Choosing the right welding rod for stainless steel can make the difference between a lasting weld and one that fails prematurely. In the world of welding, where every component tends to have specific requirements, understanding the nuances can transform a seemingly daunting task into a routine operation. This article delves into the experience, expertise, authoritativeness, and trustworthiness surrounding stainless steel welding rods.
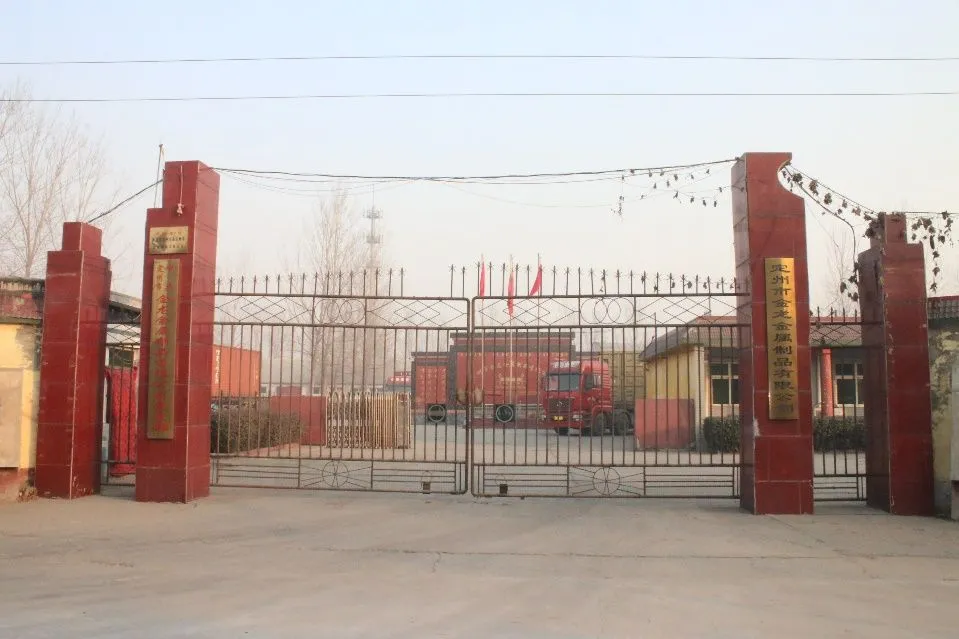
Welding rods, often referred to as filler metals, are a critical component in the welding process. Selecting the appropriate rod for stainless steel involves considering various factors such as the type of stainless steel, its application, and the required properties of the weld.
Primarily, stainless steel rods are categorized by their alloy type. The most common types include 308, 309, and 316. Each type offers distinctive characteristics that influence their suitability for various applications. For instance, the 308 welding rod is mainly used for austenitic stainless steel of the 300 series, including 304, which is known for its excellent corrosion resistance and formability. On the other hand, the 309 rod is often used for welding dissimilar metals, like joining stainless steel to carbon steel, due to its superior compatibility and resilience under thermal stress.
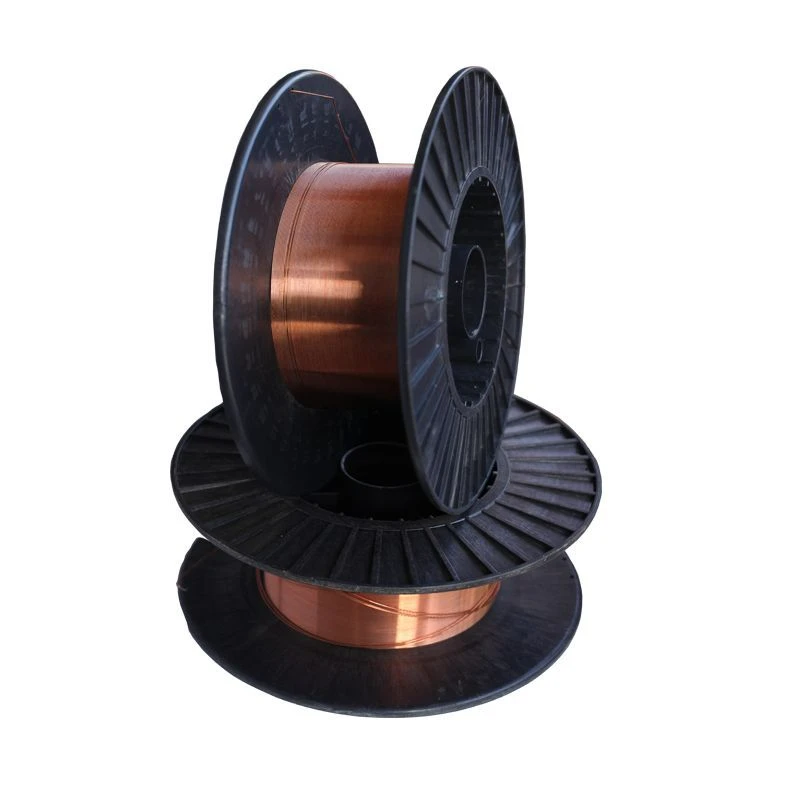
Choosing the correct welding rod also means understanding the welding environment. Factors such as temperature fluctuations, potential for exposure to corrosive elements, and mechanical stress all play crucial roles. Take for example the 316 welding rod which contains molybdenum, enhancing its ability to withstand severe corrosion in harsher environments like marine applications. This makes it an indispensable choice for projects involving chemical processing equipment or coastal infrastructure.
The success of a weld is not just attributed to the choice of the welding rod but also to the experience and technique of the welder. Expertise in welding stainless steel involves understanding its thermal expansion, which is greater than that of carbon steel. This requires welders to adopt strategies to manage distortion and avoid warping. Proper heat control, combined with selecting a compatible filler metal, ensures a high-quality weld.
welding rod for ss
Trust in a brand of welding products can be established through years of consistent performance and compliance with industry standards. For instance, companies that provide detailed data sheets and adhere to AWS (American Welding Society) specifications often enjoy higher credibility. Additionally, their products undergo rigorous testing to verify their performance under specific conditions, assuring users of their reliability.
In the realm of welding, a professional's authoritativeness is often demonstrated through certifications and continued education. Welders with AWS certification or those who participate in continuous learning opportunities are better equipped to make informed decisions about materials and techniques. This focus on education not only refines a welder's skill set but also builds a foundation of trust with clients and employers.
Finally,
the welding community thrives on shared experiences. Online forums, trade shows, and workshops serve as platforms where professionals exchange insights and developments in the field. Engaging with these communities not only enhances one's expertise but also builds a network of trust and collaboration.
In sum, selecting the right welding rod for stainless steel transcends beyond a mere purchase. It is an intricate process that involves a deep understanding of the material, welding techniques, and the broader environmental context. Whether for industrial manufacturers or artisan metalworkers, mastering these elements is crucial in ensuring strong, lasting welds that withstand the test of time.