Choosing the right welding rod for joining stainless steel to carbon steel is a critical decision that impacts the integrity and durability of the joint. It requires a blend of experience, expertise, authoritativeness, and trustworthiness to ensure the best results in various applications.
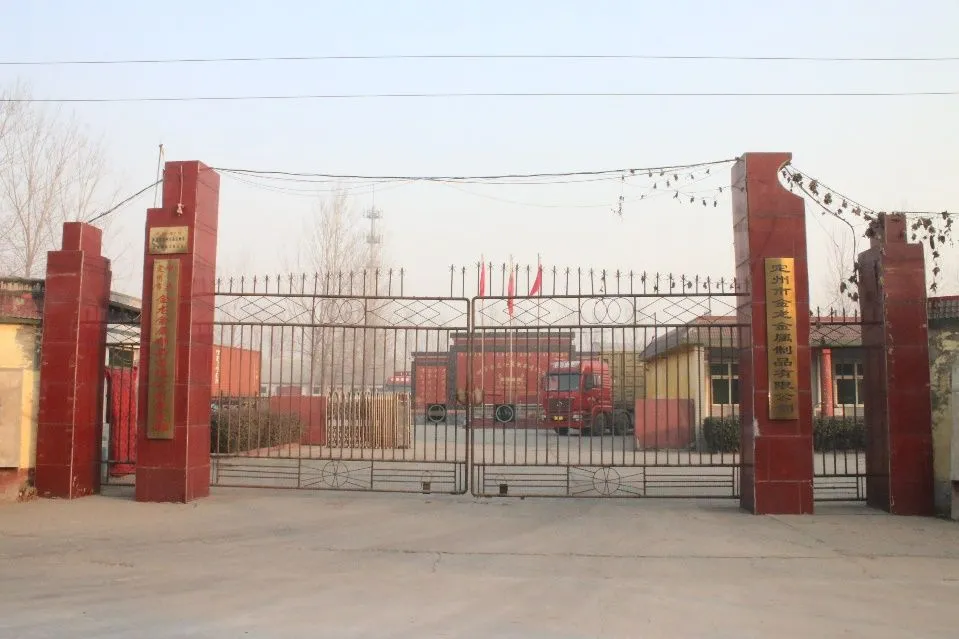
When welding stainless steel to carbon steel, the primary concern is the difference in their compositions. Stainless steel contains chromium, which makes it resistant to corrosion, whereas carbon steel is known for its strength and flexibility. The combination of these two materials necessitates the use of a specialized welding rod, usually an E309 or E309L electrode, which accommodates the differences in expansion rates and thermal conductivity between the metals.
A seasoned welder understands the importance of pre-weld preparation and post-weld treatment. The surfaces should be thoroughly cleaned to eliminate contaminants that could affect the integrity of the weld. Grinding the weld area helps to remove any oxides that may form during the welding process. Additionally, maintaining an appropriate heat input during welding is crucial. The temperature should be controlled to prevent excessive thermal stress and distortion, which can compromise the joint's strength.
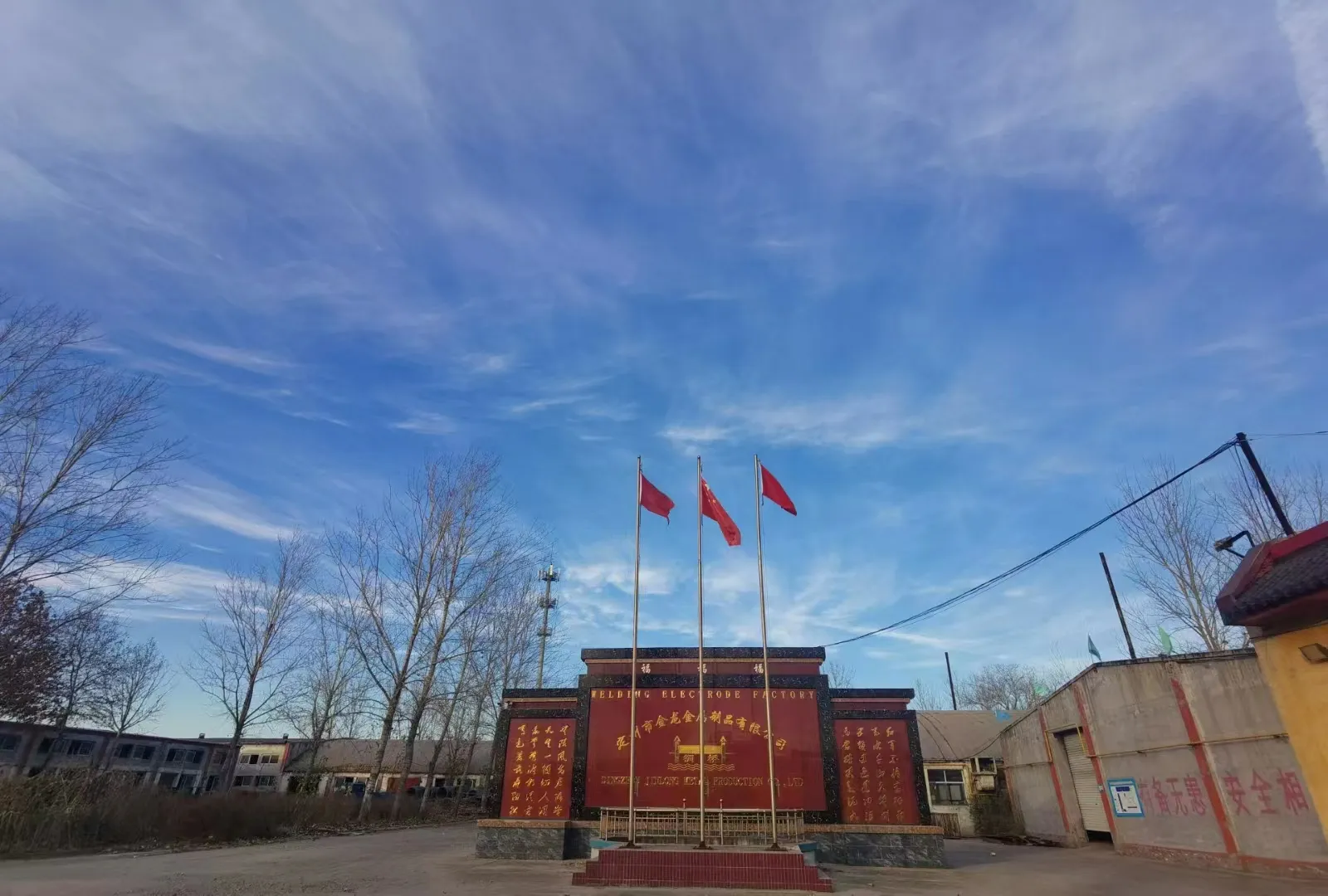
Expertise plays a vital role in selecting the appropriate filler material. E309 and E309L rods are specifically designed for joining dissimilar metals like stainless steel and carbon steel. These rods contain a balanced composition of chromium and nickel that provides excellent tensile strength and corrosion resistance, ensuring a robust and long-lasting weld. Moreover, the low carbon content in E309L reduces the risk of carbide precipitation at the grain boundaries, thereby preventing intergranular corrosion.
welding rod for stainless steel to carbon steel
Authority on this subject comes from years of practical experience and consistent successful outcomes in welding operations. Professionals often test various welding parameters, such as amperage settings and travel speed, to optimize weld quality. They rely on established standards and guidelines from authoritative bodies like the American Welding Society (AWS) which provides detailed specifications for welding dissimilar metals.
Trust is built through proven reliability and consistent performance. Welders who follow these best practices demonstrate an understanding of both the materials and the processes involved. They often engage in continuous education and certification programs to stay updated with the latest advancements in welding technology and techniques.
Safety is paramount in welding operations. Welding fumes and sparks pose significant health risks, so wearing appropriate personal protective equipment (PPE) like helmets, gloves, and flame-resistant clothing is essential. Employing effective ventilation systems mitigates fume exposure, ensuring a safe working environment.
In conclusion, the union of stainless steel and carbon steel using the correct welding rod requires a comprehensive understanding of metallurgy and welding principles. It is not merely a technical task but an art that balances science with practical know-how. By adhering to industry standards, leveraging specialized materials like E309 or E309L, and following stringent safety protocols, welders craft durable, high-integrity joints that stand the test of time. This approach not only highlights their expertise and authority but also builds trust with clients and stakeholders.