TIG welding, short for Tungsten Inert Gas welding, is a highly precise technique employed by professionals and hobbyists alike to weld a variety of metals, including 1/16 inch stainless steel. The finesse required to successfully TIG weld thin stainless steel sheets makes the process both an art and a science. Its complexity and specificity underscore the need for expertise, experience, and precise equipment.
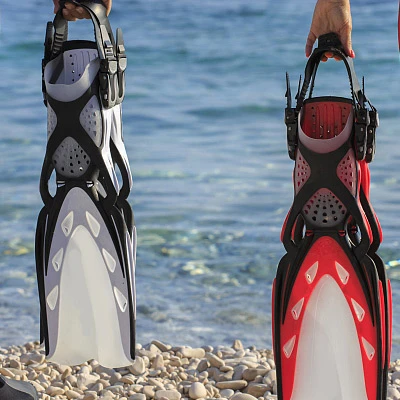
To begin with, choosing the right equipment is crucial for TIG welding 1/16-inch stainless steel. The welder must utilize a well-calibrated TIG welding machine capable of providing stable and consistent power output. The choice of tungsten electrode plays a critical role; a 1/16 inch lanthanated tungsten electrode generally offers a good balance between versatility and precision for welding thinner metals. The selected tungsten should be sharpened to a fine point to enable a concentrated arc, which is essential for preventing burn-through on thin metal pieces.
Shielding gas is another pivotal component in the TIG welding process. Argon is often the gas of choice due to its excellent shielding properties, which protect the weld area from oxidation and contaminants. For welding stainless steel, it's advisable to use pure argon or a mixture containing a small percentage of hydrogen for deeper penetration and cleaner welds. The flow rate should be optimally set between 10-20 CFH (cubic feet per hour), proportional to the environmental conditions and the specifics of the welding task.
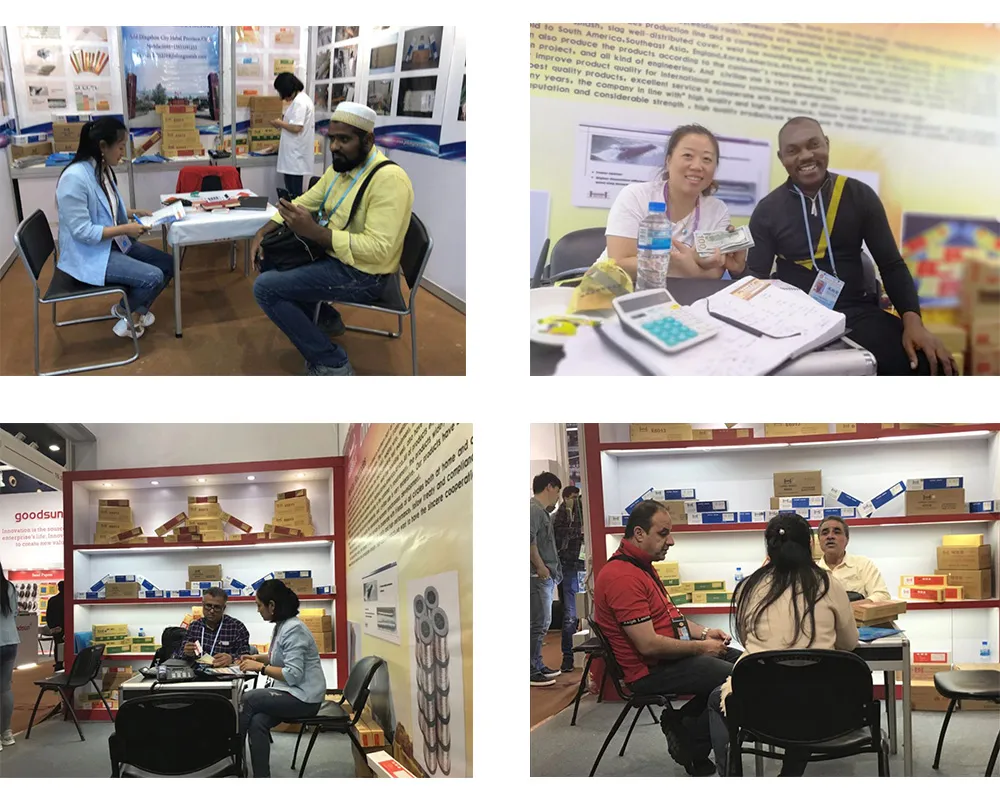
A key factor to a successful weld is the preparation of the stainless steel surface. Cleaning the metal thoroughly with a stainless steel brush or a dedicated acetone solution removes any oxides, oils, or impurities that could undermine weld integrity. Even though stainless steel is corrosion-resistant, these contaminants can still interfere with your weld, leading to issues such as porosity or weak weld joints.
The technique itself requires a steady hand and keen attention to detail.
TIG welding 1/16 inch stainless steel demands precise control over heat input. A pulsed current can be beneficial, allowing for controllable bursts of heat to prevent warping or burn-through while maintaining proper fusion. The welder’s skill in adjusting the amperage and travel speed in response to these pulses is paramount. A typical starting point for amperage is around 40-60 amps, but this can vary based on joint configuration and specific project requirements.
tig welding 1 16 stainless steel
Practicing correct technique is crucial for achieving strong, clean welds. Begin with tacking the metal pieces together at intervals to stabilize the work. This ensures that the parts do not move out of alignment before the main welding starts. Maintaining the right angle between the electrode and the work piece, typically around 15 to 20 degrees, helps direct the heat effectively onto the weld joint. Moreover, maintaining a consistent travel speed ensures even heat distribution and a smoother weld bead.
Another component not to overlook is post-weld finishing. After completing the weld, any discoloration or surface oxides should be removed, often with a stainless wire brush or chemical cleaning agents specifically designed for stainless steel. This not only enhances the aesthetic appearance of the weld but also helps in preventing future corrosion.
Safety cannot be overstated in the realm of TIG welding. Keeping a fire extinguisher nearby, wearing appropriate safety gear such as gloves, a welding helmet with adequate shading, and protective clothing can lessen risks associated with ultraviolet radiation and other hazards inherent to welding processes.
From equipment selection, preparation, to actual technique and finishing, TIG welding 1/16 inch stainless steel is a task that demands precision, patience, and expertise. Professionals and hobbyists alike must strive to refine their skills continuously, keeping abreast of the latest technologies and methods through online resources, workshops, and collaboration within the welding community. With a strong foundation and a dedication to mastering the craft, achieving perfect welds on thin stainless steel becomes an attainable and rewarding pursuit.