Choosing the right welding rod is crucial when working with dissimilar metals, such as stainless steel and mild steel. While this task presents certain challenges, understanding the intricacies involved can lead to successful, durable welds. Based on extensive experience and technical knowledge, this guide provides insights into selecting and using welding rods for stainless to mild steel applications.
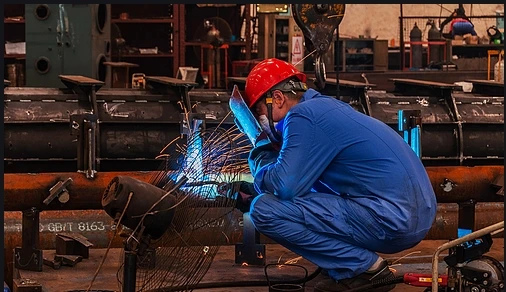
One of the most common challenges faced by welders when working with stainless and mild steel is the difference in their metallurgical compositions. Stainless steel has a higher chromium content, giving it resistance to oxidation and corrosion. Mild steel, on the other hand, is more prone to rust and is softer in nature. Because of these differences, welding these two materials requires a rod that can accommodate the blend of alloys to form a strong joint without causing cracking or weakening.
Professionals often favor 309L welding rods for projects involving stainless to mild steel. The 309L rod is specifically designed for joining 300 series stainless steel such as 304 and 309 to carbon and low-alloy steels. One reason for the popularity of 309L is its higher chromium and nickel content than standard rods, providing a strong, ductile weld designed to maintain integrity in environments where thermal cycling is common. Additionally, its low carbon content minimizes the formation of harmful carbides in the weld area, which can lead to intergranular corrosion.
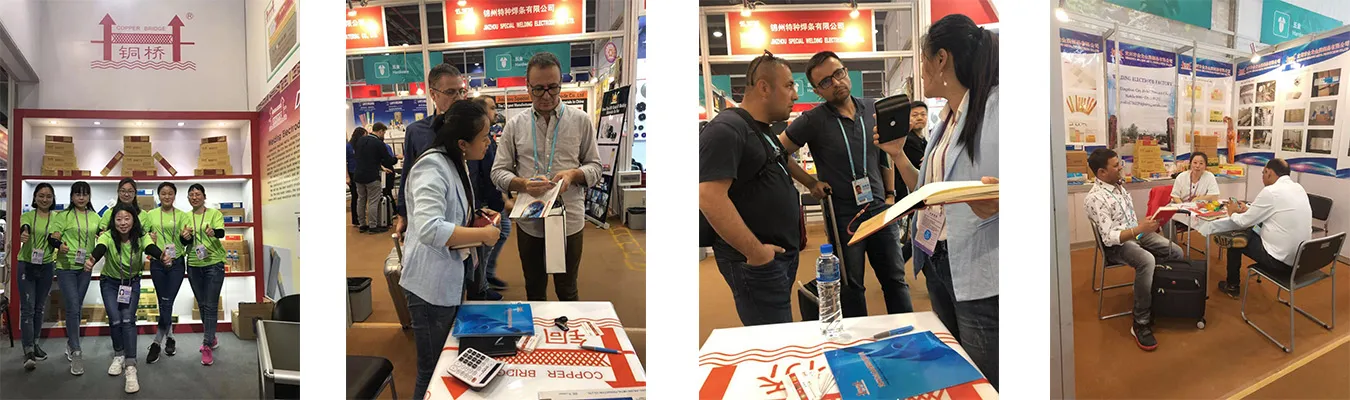
During the welding process, maintaining the appropriate environment is essential. Cleanliness cannot be overemphasized; any contaminants like oil, rust, or paint can lead to defects in the weld. Using a dedicated stainless steel brush or grinder to clean the metal surfaces ensures that no cross-contamination occurs, which can affect weld quality.
Temperature control during the welding process is another critical factor. Mild steel has a higher thermal conductivity compared to stainless steel, meaning it absorbs heat more quickly and can lead to distortion if not carefully managed. Proper heat management is essential to prevent excessive penetration when welding these two types of metals. Preheating the mild steel or post-heating both metals may be necessary depending on their thickness and the specific project requirements.
welding rod for stainless steel to mild steel
The welding technique employed can significantly influence the quality of the weld. A TIG (Tungsten Inert Gas) or MIG (Metal Inert Gas) welding technique is generally recommended over stick welding for these applications due to their precision and control. TIG welding, in particular, provides a cleaner weld with minimal spatter, which is advantageous when working with stainless steel.
Moreover, being well-versed with filler material compatibility gives welders an edge in ensuring the utmost strength and reliability of the joint. While 309L is highly recommended, there are also scenarios where alternative alloys may be better suited. Consulting material safety data sheets and expert guidelines can help in understanding particular environmental demands and ensuring the correct filler is chosen for the specific alloy combination.
Testing and inspection of the weld are critical to verify the strength and longevity of the joint. Non-destructive testing methods such as ultrasonic testing, radiography, or dye penetrant inspection are commonly used to ensure the absence of defects. These methods provide insights into the internal structure of the weld without causing any damage, making them indispensable steps in the quality assurance process for professional projects involving dissimilar metals.
Trusting in reputable brands for welding rods and consumables cannot be understated. Industry-leading brands not only offer consistent quality but also provide in-depth product support, ensuring that users can reliably meet specifications and standards. Continual education and adherence to industry standards ensure that practitioners do not only rely on anecdotal experiences but are backed by authoritative expertise.
When executed correctly, welding stainless steel to mild steel opens opportunities for constructing robust, versatile structures that can withstand a variety of applications. This is especially true in industries like automotive, construction, and manufacturing. By combining practical experience with authoritative technical guidance, welders can produce durable, high-quality welds that stand the test of time, reflecting both skill and precision in their work.