In the world of welding, selecting the right welding rod is pivotal not only for the success of a project but also for ensuring safety and durability. Among the myriad of options available, stainless steel welding rods stand out due to their superior resistance to corrosion and high-temperature environments. However, beyond merely picking a welding rod labeled stainless steel, understanding the intricacies of the welding rod number is essential for both precision and performance.
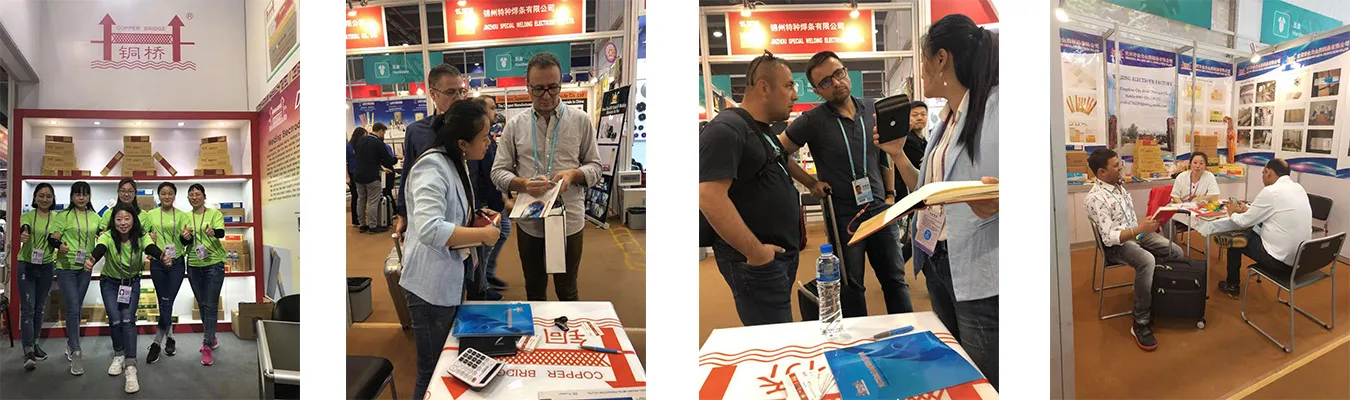
Welding rod numbers associated with stainless steel, such as 308, 309, 316, or 347, offer vital clues about the chemical composition and intended use of each rod. These numbers might seem arbitrary at first glance, but they are the outcome of years of metallurgy evolution and industry standardization. For instance, a 308 stainless steel welding rod is primarily used for welding similar base metals like 304 and 308 stainless steels. The number indicates a balance of chromium and nickel, providing excellent corrosion resistance and good ductility.
The 309 and 310 stainless steel rods are particularly interesting due to their high chromium and nickel content, making them perfect for high-temperature applications. They are typically employed in welding dissimilar metals, especially where a high heat input is necessary. The 309 rod, for example, is used when joining stainless steel to conventional steel, indicating its versatile nature and enhanced capability to handle thermal expansion differences.
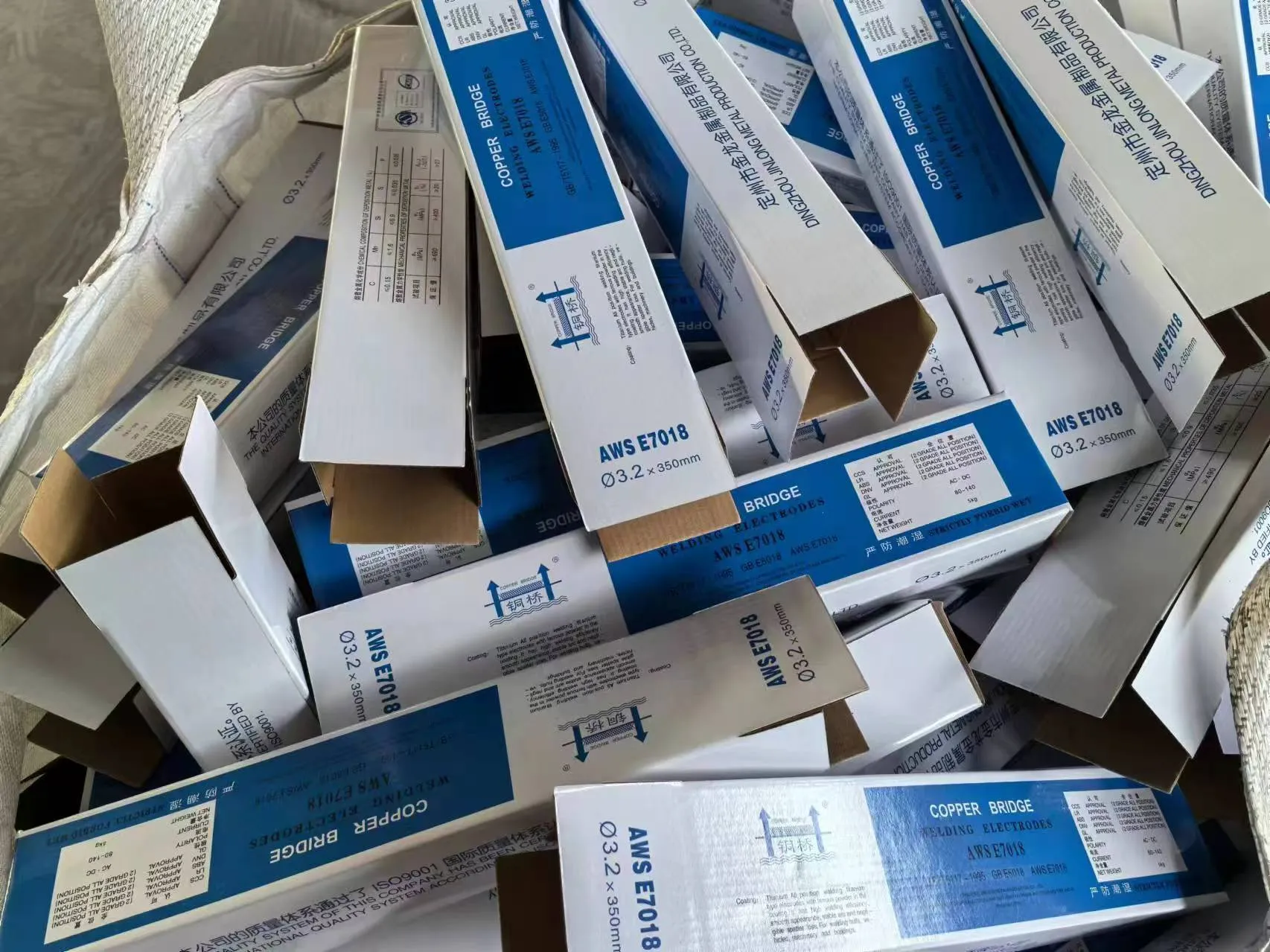
Moving to more specialized applications, the 316 stainless steel welding rod is renowned for its molybdenum content, which offers enhanced corrosion resistance against chlorides and various acids. This makes it the material of choice in chemical processing environments, medical applications, and other scenarios where sterility and resistance to aggressive substances are paramount.
For critical applications requiring utmost reliability, the 347 stainless steel welding rod comes into play. It contains niobium, which helps in stabilizing the metal structure during welding. This property is essential when welds are subjected to temperatures in long term operations, such as in power generation and aerospace industries.
stainless steel welding rod number
From an expertise perspective, the correct selection of a stainless steel welding rod extends beyond merely deciphering the numbers. Each weld project should begin with a thorough analysis of the base materials, the environmental conditions they will face, and the mechanical properties required. This expertise guides the welder in selecting the rod that provides not just a strong weld, but also a solution that will stand the test of time and conditions.
Authoritativeness in the field of welding, particularly concerning stainless steel, also demands a recognition of certifying bodies and standards. Organizations such as the American Welding Society (AWS) play a crucial role in dictating industry norms, and familiarization with their guidelines can enhance quality significantly. For instance,
a welding rod conforming to AWS classification A5.4 or A5.9 can assure the buyer of its adherence to tested quality standards, thus boosting confidence in its performance.
Trustworthiness is further cemented by choosing rods from reputable manufacturers known for quality control and superior metallurgy. Brands with a history of innovation and adherence to standards often provide data sheets detailing chemical composition, tensile strength, yield, and elongation percentages, offering transparency that can be trusted implicitly.
In conclusion, the art and science of picking a stainless steel welding rod extend far beyond the shop floor intuition. It involves a synthesis of material science, adherence to standards, and practical expertise that collectively ensure the integrity and performance of welds. Precision in understanding welding rod numbers thus becomes an indispensable tool in the welder’s toolkit, empowering them to make informed choices that resonate with safety, quality, and excellence.