When it comes to TIG welding mild steel using a stainless steel rod, there are several nuanced details and professional insights to consider in order to achieve optimal results. TIG welding, or Tungsten Inert Gas welding, is renowned for its precision and high-quality welds. It is a technique that requires skill and a solid understanding of the materials involved, particularly when working with dissimilar metals like mild steel and stainless steel.
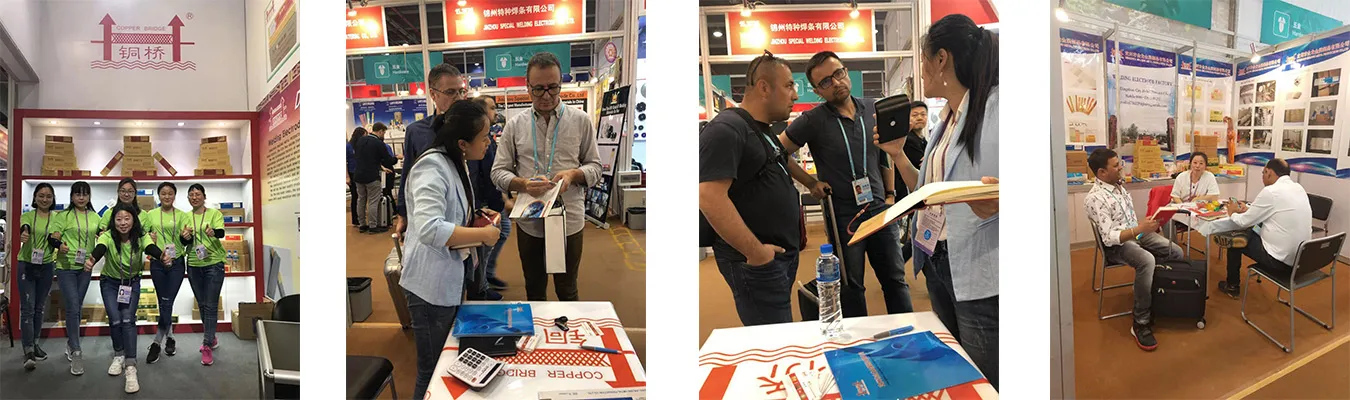
A significant benefit of using a stainless steel rod to weld mild steel lies in the properties that stainless steel brings to the weld joint. Stainless steel rods, typically austenitic alloys like ER308L or ER309L, provide superior strength and corrosion resistance compared to mild steel filler rods. This makes them an excellent choice for projects where durability, aesthetics, and resistance to environmental factors are crucial.
From an expertise standpoint, selecting the right rod is essential. ER309L is often preferred because it is specifically designed for joining dissimilar metals like stainless steel to mild steel. Its higher levels of chromium and nickel facilitate a strong bond and enhanced resistance to corrosion. This selection is crucial when the finished product will be exposed to elements that could lead to rust or degradation over time.
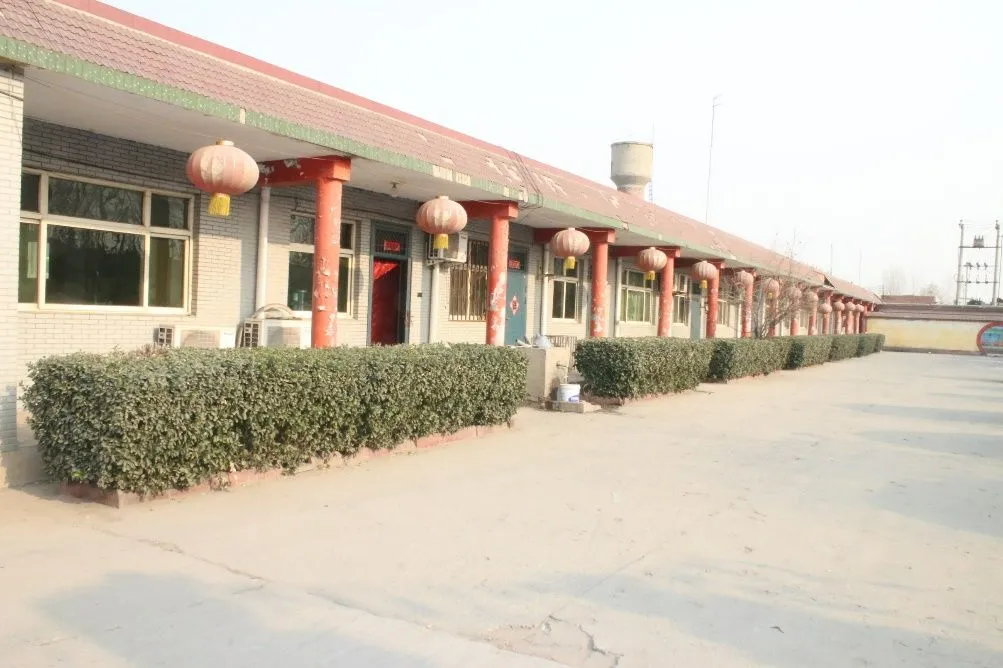
Preparation of the materials is equally important. Thoroughly clean the mild steel surface before welding, as any contaminants can significantly interfere with the quality of the weld. Use a stainless steel brush to clean the surface to avoid cross-contamination. Edge preparation is also vital to ensure a strong weld; chamfer the edges appropriately and ensure a tight fit to facilitate deep penetration of the weld.
tig welding mild steel with stainless rod
Heat control is an aspect that underscores both expertise and trustworthiness in the TIG welding process. Mild steel and stainless steel conduct heat differently; mild steel tends to warp if exposed to too much heat, while stainless steel can suffer from carbide precipitation.
Adjusting the welder settings to accommodate these differences is crucial. Employ a lower amperage than you might typically use for mild steel to maintain control over the heat-affected zone and reduce the risk of distorting the base materials.
Positioning the weld correctly is important to maintain integrity. Use a back-purge of argon gas, especially if full penetration welds are necessary. This prevents oxidation on the underside of the weld, ensuring no weaknesses compromise the joint's quality. A precise and steady hand is needed to guide the tungsten electrode accurately, ensuring it doesn’t make contact with the weld pool, which can introduce contaminants and weaken the weld.
Finally, testing the strength and quality of the weld is non-negotiable. Conducting destructive tests on practice joints can reveal imperfections and provide insights into adjustments that need to be made. This process not only improves the individual's skills but also ensures the reliability and safety of the welded structure.
By approaching TIG welding of mild steel with a stainless steel rod with these considerations in mind, an authoritative and trusted craftsmanship can be achieved, extending the lifespan and performance of the welded joint. This knowledge positions you as an expert in the field, capable of delivering superior welding solutions with a deep understanding of both the materials and the technical requirements involved.