Navigating the world of welding rods can be a daunting task for both novices and seasoned welding professionals. With a variety of welding rod types available, each designed to cater to specific welding needs and material requirements, understanding their uses is essential for ensuring welding success and quality craftsmanship.
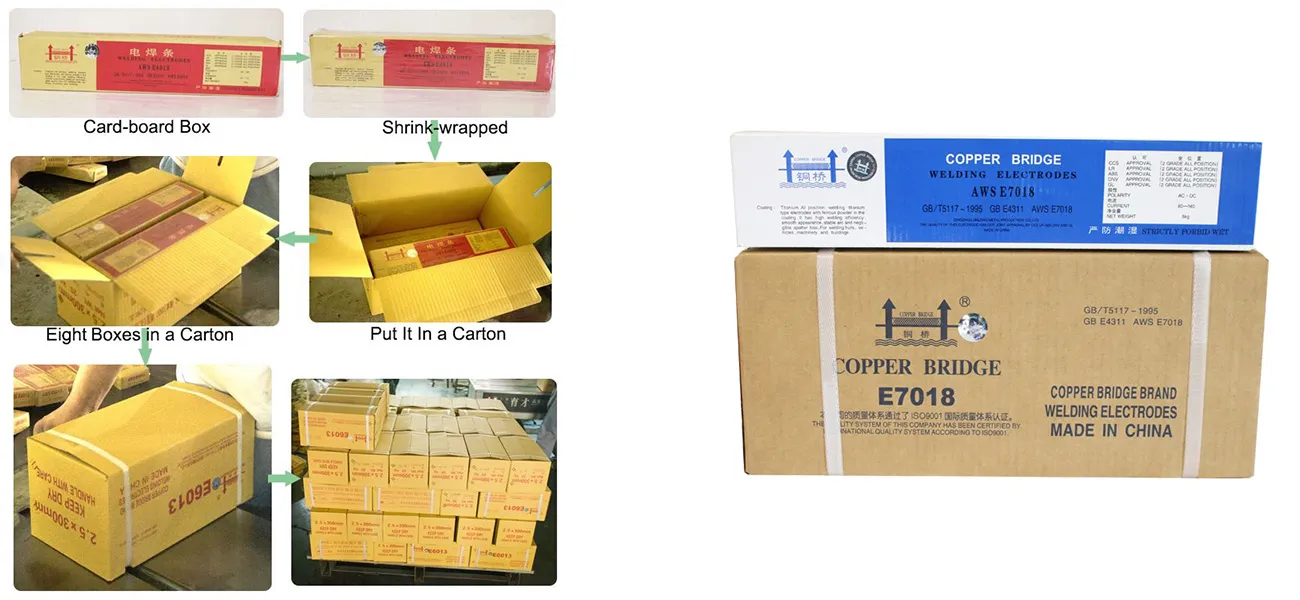
Welding rods, also known as filler metals, serve as an indispensable part of the arc welding process. The choice of welding rod can drastically affect the strength, durability, and appearance of the weld. Here is a comprehensive guide to the types and uses of welding rods, intended to enhance both your expertise and practical experience.
1. Consumable Electrodes
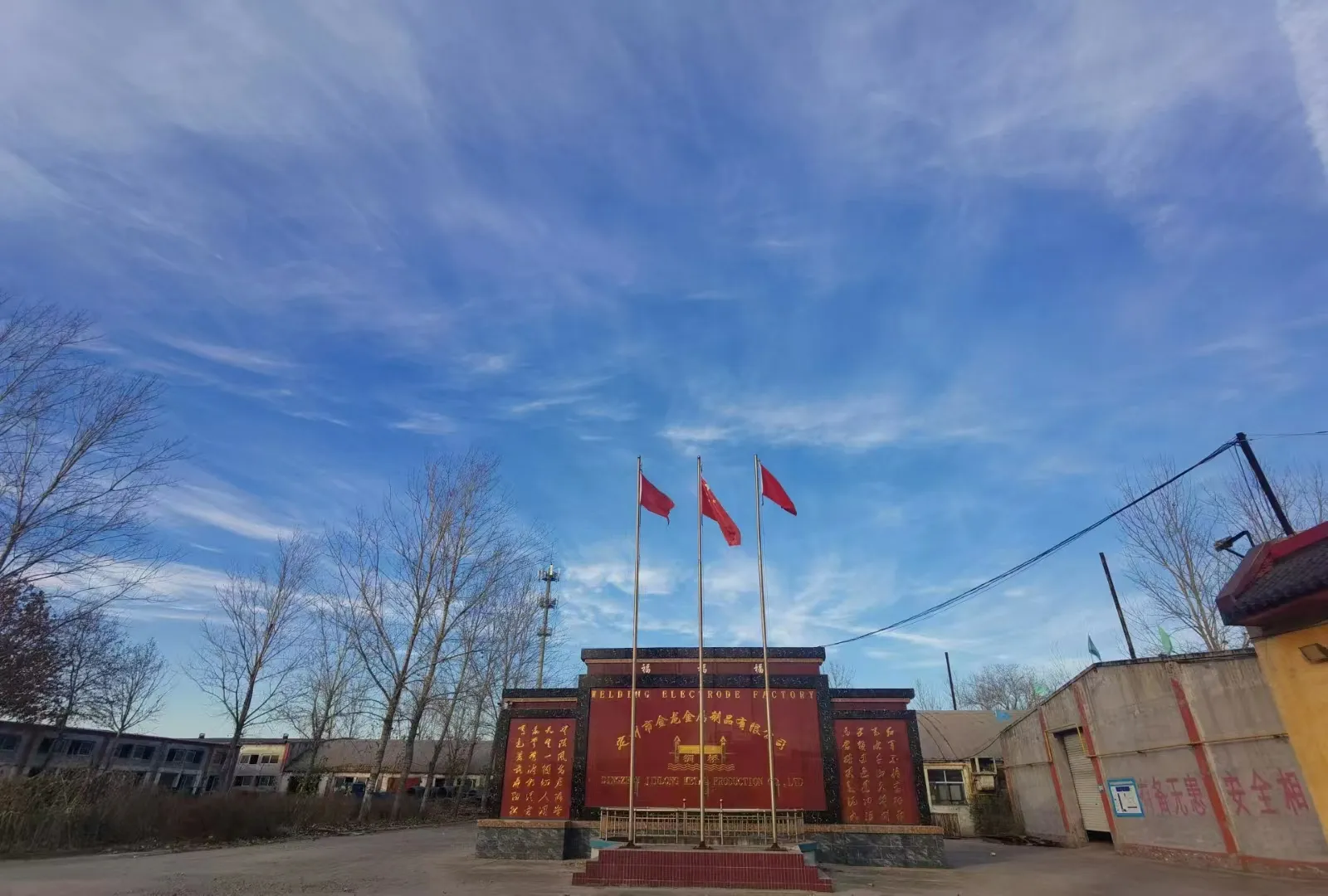
These are the most commonly used welding rods and include a protective coating. They melt alongside the base material, contributing to the weld pool. Consumable electrodes come in different types such as E6010, E6011, E6013, E7018, each having unique properties and suited for various welding conditions.
- E6010 and E6011 Known for deep penetration capabilities, they are ideal for welding in difficult positions and for working with dirty or oxidized metals. These rods are frequently used in pipeline work and for repairing heavy equipment.
- E6013 A general-purpose welding rod, E6013 is user-friendly and provides a smooth, stable arc, producing welds with a neat finish. It is perfect for beginners or for applications where appearance is critical.
- E7018 This low-hydrogen electrode is prized for its tensile strength and ductility. It is commonly used in structural welding applications like bridges and skyscrapers due to its ability to produce strong, crack-resistant welds.
2. Non-Consumable Electrodes
welding rod types and uses pdf
Utilized chiefly in Tungsten Inert Gas (TIG) welding, non-consumable electrodes do not melt during the welding process. Instead, they provide a stable arc and are used with a separate filler material.
- Tungsten Electrodes Tungsten is known for its high melting point and current-carrying capacity. A variety of tungsten electrodes are available, such as Thoriated, Ceriated, and Lanthanated, each offering benefits like easier arc starting or improved arc stability. These rods are essential for precision work, especially in aerospace or automotive industries where clean, controlled welds are critical.
3. Specialty Welding Rods
There are specific rods designed for unique applications or materials. Nickel and stainless steel rods fall into this category, used primarily for welding non-ferrous metals or dissimilar metals.
- Nickel Electrodes These are used for welding nickel alloys and cast iron, often found in marine environments or chemical plants where corrosion resistance is paramount.
- Stainless Steel Electrodes These rods are utilized for welding stainless steel materials, providing excellent corrosion resistance which is crucial in food processing, medical equipment, and environments exposed to the elements.
Understanding which welding rod to select is critical for optimizing welding performance, minimizing defects, and ensuring the longevity of the structures being built or repaired. Mastering the use of the different rods not only elevates the quality of your welds but also enhances your reputation in the field as a knowledgeable and capable welding professional. Whether you are spearheading a large-scale construction project or undertaking intricate repair work, the correct choice of welding rods is the bedrock of creating durable and reliable welds.