Selecting the right electrode for welding is a critical decision that greatly impacts the effectiveness, quality, and safety of your welds. This guide is tailored for both beginners and seasoned professionals seeking insightful, expert advice on making an informed choice.
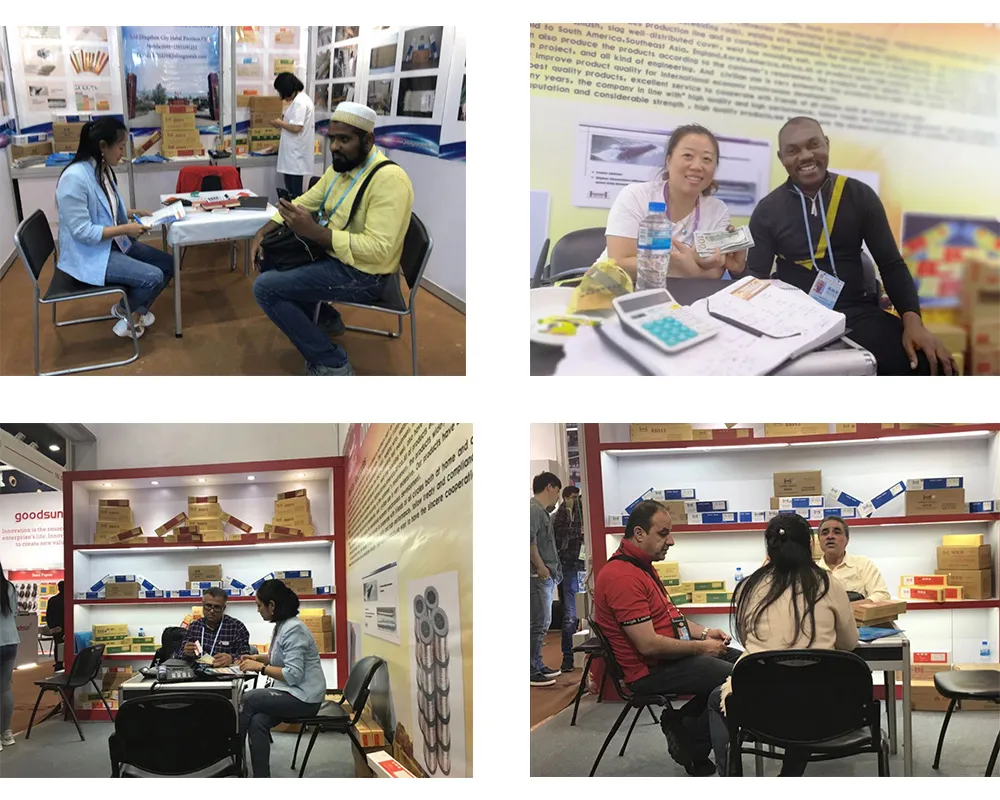
Understanding Electrode Types
Electrodes are essentially categorized into consumable and non-consumable electrodes. Consumable electrodes, such as those used in Shielded Metal Arc Welding (SMAW), Metal Inert Gas (MIG), and Flux-Cored Arc Welding (FCAW), melt during welding to fill the joint. Non-consumable electrodes, as seen in Tungsten Inert Gas (TIG) welding, do not melt but instead provide a conductive path for the electric arc.
Key Factors in Electrode Selection
1. Material Compatibility A primary consideration is the base material you plan to weld. For steel, electrodes like E6010, E6011, or E6013 are popular; for stainless steel, E308, E309, and E316 are preferred. Aluminum requires special electrodes, often based on the specific alloy.
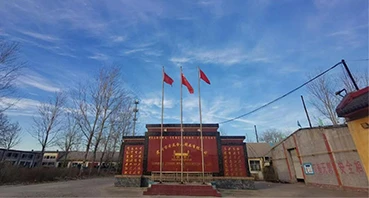
2. Welding Position Each welding position—flat, horizontal, vertical, or overhead—presents unique challenges. Certain electrodes are designed to handle these specific positions. For example, E7018 electrodes provide excellent performance in all positions, thanks to their versatile coating.
3. Thickness and Type of Joint The thickness of the materials and the joint configuration influence electrode choice. E7018 electrodes are suitable for heavier materials due to their strong penetration and filler properties, whereas E6013 is more suited to thinner sections and clean surfaces.
4. Power Source Compatibility The electrode selection must align with your welding machine's power capabilities—DC, AC, or both. Some electrodes are versatile, operating on both AC and DC, while others might be more specialized.
Secrets to Exceptional Weld Quality
- Electrode Coating The coating stabilizes the arc, protects the molten metal from contaminants, and can even influence penetration. Understanding the purpose of different coatings—like cellulose, rutile, or basic—can refine your welding outcomes.
how to choose electrode for welding
- Size Matters The diameter of the electrode affects the heat input and the deposition rate. Generally, thicker materials require larger diameter electrodes, but the welding position and desired precision can alter this guideline.
- Trial and Error Each project can present unique challenges, and experienced welders often emphasize the importance of testing different electrodes with sample materials before committing to a final choice. This practice can reveal unexpected nuances and optimize performance.
Enhanced Performance through Preparation
Proper electrode storage is vital to prevent moisture absorption, which can lead to defects like porosity or cracking. Consider storing electrodes in a dry environment with controlled humidity. Additionally, clean your base materials meticulously to remove rust, oil, or coatings that could interfere with the welding process.
Learning from Experts
Frequently, the nuanced knowledge of experienced welders can significantly shorten the learning curve. Joining welding forums, attending workshops, and seeking out tutorials can provide valuable insights into electrode performance, innovative techniques, and common pitfalls to avoid.
The Evolution of Electrode Technology
Manufacturers continue to innovate, creating electrodes with better arc stability, improved mechanical properties, and enhanced environmental considerations. Staying updated with the latest advancements can provide a competitive edge in both quality and productivity.
Final Thoughts
Choosing the right electrode involves a blend of scientific understanding and practical experience. By considering factors like material compatibility, welding position, power source, and preparation techniques, welders can achieve superior results while maintaining safety and efficiency.
Ultimately, the perfect electrode is one that meets the specific demands of your welding project, resulting in a strong, clean weld that meets or exceeds standards.