Choosing the right welding electrode size is a crucial process that directly affects the quality and performance of a welding project. As seasoned welding professionals understand, electrode size is not merely a matter of preference but is influenced by several critical factors, including the thickness of the material, the type of joint, and the specific welding conditions.
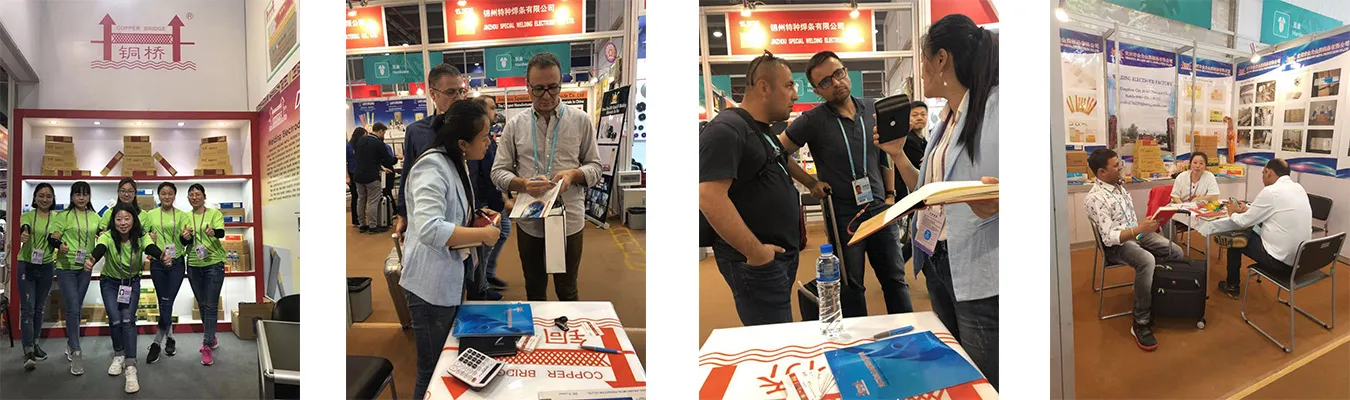
The electrode’s diameter dictates the depth of penetration and the weld's overall integrity. For example, smaller electrodes, typically ranging from 1/16 inch to 3/32 inch, are ideal for welding thin materials. This is because smaller electrodes provide a finer control over the welding process with minimal heat input, reducing the risk of burn-through on delicate materials. This makes them especially suitable for intricate automotive and thin sheet metal repairs.
Conversely, larger electrodes, measuring up to 5/32 inch or more, are required for heavy-duty applications involving thick metal plates. The increased diameter provides a larger arc and deeper penetration, which is essential for achieving the strong, durable joints necessary in construction and structural projects. The expertise of the welder also plays a significant role in electrode selection; skilled welders often experiment with electrode sizes based on the specific demands of the project at hand, balancing between penetration and finesse.
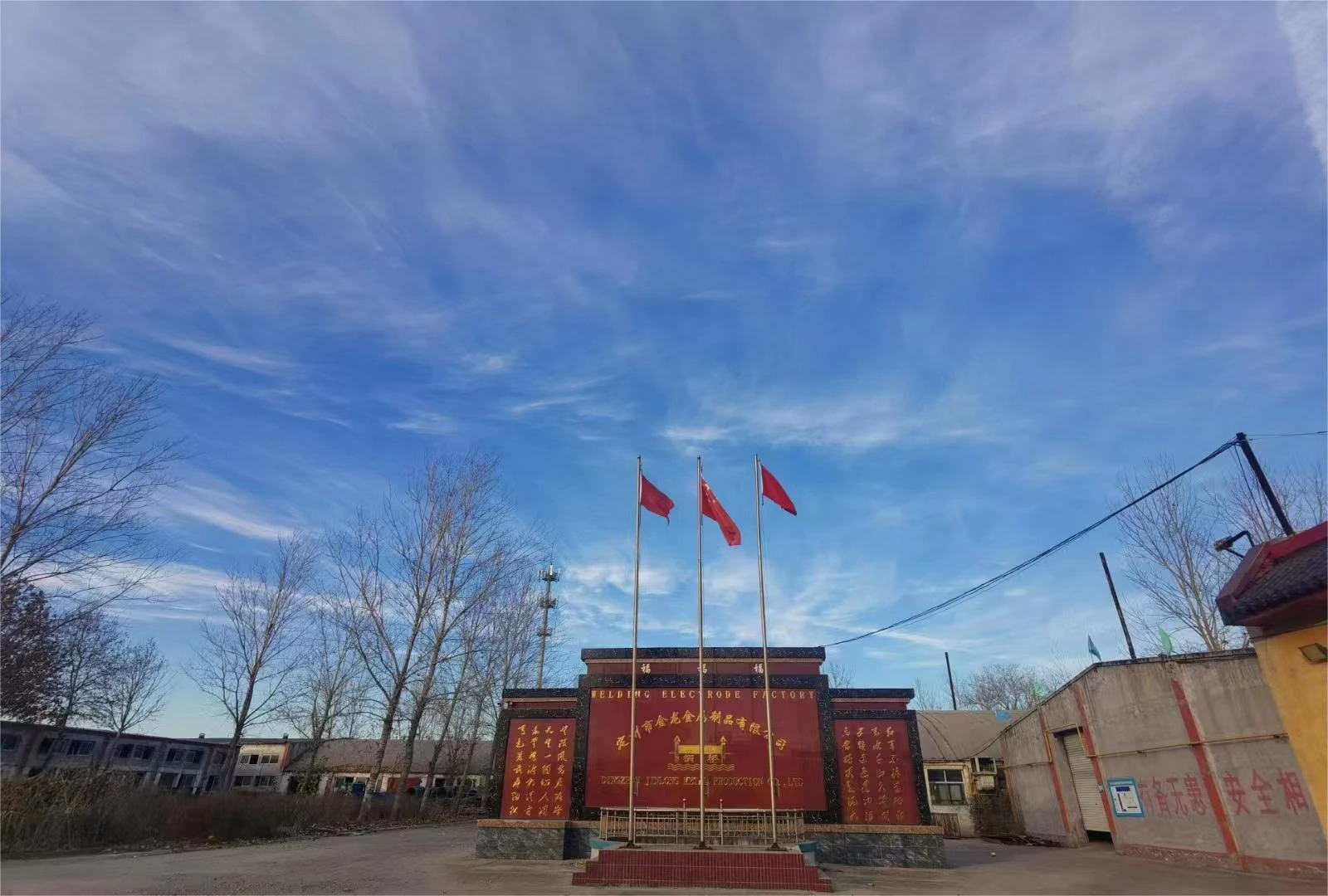
Material type is another factor that must be considered. For example, while stainless steel demands electrodes like the E308 or E316 series, aluminum requires a very different approach, often utilizing tungsten electrodes in TIG welding for precision. Each material reacts differently to heat and welding procedures, highlighting the importance of selecting an electrode that augments the material’s properties rather than detracting from them.
welding electrode size selection
Additionally, joint configuration and welding position can impact electrode size choice. Out of position welds, such as vertical or overhead positions, benefit from smaller electrodes which are easier to control, reducing spatter and improving arc stability. For flat or horizontal joints, where gravity isn’t as much of a concern, larger electrodes can cover more area efficiently, enhancing productivity without compromising on weld quality.
The welding current is another critical element determined by electrode size. Lower currents are suited for thinner electrodes, while higher currents pair with larger electrodes for optimal performance. There needs to be a balance between the amperage and electrode size to avoid common welding defects such as excessive spatter or undercut.
For those in professional welding, understanding the symbiotic relationship between electrode size and these variables is imperative. Not only does it ensure sound and aesthetically pleasing welds, but it embodies the expertise and trustworthiness that clients seek in any welding endeavor. Ensuring correct electrode size selection is not only about achieving a structurally sound weld but also exemplifies a commitment to quality and excellence.
Ultimately, while technological advancements continuously shape the welding field, the fundamental principles of electrode size selection remain unchanged. It is the mastery of these principles that defines expertise in welding, solidifying a welder's reputation as an authoritative and trusted professional in the field.