Selecting the right stainless steel TIG welding rod is crucial for achieving high-quality welds, particularly in precision and industrial applications. The choice of a welding rod affects the weld's mechanical properties, corrosion resistance, and overall durability. Understanding the nuances of each type of stainless steel TIG welding rod can guide you in selecting the right material for your specific project, ensuring not just superior execution but also compliance with industry standards.
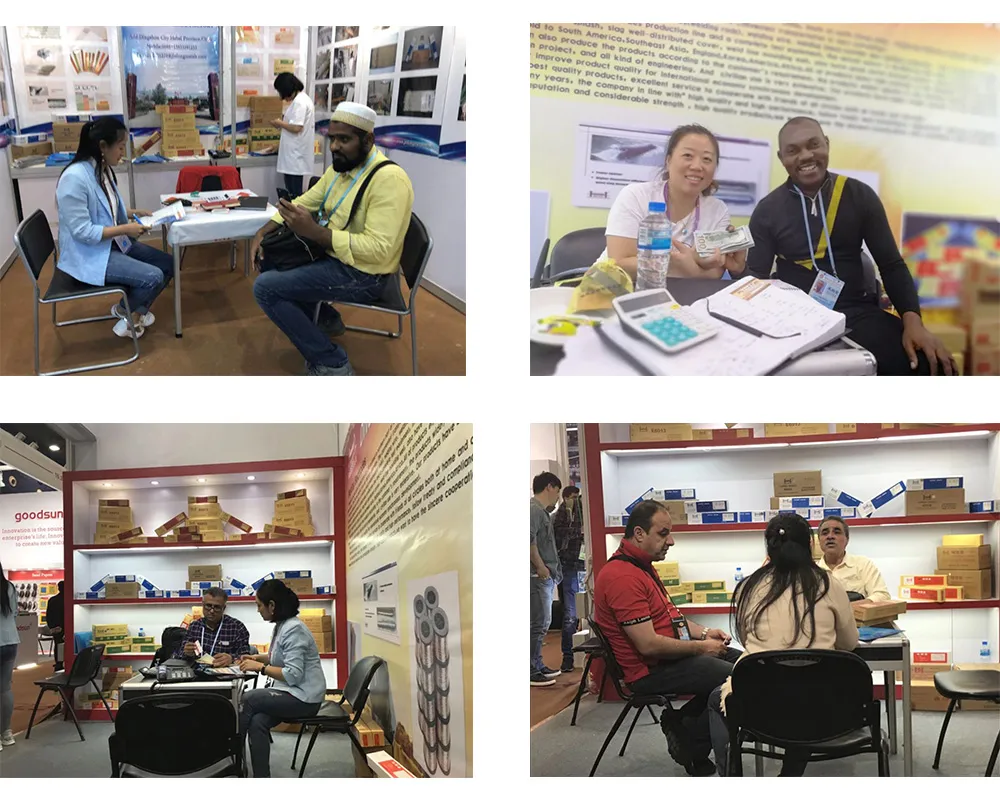
Stainless steel TIG welding, known for its precision and cleanliness, relies on filler rods that complement the base materials. ER308L is among the most commonly used types due to its versatility and ability to weld austenitic stainless steels such as 304 and 304L. The 'L' signifies low carbon content, which prevents carbide precipitation and enhances corrosion resistance, making it ideal for applications where the weld is subject to corrosive environments.
When working with 316 or 316L stainless steels,
ER316L welding rods are the recommended choice. These rods contain molybdenum, offering added resistance to pitting and crevice corrosion — a critical feature in saline and industrial settings. The ER316L is frequently utilized in chemical processing plants, marine applications, and in the manufacturing of medical devices, illustrating its broad scope of application and reliability in harsh conditions.
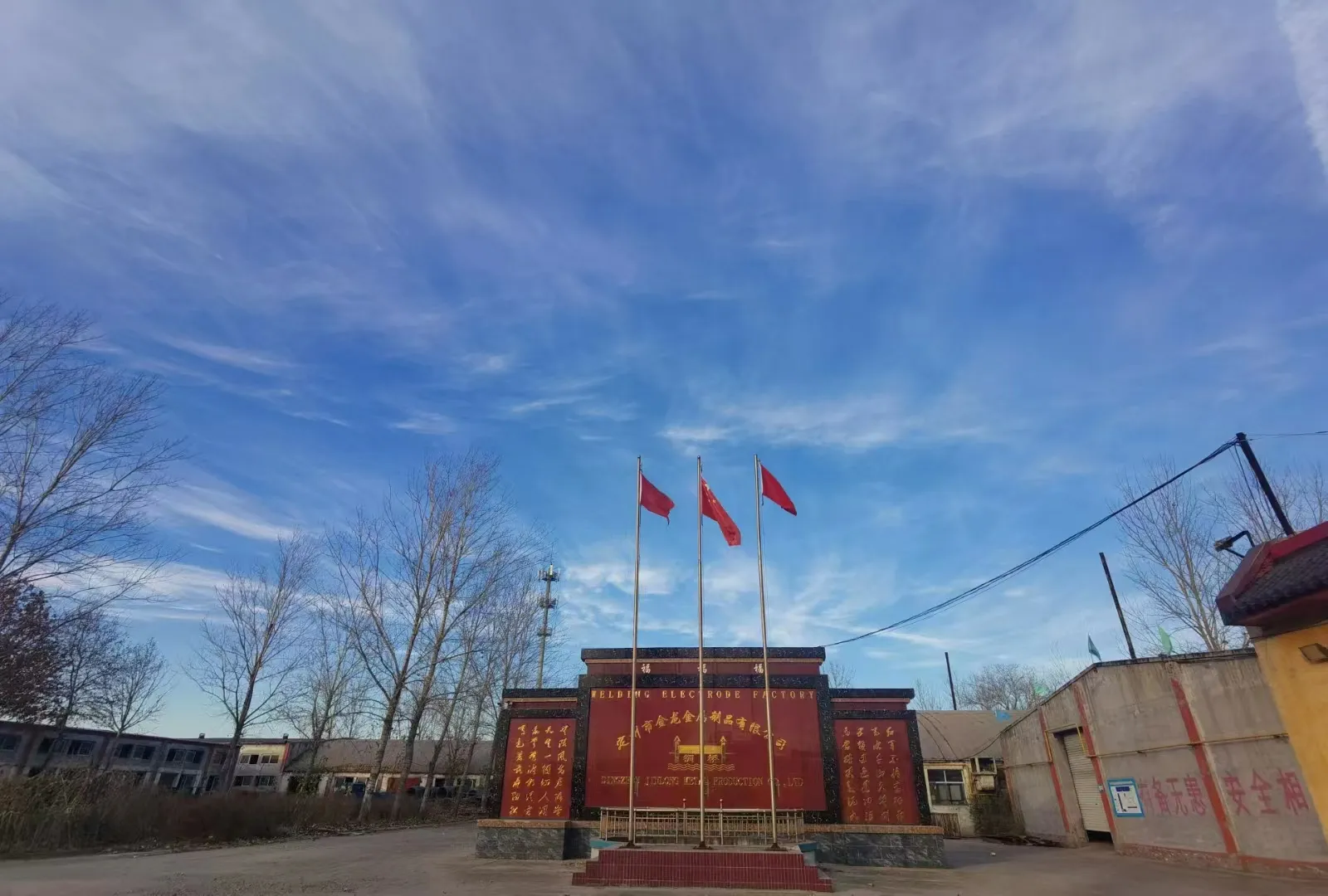
For high-temperature applications, ER310 welding rods provide a robust solution. Designed for 310 stainless steel, these rods maintain their integrity at temperatures up to 2100°F (1150°C). This makes them suitable for welding furnace parts, heat treatment baskets, and kiln linings.
Duplex stainless steels call for specialized electrodes like ER2209, which reinforce both strength and corrosion resistance through a dual-phase structure of austenite and ferrite. Such fillers are essential in environments that demand high resistance to stress corrosion cracking and corrosion fatigue, commonly needed in offshore platforms and chemical tankers.
stainless steel tig welding rod chart
In terms of technique, precision in welding involves managing heat input and shielding gas flow to avoid defects like porosity or cracking. Argon is often used as the primary shielding gas, but mixtures of argon with hydrogen or helium are employed to enhance penetration and control bead profile, especially in thicker sections.
Conforming to industry standards such as AWS (American Welding Society) and ISO (International Organization for Standardization) ensures the material's authenticity and performance. Certifications act as a guarantee for quality and suitability, providing peace of mind to manufacturers and end-users.
Professional welders emphasize the importance of rod handling and storage to maintain quality. Exposure to moisture can lead to hydrogen entrapment, leading to potentially catastrophic weld failures. Keeping rods in a dry, controlled environment is a simple yet critical practice for ensuring the longevity and integrity of the welds.
In conclusion, choosing the appropriate stainless steel TIG welding rod involves a combination of understanding the material properties, application requirements, and adherence to industry standards. Mastery of these elements supports the execution of superior welds suited to the demands of modern engineering projects. As industries evolve and the demand for durable, corrosion-resistant materials grows, staying informed about the latest advancements and techniques in welding rods becomes an indispensable aspect of professional development for engineers and welders alike.