Selecting the right stick rod for stainless steel welding is crucial for ensuring high-quality welds that meet both the aesthetic and functional requirements of your project. Stainless steel is celebrated for its excellent resistance to corrosion and rust, making it a popular choice in industries ranging from automotive to construction and even food processing. However, due to its unique properties, welding stainless steel requires specific considerations and precision.
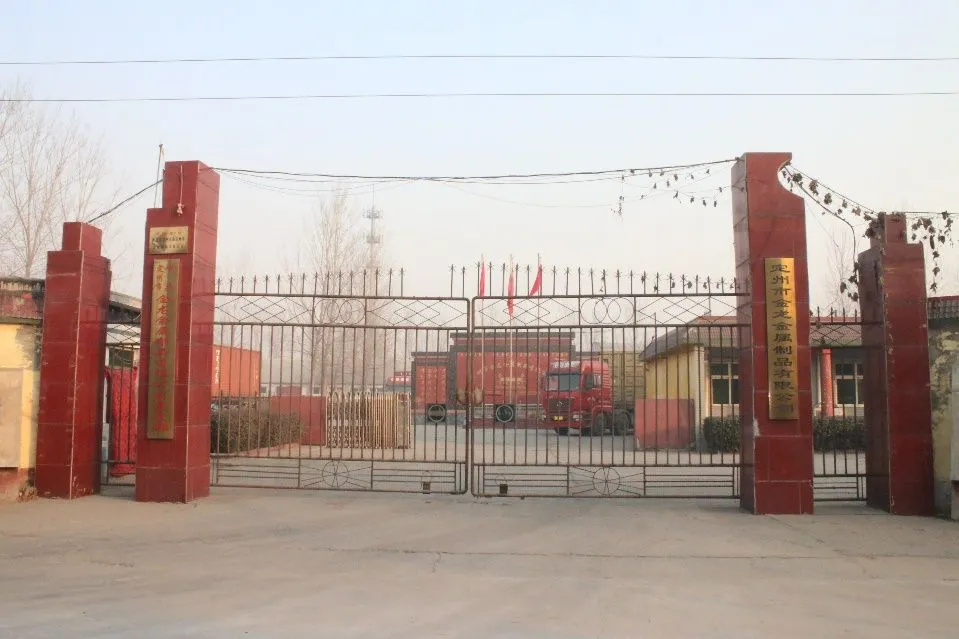
When it comes to welding stainless steel, E308L-16 is one of the most commonly used stick rods. This electrode is designed specifically for welding austenitic stainless steels, like types 304 and 308, which are among the most widely used stainless steel grades. What makes the E308L-16 electrode stand out is its low carbon content. This feature reduces the risk of intergranular corrosion, making it incredibly effective for joining stainless parts without compromising their durability.
Another notable option is the E309L-16 electrode, which is primarily used for welding dissimilar metals. If your project involves joining stainless steel to mild or carbon steel, this rod is the ideal choice. The unique composition of E309L-16 effectively accommodates the differences in expansion and thermal conductivity between the two metals, providing a strong, reliable bond.
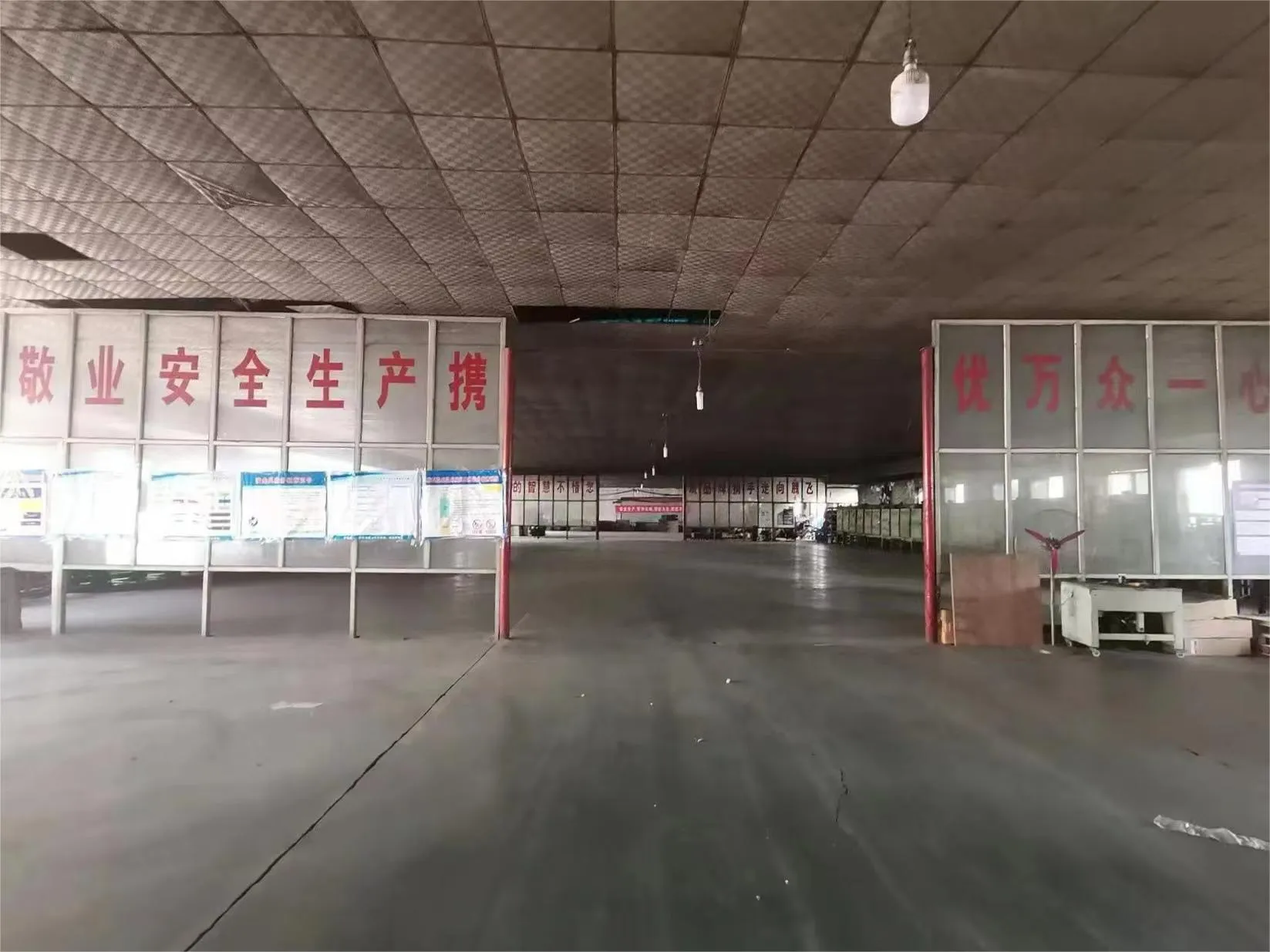
E316L-16 electrodes offer an additional layer of protection against corrosion, making them suitable for environments exposed to harsh chemicals or high saline conditions, such as marine or industrial applications. These rods are perfect for projects requiring enhanced resistance to chemical corrosion, especially if the stainless steel in use is of grade 316.
stick rod for stainless steel
One key aspect in stainless steel welding is managing heat input. Stainless steel can become distorted or discolored if exposed to excessive heat. Skilled welders recommend using a lower amperage setting with stick rods to maintain a cooler arc and minimize heat input. Onsite experience shows that consistent practice and technique adjustment are required to master the balance between adequate penetration and heat management. Experienced welders often preheat thicker sections of stainless steel to reduce thermal shock, which helps prevent warping and cracking.
For those venturing into stainless steel welding, safety is paramount. Stainless steel produces toxic fumes when welded with stick rods, necessitating adequate ventilation and proper protective gear. It's crucial to wear a respirator and ensure that the work area is well-ventilated to avoid the inhalation of harmful particles. Professional welders stress the importance of these precautions, noting that long-term exposure can lead to serious health issues.
When selecting a supplier for stick rods, reputation and certification are important indicators of quality and reliability. Suppliers who conform to international standards, like AWS (American Welding Society), guarantee that their electrodes meet rigorous safety and performance benchmarks. Buyers should insist on documented evidence of certification and consider user reviews and recommendations to gauge the trustworthiness of their supplier.
Incorporating these insights not only fosters a deeper understanding of stick rod applications for stainless steel but also promotes practices that align with principles of expertise and authority in the welding industry. Whether you are a seasoned professional or a hobbyist, understanding these elements will enhance your welding projects and ensure the longevity and safety of your welded structures.