When navigating the complex marketplace of welding electrodes, price plays a crucial role in decision-making for both individual buyers and large industrial operations. Understanding the factors that influence the cost of welding electrodes can empower you to make informed purchasing decisions, ensuring quality and enhancing your project outcomes.
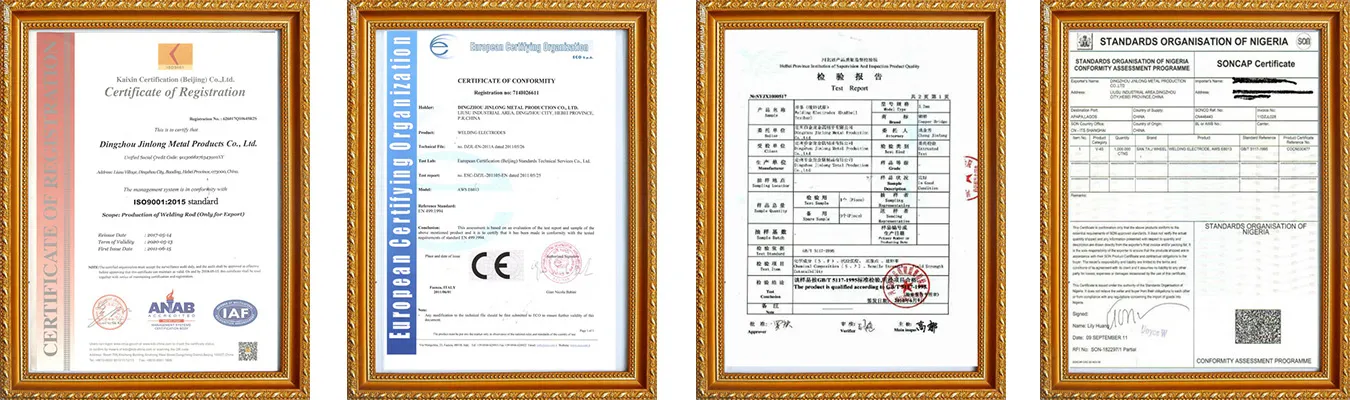
The price of welding electrodes is subject to several factors, including material composition, manufacturing process, brand reputation, and the specific application for which they are designed. High-quality welding electrodes, such as those made from premium alloys, tend to command higher prices due to their superior performance and longevity. These electrodes deliver cleaner welds with fewer failures, making them a cost-effective choice for critical applications where failure is not an option.
Materials form the foundation of welding electrode costs. Electrodes composed of specialty alloys, like stainless steel, nickel, or aluminum, will often be priced higher than standard carbon steel electrodes. This is due to the complex extraction and refinement processes involved in producing these materials, as well as their rarity. For industries requiring precise and reliable welds, the initial investment in higher-grade electrodes can mean the difference between project success and costly downtime.
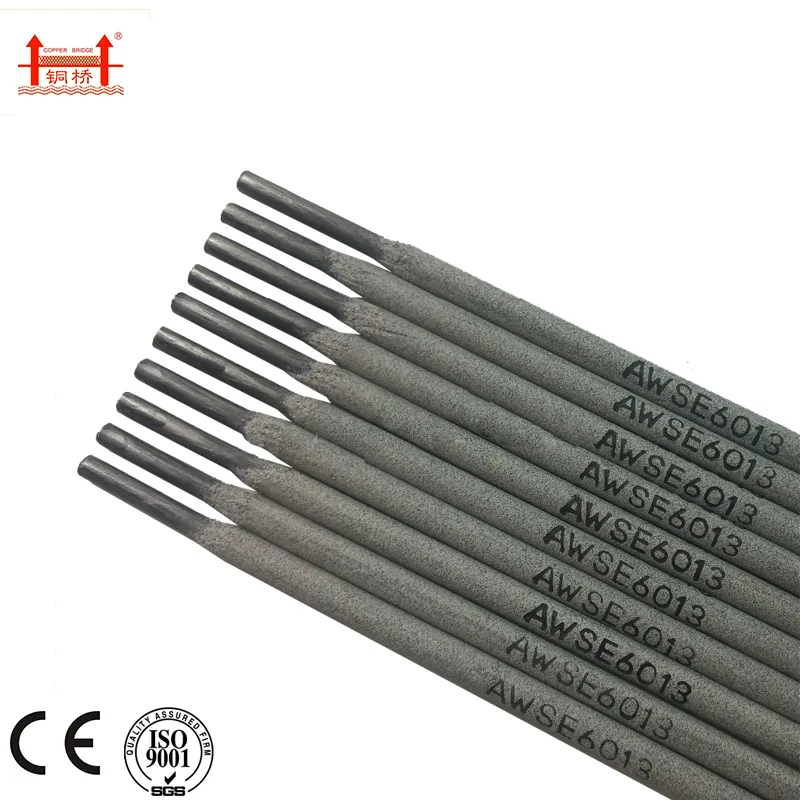
Manufacturing processes also play a significant part in determining welding electrode prices. Advanced production techniques that ensure uniform coating thickness, consistent chemical composition, and superior mechanical properties can result in more reliable products that naturally demand a premium. Investing in such high-quality electrodes might appear costly upfront, but they often represent long-term savings by reducing consumable waste and improving work efficiency.
Brand reputation is another influential factor. Renowned manufacturers with a history of delivering high-quality welding products generally command higher prices. Their electrodes are typically subjected to rigorous testing and quality control checks, ensuring they meet or exceed industry standards. Such brands also provide comprehensive customer support and technical assistance, bolstering their offer with authority and trustworthiness.
welding electrode price list
Moreover, the application-specific nature of welding electrodes means that their prices can vary dramatically depending on the intended use. Electrodes designed for specific metals, environments, or welding techniques may be priced higher due to their tailored properties. For instance, electrodes with enhanced moisture resistance are essential for projects in high-humidity environments, justifying their higher cost through improved functionality and reliability.
When building a welding electrode price list, transparency about these factors is crucial. Providing detailed information about the composition, manufacturing process, and typical applications for each product lends authority to your offerings and builds trust with potential buyers.
To navigate pricing strategically, consider consulting welding experts and engaging industry forums. Leveraging professional expertise helps to ensure that you not only select the right electrodes for your project needs but also receive competitive pricing. Such interactions not only enhance your understanding of market trends but also allow you to establish a network of trusted suppliers who can provide ongoing advice and support.
Ultimately, the cost of welding electrodes is an investment in the quality of your work. By prioritizing expertise and reliability over short-term cost savings, you position yourself as a knowledgeable and authoritative figure in your industry, capable of delivering superior results that meet client expectations and project specifications.