Choosing the right welding rod for joining stainless steel to carbon steel is a crucial step that can significantly impact the integrity of the weld and the longevity of the final product. This process is frequently encountered in various industries, including construction, automotive, and manufacturing, where parts made of different materials need to be welded together. A deep understanding of both materials and expertise in welding processes enhances not only the quality of the weld but also instills confidence in the longevity and safety of the structures involved.
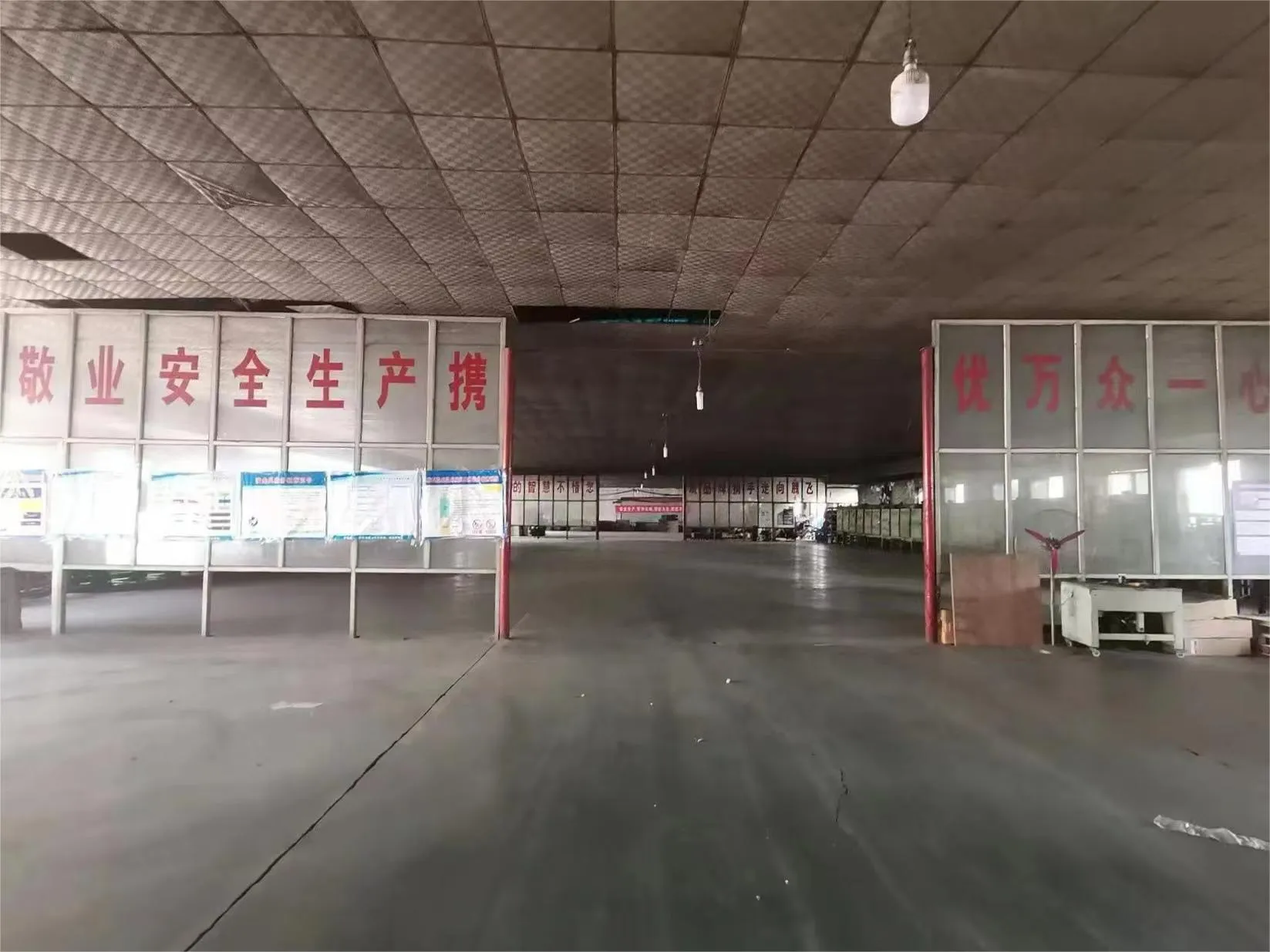
The primary challenge when welding stainless steel to carbon steel lies in the differing metallurgical properties of the two materials. Stainless steel contains chromium, which provides corrosion resistance, while carbon steel is primarily composed of iron and carbon, with less resistance to rust.
The welding rod must accommodate these differences to ensure a strong and durable bond. Among the most recommended choices for this type of joint is the 309L welding rod. Its unique formulation contains elements that help bridge the metallurgical gap, such as higher chromium and nickel contents, making it ideal for dissimilar metal welding.
From the perspective of a seasoned welding expert, several practical considerations should be prioritized to achieve optimal results. Firstly, the prep work is paramount; both surfaces must be meticulously cleaned to remove any contaminants such as oil, rust, or mill scale, which could compromise the weld quality. Using a stainless steel brush for the stainless steel part and a carbon steel brush for the carbon steel part helps avoid cross-contamination, which can lead to defects in the weld.
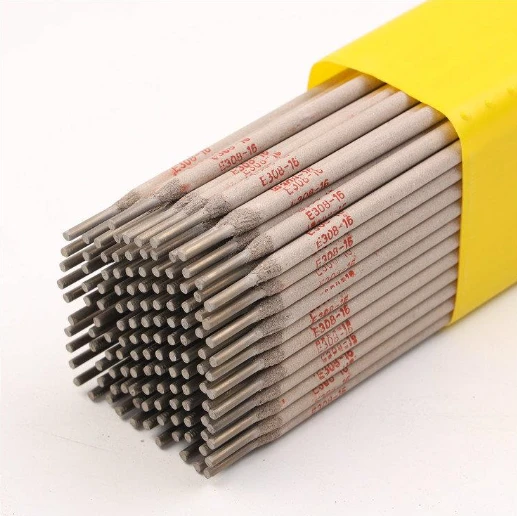
When it comes to executing the weld, understanding heat management is crucial. Carbon steel and stainless steel have different thermal expansion and heat conductivity rates, which can lead to distortion or cracking if not managed properly. Applying the correct heat input, typically lower for stainless steel, and using controlled cooling methods will minimize these risks.
welding rod for stainless to carbon steel
A key area of focus that further displays expertise is the positioning and technique used during welding. Vertical or overhead positions should be avoided when possible, as gravity can cause the weld pool to sag, especially when dealing with the high fluidity of stainless steel. Flat or horizontal positions are recommended for beginners or in critical applications to ensure consistent and high-quality welds.
In addition to traditional welding techniques, advanced processes like laser welding or friction welding can be explored for specific applications. These methods provide precision and minimize the heat affected zone, further enhancing the integrity of the joint. Consulting with welding engineers and experimenting with different techniques can offer new insights and potentially yield superior results.
Authoritativeness in this domain often comes from certification and continuous learning. Certified Welding Inspectors (CWI) and Certified Welders (CW) are highly regarded professionals in the industry, but even they must regularly update their skills to keep pace with new materials and technologies. Participating in workshops, seminars, and online courses is an excellent way to stay informed about the latest advancements and gain a more profound understanding of welding practices.
Finally, trustworthiness is an essential component for any welding project, especially those involving dissimilar metals. Trust is earned through consistent performance, adherence to safety standards, and attention to detail. Ensuring that all welders and technicians are properly trained and that their equipment is regularly maintained reflects a commitment to quality and safety. Documenting each stage of a project and maintaining open communication with clients further reinforces trust, showcasing a dedication to not only expertise but also transparency and accountability in every welding task.