SS welding, or stainless steel welding, is a complex and crucial process that requires a deep understanding of materials, techniques, and specifications to ensure high-quality results. A primary concern for any project involving stainless steel is the selection of the appropriate welding electrode, which directly influences the strength, appearance, and durability of the weld. This article delves into the specialized world of SS welding electrode specifications, providing insights into selecting the right electrode for your specific needs, enhancing both your project's outcome and the credibility of your work.
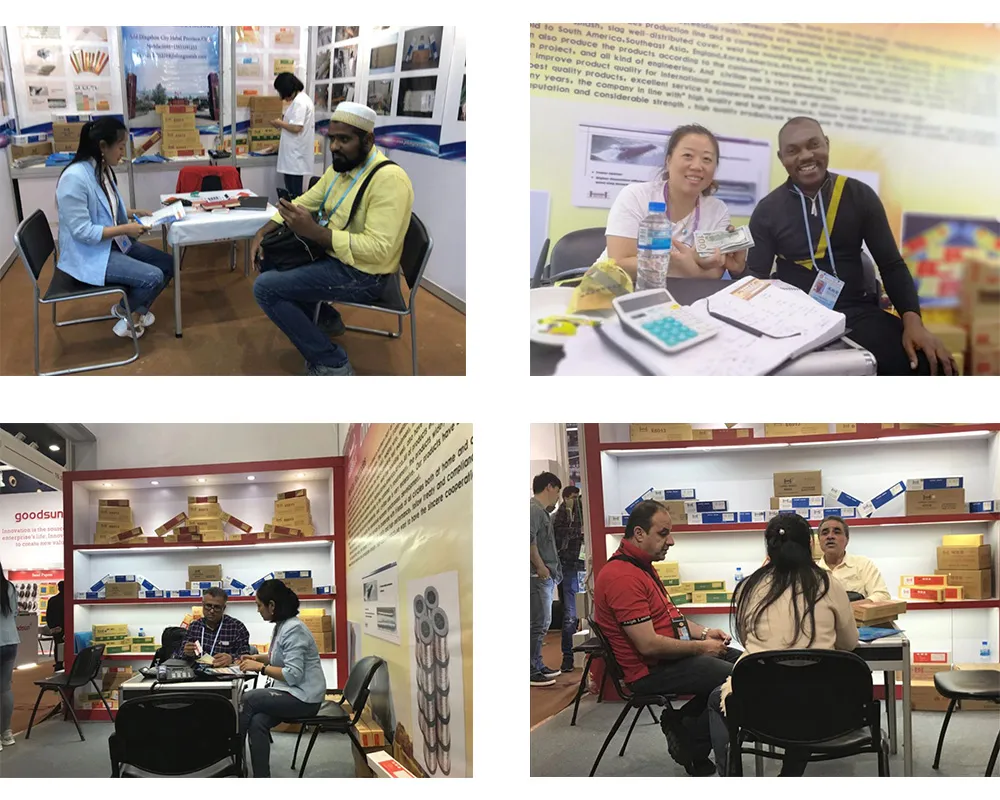
The heart of stainless steel welding lies in the properties that make stainless steel unique—its resistance to corrosion, high strength, and aesthetic appeal. However, these same properties can make welding it more challenging. The electrode you choose must match these properties to achieve a seamless weld. For instance, electrodes such as E308L and E309L are often recommended for welding austenitic stainless steels due to their lower carbon content, reducing the potential for carbide precipitation and thereby enhancing corrosion resistance.
Selecting the right electrode starts with understanding the base metal you are working with. Stainless steel grades can vary significantly, and so must the electrodes designed to weld them. The electrode coating is equally crucial, influencing factors such as arc stability, penetration, and weld bead appearance. Basic coated electrodes are often favored in professional settings for their ability to produce smooth, clean welds with little slag.

One critical aspect for ensuring the author's expert status is discussing the nuances of electrode sizing. Choosing the correct diameter is necessary to achieve optimal penetration and to accommodate the joint's specifics, such as its location and orientation. Smaller diameters are suitable for thin materials, whereas thicker electrodes can better manage higher heat inputs for thicker materials. Experts will also account for welding position; overhead or vertical welds often benefit from different electrode choices than flat or horizontal ones.
Moreover,
the choice of electrode is influenced by the welding environment. For instance, certain electrodes are designed for low-temperature or high-moisture conditions. Acidic environments, which can accelerate corrosion, necessitate electrodes that can offer superior resistance to these conditions. This attention to environmental details affirms the expertise required to make informed choices.
ss welding electrode specification
A discussion about welding electrode specifications would be incomplete without mentioning the importance of conformity to industrial standards. Certification and manufacturing standards, such as those provided by the American Welding Society (AWS), offer guidance and ensure electrodes meet rigorous testing for reliability and performance. This level of compliance not only reassures clients of quality but also positions the welder as knowledgeable and authoritative within the industry.
Trustworthiness in welding comes from not only using high-quality electrodes but also following stringent testing and quality control measures. Expert welders will consistently test their equipment and materials, adapting techniques as necessary to ensure the integrity of the weld. This dedication to quality assurance is what sets top professionals apart from the competition, establishing a reputation for excellence.
In practical terms, thorough documentation of your choice of electrodes, environmental conditions, and results not only provides a valuable reference for future projects but also reinforces the authority and expertise of the professional. This recorded experience becomes a testament to the welder's skill, enhancing both personal credibility and client confidence.
In conclusion, the world of SS welding electrode specification is intricate and demands a high level of expertise and attention to detail. By selecting the right electrode based on the base metal, environmental conditions, and industry standards, professionals can create welds characterized by strength and longevity. This meticulous approach not only elevates the quality of work but also enhances the welder's reputation for competence and reliability in the field.