Welding rods, often referred to as welding electrodes, are essential components in the welding process, serving as the filler material that connects two metal pieces together. Understanding the different types of welding rods and their applications is crucial for achieving strong, durable welds. This comprehensive guide provides in-depth insight into the various categories of welding rods and their specific uses, grounded in professional experience and technical expertise.
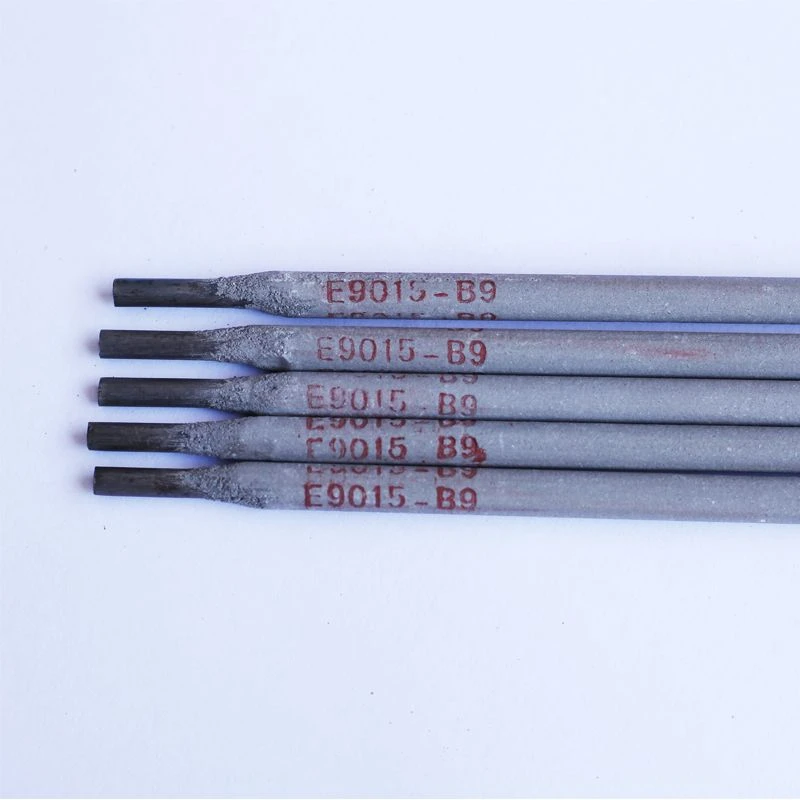
Welding rods are primarily classified into three types consumable, non-consumable, and flux-cored. Each type has distinct characteristics and applications, tailored for specific welding techniques.
Consumable electrodes are widely used in metal inert gas (MIG) and shielded metal arc welding (SMAW) processes. Among these, the E6010 and E6011 rods are noted for their deep penetration capabilities, making them suitable for welding through rust, oil, or paint on farm implements and piping. The E7018 rod is another popular choice, particularly for its low-hydrogen properties, which prevent cold cracking in structural steel, pipelines, and high-pressure environments. Experienced welders trust the E7018 for its versatility, yielding a stable arc and smooth finish across various positions.
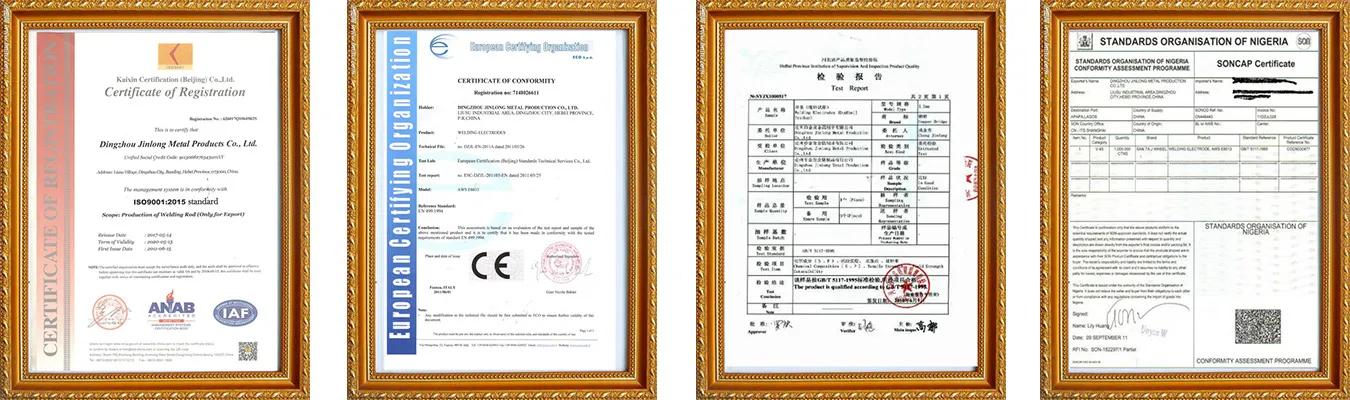
Non-consumable electrodes, such as tungsten electrodes, are fundamental in gas tungsten arc welding (GTAW or TIG welding). They do not melt during the arc process, thus requiring a separate filler metal. Tungsten electrodes are favored for precision welding tasks in aerospace, automotive, and art installations, where their ability to handle high-melting-point metals like stainless steel, aluminum, and magnesium is unparalleled. The choice between pure tungsten, thoriated, or ceriated tungsten depends on the specific welding requirement, with thoriated rods favored for their durability and superior arc stability.
welding rod types and uses
Flux-cored electrodes are designed for environments with challenging welding conditions, such as windy outdoor settings. This type includes self-shielded and gas-shielded variants, which incorporate shielding agents within the rod to protect the weld pool from atmospheric contamination. These rods are particularly useful in construction and shipbuilding. The E71T-1 rod, for example, is appreciated for its adaptability in producing high-quality welds in automated and semi-automated welding processes, especially in thick steel construction where bead appearance and no-spatter performance are critical.
Each welding rod type must be stored properly to maintain its efficacy. Moisture absorption is a common issue, particularly with low-hydrogen electrodes such as the E7018. Storage in a controlled environment, such as a dry rod oven, prevents moisture-related welding defects like porosity.
Welding professionals emphasize the importance of selecting the appropriate rod based on material compatibility, joint design, and welding position. Matching rod characteristics with these parameters ensures the integrity of the weld and its long-term performance. Additionally, adhering to manufacturer guidelines for amperage settings and rod manipulation techniques optimizes welding outcomes.
Utilizing the right welding rod not only affects the structural integrity of the project but also enhances efficiency and reduces post-weld clean-up. As industries evolve, welding technology advances, and maintaining a thorough understanding of welding rod types and applications will remain a cornerstone of successful welding projects. This ongoing commitment to expertise and quality assures the reliability of metal constructions, underpinning countless sectors worldwide.