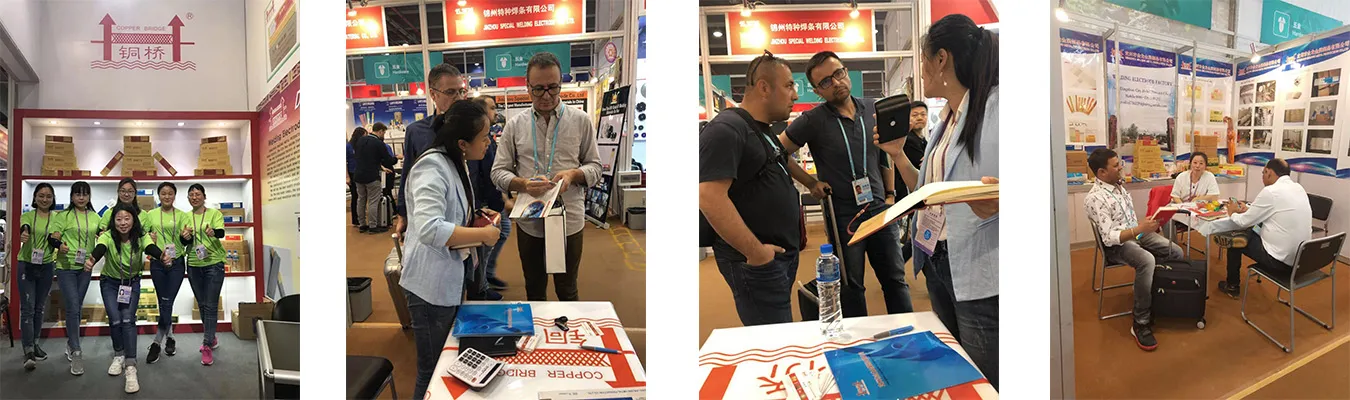
Beyond just size, the composition and coating of the welding rod also play critical roles. Experts emphasize selecting the appropriate rod based on the metal composition to prevent issues like cracking or weak joints. For low alloy and mild steel, popular rod options are E6010 or E6011, which offer deep penetration and work well in awkward positions. However, projects involving stainless steel or non-ferrous metals like aluminum demand specialized rods that align with those materials' unique properties.
different size welding rods
Authoritativeness in welding is built on understanding industry standards and best practices. For instance, guidelines set by agencies such as the American Welding Society (AWS) are trusted resources that welders rely on to ensure their work meets safety and quality benchmarks. According to the AWS, the choice of electrode size affects not only the weld strength but also efficiency and cost-effectiveness. Larger rods can speed up the welding process by laying down more filler material quickly, which can be advantageous in large-scale projects.
Trustworthiness in selecting welding rods is fundamental, particularly in critical applications like pipeline welding, construction, and automotive industries. A professional approach involves not only relying on expert advice but also considering the manufacturer's specifications and the intended environmental conditions where the welds will be applied. Quality welding rod brands often undergo rigorous testing and quality control, highlighting the importance of sourcing from reputable manufacturers to minimize defects and ensure consistency.
Ultimately, the decision on which welding rod size to use is intricate, blending an understanding of material science, welding techniques, and project requirements. Through experience and a profound grasp of technical nuances, professionals can execute welds that are not only strong and durable but also meet or exceed industry standards. The nuanced selection process underscores the need for continued learning and adaptation as new materials and welding technologies emerge, ensuring that welders maintain their edge in this essential craft.