Welding mild steel with a stainless steel rod is a task that often raises questions about the suitability and outcome of such a process. As someone with extensive experience and expertise in the field of welding, I can provide valuable insights into the intricacies and considerations involved, ensuring you understand both the practical and theoretical aspects of this technique.
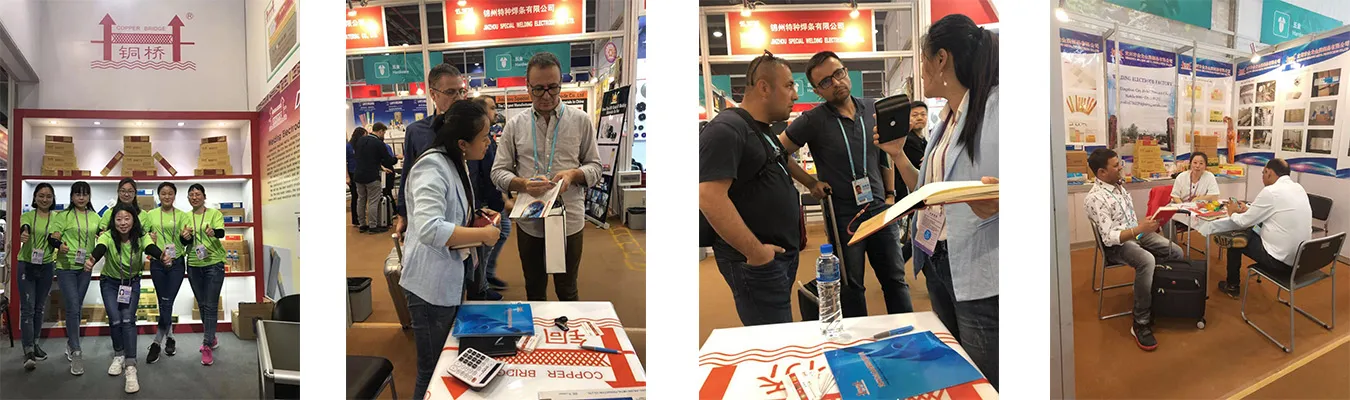
When it comes to welding different metals, understanding the properties of your materials is crucial. Mild steel, known for its malleability and ease of welding, is a low-carbon steel that forms the backbone of numerous structures. Stainless steel, on the other hand, is appreciated for its corrosion resistance and strength, thanks to its chromium content. The challenge arises in achieving a joint that takes advantage of the properties of both metals while avoiding the introduction of unwanted weaknesses.
Using a stainless steel rod to weld mild steel requires meticulous attention to detail, starting with the choice of filler. The most commonly used rod for such tasks is the 309L type, known for its compatibility and ability to form strong joints between dissimilar metals. The 309L welding rod is specifically formulated to prevent the intergranular corrosion that can occur when joining stainless steel to mild steel, owing to its balanced chromium and nickel content.
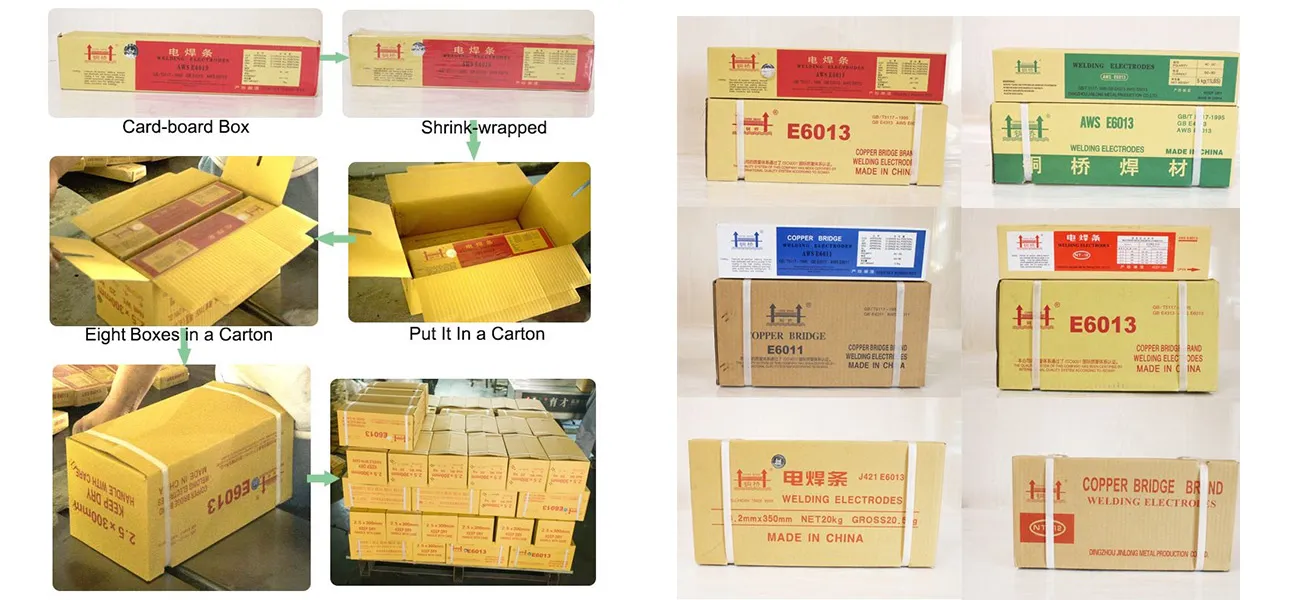
Preparation is pivotal in achieving a successful weld.
Ensure that both the mild steel and the stainless rod are clean and free of contaminants. This involves thorough cleaning using a grinder or brush to remove any rust, oil, or scale. Proper alignment and securing of materials ensure minimal distortion during welding, a common issue given the differing expansion rates of mild and stainless steel.
Setting the right parameters on your welding machine is equally important. For professionals, a MIG or TIG welder is ideal, with TIG offering greater control over the heat input. Keeping the heat input low is crucial to avoid excessive grain growth in the mild steel and to maintain the fundamental properties of both metals. A common tip is to use a pulsing technique to control the heat, especially when using TIG welding, as it minimizes the heat affected zone (HAZ).
welding mild steel with stainless rod
During the welding process, the welder should maintain a steady hand and consistent speed to ensure an even weld pool, reducing the risk of weak spots. Once the welding is complete, post-weld heat treatment might be necessary depending on the thickness and application of the materials involved. This helps relieve any stresses introduced during welding and enhances the overall strength of the joint.
Intrinsic in discussing the compatibility of these materials is the potential for galvanic corrosion. This electrochemical process occurs when two dissimilar metals are in contact in the presence of an electrolyte, potentially leading to accelerated rusting of the less noble metal, in this case, mild steel. Using an appropriate welding technique to minimize residual stress and applying a protective coating can mitigate such risks.
From a practical standpoint, the application of welding mild steel with a stainless rod spans several industries, from construction to automotive repairs. One remarkable advantage is the enhanced corrosion resistance imparted to mild steel when mated with stainless; this can prove beneficial in environments where moisture and chemical exposure are persistent concerns.
In conclusion, while welding mild steel with a stainless rod presents its fair share of challenges, informed preparation and understanding of the materials involved can yield durable and resilient results. This method opens up new possibilities in combining economical material choices without compromising on quality or performance. As welders gain experience with such techniques, they expand their craft, bringing together the best of both worlds—mild steel's affordability and stainless steel's durability. Through knowledge-backed execution, welders can leverage these properties to meet and exceed practical demands in various applications.