Stainless steel electrodes are pivotal in the welding industry, offering remarkable durability and corrosion resistance. These electrodes are essential for tasks across various industries, from construction to automotive repair. Understanding the classification of stainless steel electrodes is crucial for optimizing their use, ensuring safety, and maximizing product longevity.
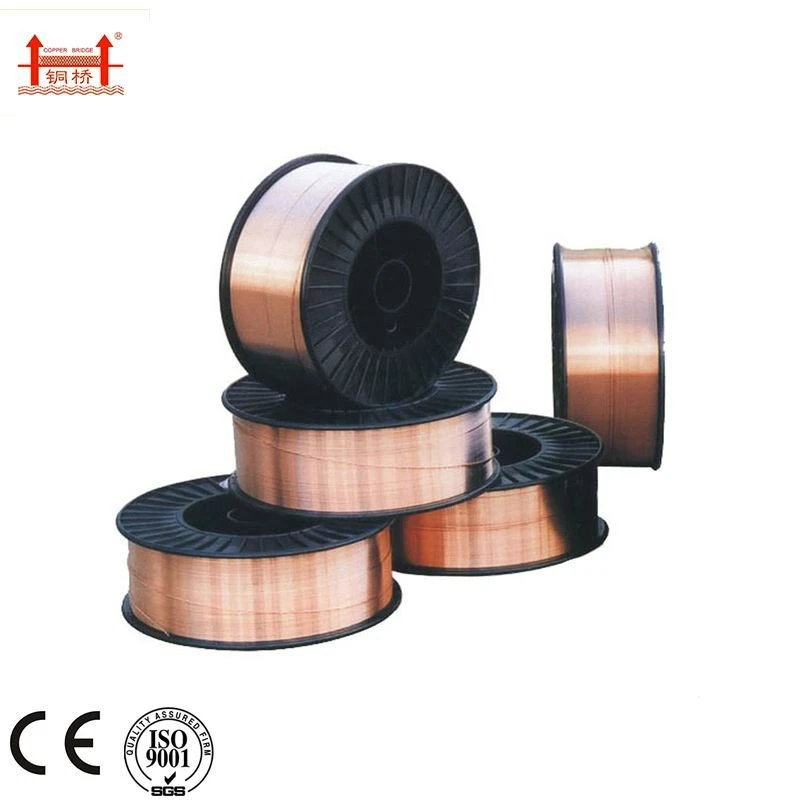
The classification of stainless steel electrodes is guided by standards set by organizations like the American Welding Society (AWS). Each electrode is categorized based on its unique chemical composition, mechanical properties, and intended application. One common standard is the AWS A5.4/A5.4M2012, which describes stainless steel electrodes used for shielded metal arc welding (SMAW). This classification encompasses several components that demand a nuanced understanding.
Typically, stainless steel electrodes are identified by a series of letters and numbers, such as E308L-16. Each section of this identifier shares specific information about the electrode’s characteristics.
The ‘E’ stands for electrode, indicating its primary functional role in welding. The first three digits (e.g., 308) reveal the chemical composition, which is tied to the type of stainless steel being welded. For instance, the ‘308’ series is commonly used to join 304 stainless steel.
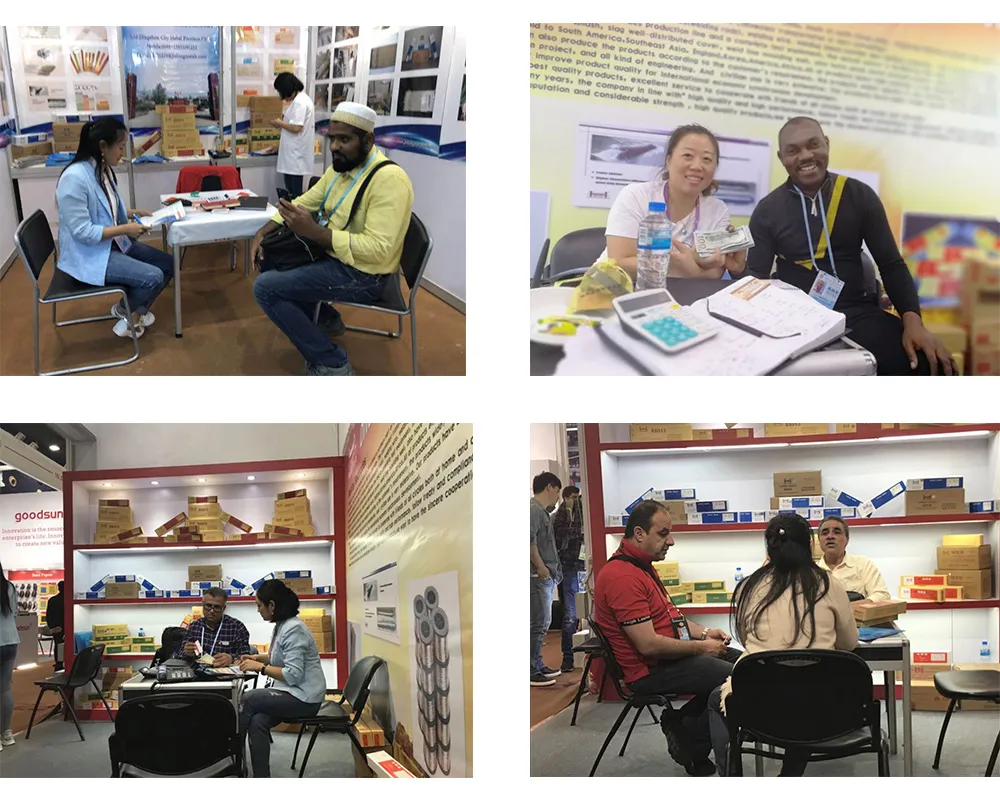
The letter that follows these digits provides additional information about the electrode’s low carbon content, indicated by an ‘L’ (e.g., E308L). Low carbon content helps minimize carbide precipitation, which is a crucial factor in preventing intergranular corrosion in stainless steel welds. Such prevention is vital in industries like food processing or pharmaceuticals, where hygiene and material integrity are paramount.
The number following the dash (e.g., 16 in E308L-16) indicates the type of current and coating used. The digit ‘1’ denotes an electrode usable with AC and DC currents, while the number ‘6’ refers to the specific type of flux coating, which influences the slag formation, arc stability, and overall weld quality. Understanding these subtle differences allows for the selection of the perfect electrode for specific applications, ensuring weld integrity and longevity.
stainless electrode classification
Products such as the E316L-16 electrode are favored for use in environments demanding resistance to chemical corrosion, especially in industries dealing with acids. The higher molybdenum content in the 316 series provides superior resistance, enhancing the weld’s ability to withstand harsh conditions. Different classifications bring unique benefits like increased tensile strength or enhanced corrosion resistance, and selecting the right one can mean the difference between a long-lasting structure and one prone to rapid decay.
The expertise required to choose the right stainless steel electrode involves not only a solid understanding of the classification system but also an appreciation of the welding process and the eventual operating environment of the weld. Skilled welders and engineers must be able to assess factors such as the base materials, the environmental conditions, and the mechanical stresses that the welded joints will endure. Additionally, understanding compliance and safety standards is imperative to ensure that welds meet regulatory requirements while maintaining structural integrity.
A real-world experience shared by industry professionals highlights the importance of electrode classification in critical infrastructure projects. In one instance, a team working on a major pipeline project needed to ensure that the welded joints could withstand high temperatures and pressures. By selecting the appropriate electrode, in this case, the E309L-16, they successfully maintained the integrity of the pipeline, preventing potential failures and ensuring the safety of the environment.
In conclusion, the classification of stainless steel electrodes is a sophisticated system that serves as the backbone for successful welding projects. By mastering these classifications, industry professionals can ensure optimal performance, safety, and durability in their welded structures. Trust in the system's expertise and authority ensures that every weld delivers on its promise of strength and longevity. Decoding this complex system opens up the potential for creating structures that stand the test of time, ultimately establishing a trusted standard in welding practices globally.