TIG welding, known as Tungsten Inert Gas welding, is an intricate process cherished for its precision and ability to produce high-quality welds. Specifically, welding 1.6 mm stainless steel presents unique challenges that, when properly addressed, yield superior results. The process requires a steadfast hand, keen attention to details, and a deep understanding of both the materials and the tools involved. This guide ventures into the experience, expertise, authoritativeness, and trustworthiness needed to master TIG welding of this thin and versatile metal.
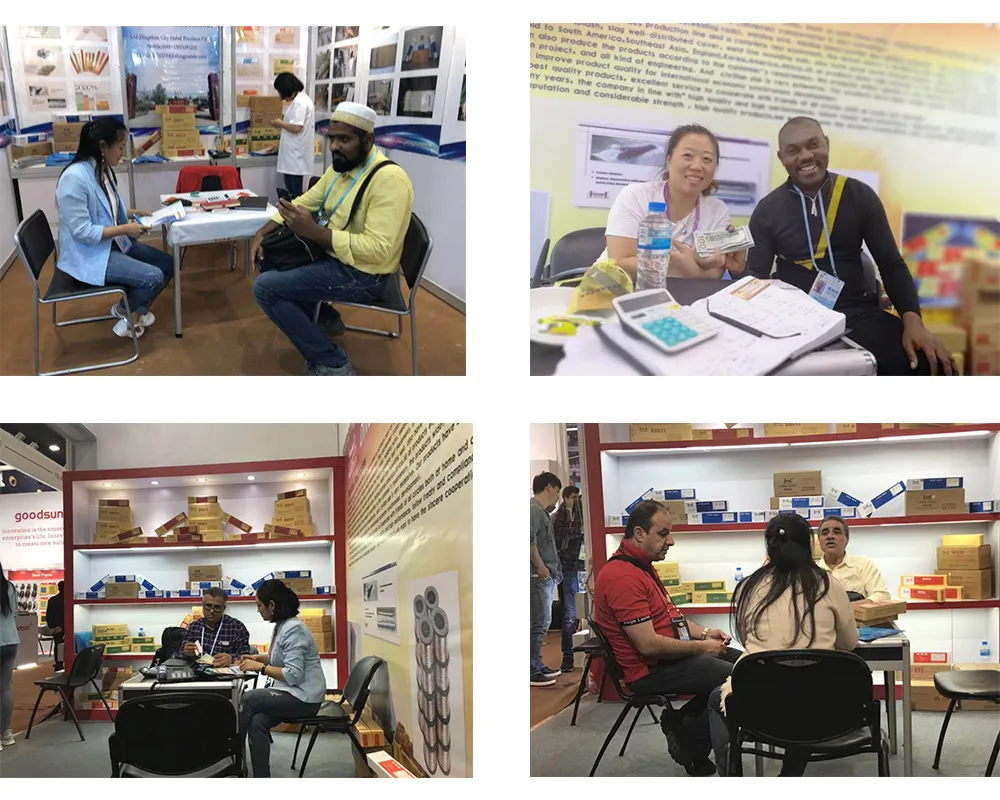
Experience Welding 1.6 mm stainless steel necessitates hands-on experience with TIG welding techniques. Stainless steel is prized for its corrosion resistance and strength, attributes that stem from its specific alloy composition, primarily chromium. Yet, these same strengths pose challenges during welding. The thinness of 1.6 mm stock requires the welder to be adept at controlling heat input to avoid burn-through. Experience teaches that a low amperage setting, typically ranging from 30 to 70 amps depending on the specific alloy and joint type, is essential for maintaining the integrity of the stainless steel without compromising its structural properties.
Expertise Mastery of TIG welding on 1.6 mm stainless steel includes understanding the importance of the tungsten electrode's preparation. Precision welding demands a sharp, consistent tungsten tip which ensures a stable arc and minimizes weld contamination.
Selecting the correct tungsten, usually a 1.0 or 1.6 mm diameter thoriated or ceriated tungsten, ensures stability in the arc. Maintaining a short arc length helps in focusing the heat on the weld puddle, reducing the chances of warping this thin material. Mastery also involves gas selections, such as the use of pure argon or an argon-helium mix, to enhance arc characteristics and weld pool stability.
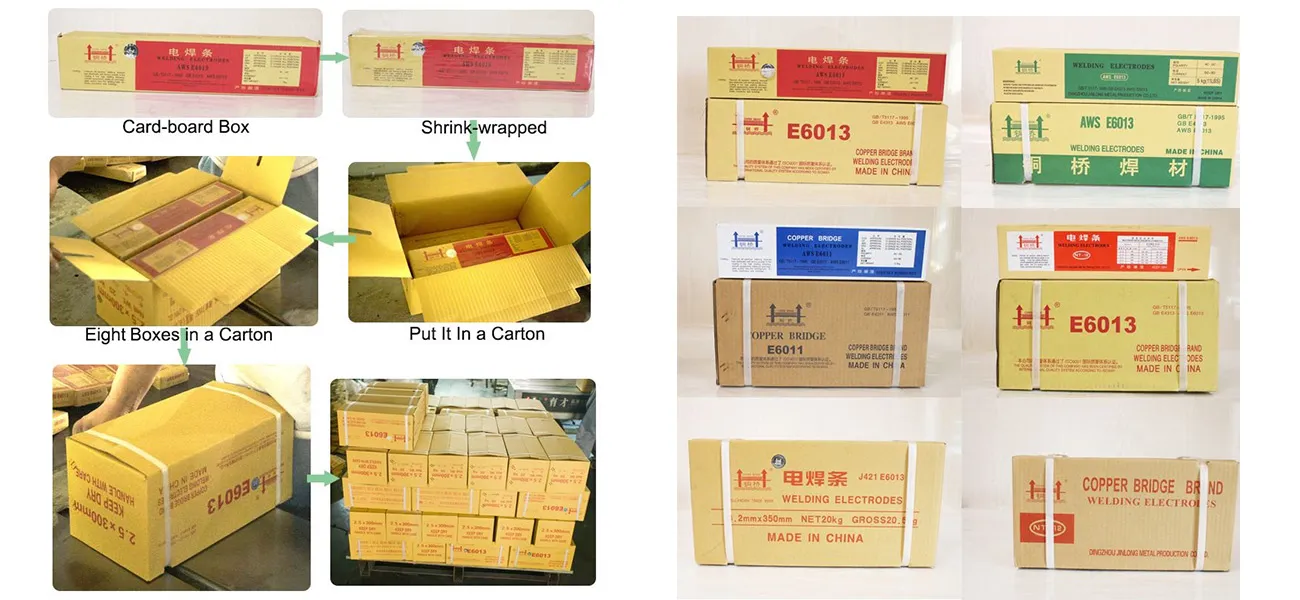
tig welding 1.6 mm stainless steel
Authoritativeness Being an authoritative figure in TIG welding goes beyond technique; it involves understanding and addressing potential defects and issues that could arise during the welding of stainless steel. To this end, maintaining a clean work environment is pivotal, as any contamination could severely compromise a weld. Brush and clean the metal surfaces thoroughly before beginning any weld to mitigate the risk of inclusions. Additionally, understanding the nuances of post-weld treatments, such as passivation or pickling, ensures the longevity of the weld and preserves the inherent corrosion resistance of stainless steel. Guidance on these aspects from industry leaders and technical data sheets provides invaluable insights and establishes authority in practices.
Trustworthiness Ensuring consistent quality in TIG welding involves fostering trust through methodical and repeatable processes. This includes calibration and regular maintenance of equipment, such as TIG torch components, power sources, and gas cylinders. Welding tests on scrap pieces can simulate real weld conditions, providing insight into weld behaviors and allowing the practitioner to adjust techniques for optimal outputs. Validating these adjustments through non-destructive testing (NDT) methods such as dye penetrant tests sustains trust in weld quality, offering transparency and reliability to clients or project stakeholders.
From execution to evaluation, welding 1.6 mm stainless steel is both an art and a science, demanding credible strategies to ensure flawless results. Incorporating these principles of experience, expertise, authoritativeness, and trustworthiness solidifies an exceptional foundation. The goal is not only a seamless weld but the proliferation of knowledge and practice that meets and exceeds industry standards. Such caliber in craftsmanship and process is what separates seasoned practitioners from novices and sets a benchmark for excellence in the delicate art of TIG welding thin stainless steel.