Selecting the right stainless steel welding rod size is crucial for achieving optimal weld quality and performance. Understanding the variability in sizes and their corresponding applications not only ensures robust welds but also enhances operational efficiency and safety. This guide delves into the nuanced world of stainless steel welding rods, offering insights that cater to both novices and seasoned professionals in the welding industry.
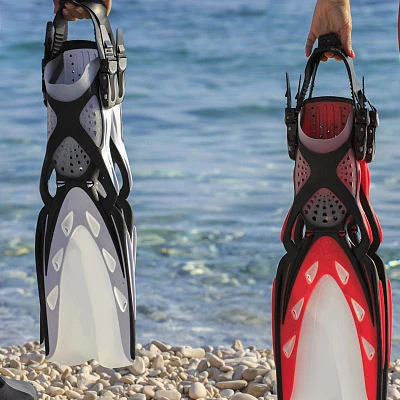
Stainless steel welding rods come in a variety of sizes, each tailored for specific applications. These rods are primarily categorized based on diameter, which can range from as small as 1/16 inch to as large as 1/4 inch. The choice of size influences several factors including penetration depth, stability of the arc, and overall strength of the weld. Smaller diameters, such as 1/16 inch and 3/32 inch, are typically used for applications requiring precision and delicate handling. These sizes are ideal for thin materials or intricate welding tasks where control and finesse are paramount.
For applications involving thicker materials or requiring deeper penetration, larger sizes such as 1/8 inch, 5/32 inch, and 1/4 inch are more appropriate. These rods provide the necessary heat input and arc stability for robust welds on thick sections. It’s essential to match the rod size with the appropriate amperage settings on the welding machine to prevent defects like burn-through or lack of fusion.
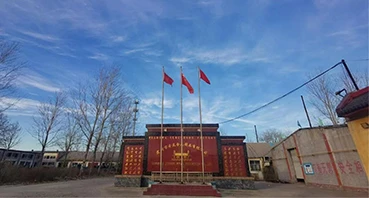
The material composition of stainless steel welding rods also plays a critical role in their selection. They are generally composed of an alloy that combines elements such as chromium, nickel, and molybdenum, designed to enhance corrosion resistance and mechanical properties. For instance, a 308L rod is commonly used for welding similar grades of stainless steel due to its low carbon content that minimizes carbide precipitation. On the other hand, 316L rods are preferred in environments prone to harsh chemical exposure due to their enhanced corrosion resistance.
Another crucial consideration is the welding process being employed. Processes like Tungsten Inert Gas (TIG) and Metal Inert Gas (MIG) welding have specific requirements regarding rod sizes and types. TIG welding, known for its precision and ability to produce clean welds, often utilizes smaller rod diameters which facilitate meticulous control. In contrast, MIG welding, characterized by its speed and efficiency, generally uses larger rods that feed automatically from a reel.
stainless welding rod sizes
The working environment also dictates rod size selection. Factors like welding position—whether it’s flat, vertical, overhead, or horizontal—affect the choice of rod diameter. Certain positions necessitate smaller rods to avoid gravitational issues and ensure optimal flow and deposition. Environmental conditions like humidity and temperature should also be considered, as they can impact the rod’s performance and the overall quality of the weld.
In the broader context of the welding industry, operator skill level significantly influences rod size selection. Beginners are often cautioned against using oversized rods without sufficient practice, as they may struggle with control, leading to suboptimal welds. Training and skill refinement can thus widen the spectrum of rod sizes an operator may confidently handle.
Safety cannot be overlooked when selecting welding rod sizes. Proper handling ensures that the welder and nearby personnel are protected from ultraviolet and infrared radiation exposure. Appropriate safety gear, including goggles, gloves, and protective clothing, must be used in conjunction with the right rod size to maintain a safe working environment.
The choice of stainless steel welding rod sizes directly impacts the welding process's efficiency, quality, and safety. By understanding the specific applications, material properties, requirements of different welding processes, environmental factors, and safety protocols, welders can make informed decisions that enhance their craftsmanship and professionalism. Continuous learning and adaptation to new materials and technologies will further solidify an operator’s expertise and authority in the field, ensuring trustworthiness in delivering durable and reliable welds.