Stainless steel stick welding, also known as shielded metal arc welding (SMAW), is a process that demands both skill and understanding of metal properties to achieve optimal results. As a seasoned welding technician, mastering this craft requires a keen insight into the nuances of stainless steel and the specific techniques to tackle its challenges effectively.
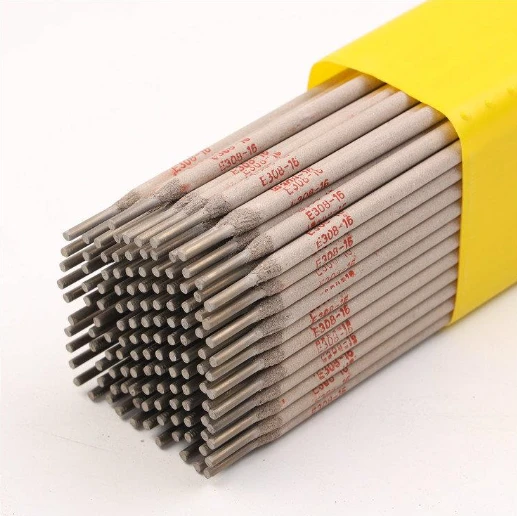
Stainless steel is praised for its corrosion resistance, which stems from its chromium content. This same characteristic presents challenges during welding, primarily due to its ability to retain heat, leading to potential warping and distortion. Moreover, the introduction of ferrite in stainless steel can influence the mechanical properties post-welding, necessitating careful selection of electrodes and welding parameters.
When considering electrodes for stick welding stainless steel, selecting the right type is crucial for ensuring weld integrity. Electrodes such as the E308 and E309 series are commonly used, depending on the grade of stainless steel in question. These electrodes are designed to match and compensate for the chromium and nickel content in the base metals, maintaining the corrosion resistance and mechanical strength in the finished weld.
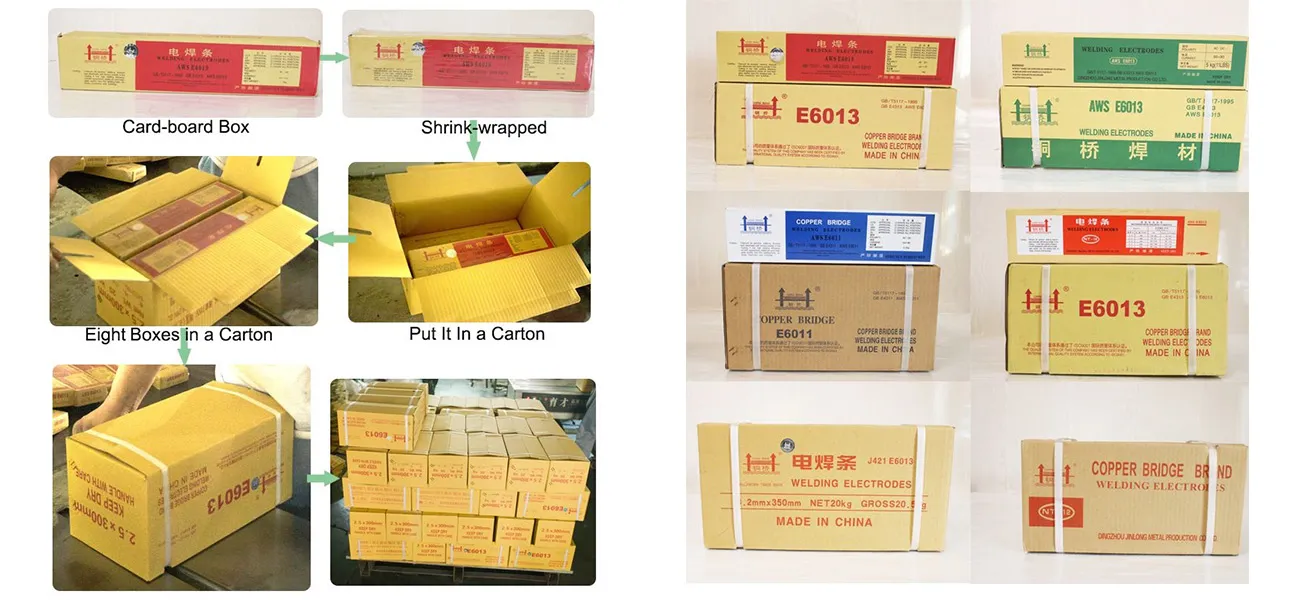
Preparation is critical in the welding process. Ensure the surfaces are thoroughly cleaned and free from contaminants. Stainless steel is susceptible to contamination from carbon or any foreign particles, which can lead to carbide precipitation and intergranular corrosion. Using dedicated tools and brushes for stainless steel is recommended to avoid cross-contamination.
Controlling the heat input is another critical aspect of welding stainless steel. Excessive heat can result in discoloration and loss of corrosion resistance at the weld area. Techniques such as stitching or short, intermittent welds can effectively manage heat buildup. In addition, using back purging techniques with argon gas can help protect the weld's underside, minimizing oxidation and discoloration.
stick stainless steel welding
A major factor influencing the success of a stainless steel weld is the welder's expertise. Familiarity with the various welding positions and the ability to adjust technique accordingly is essential. In particular, stainless steel requires more precise control over the arc and electrode angle due to its thermal conductivity properties, which are lower than those of carbon steel. This affects the heat distribution and can lead to issues such as porosity or incomplete fusion if not properly managed.
Post-weld cleaning is an important step often underestimated by beginners. Removing heat tints and oxides from the weld area is crucial for returning the stainless steel to its optimal corrosion-resistant state. This can involve mechanical methods such as brushing and grinding or chemical passivation, which can restore the chromium-oxide layer on the surface.
Safety considerations are pivotal when welding, especially with stainless steel, given the health risks associated with hexavalent chromium fumes. Implementing appropriate ventilation and personal protective equipment is non-negotiable to safeguard against these hazards.
Stainless steel stick welding is not just a technical skill but an art that melds knowledge with precision. Mastering this process means understanding the steel itself as much as the technique. Each weld tells a story of the welder's expertise, evidenced by smooth, consistent beads and a clear, unmarred surface.
This article serves as a testament to the depth of expertise required to excel in stainless steel welding. By combining practical experience with technical knowledge, welders can ensure a high-quality outcome that meets the stringent demands of industries reliant on stainless steel's enduring properties. As production standards elevate globally, so too must the precision and professionalism of the welds we perform, solidifying the welder's role as both artisan and engineer.