Selecting the right welding rod is critical for ensuring the strength, stability, and durability of welded structures. Welding rods, also known as filler rods, are not a one-size-fits-all product. They vary in material composition, size, coating type, and function, which is why understanding these variables is crucial for any welder, whether a novice or an expert. Here’s a guide to help you make an informed decision.
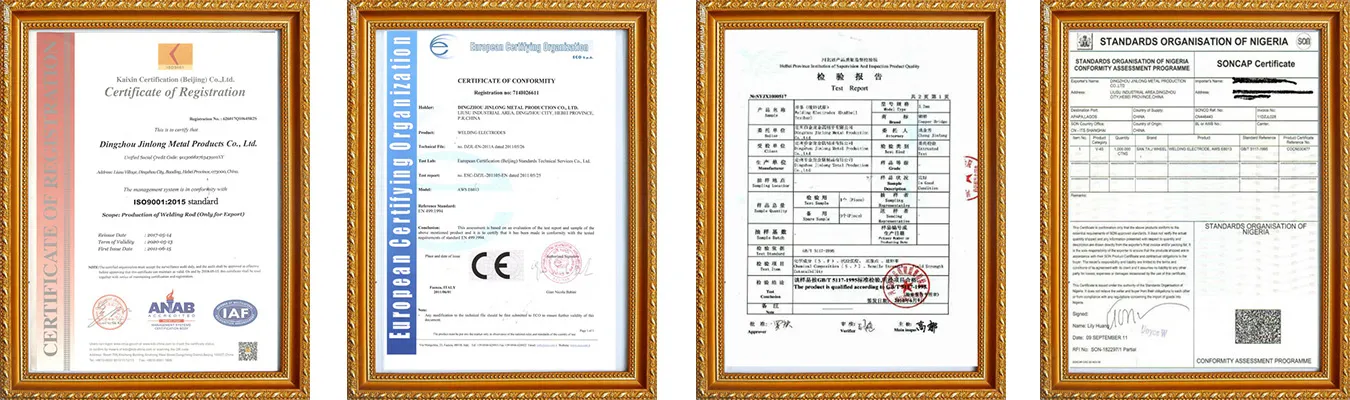
The first aspect to consider is the base metal you intend to weld. Welding rods must be compatible with the base metal to create a strong bond. Common metals include steel, stainless steel, aluminum, and cast iron, each requiring specific types of rods. For example, mild steel welding often utilizes E6010 or E7018 rods due to their versatility and strength.
Another significant factor is the welding position. Some rods are designed for specific positions such as flat, horizontal, vertical, or overhead. The E7018 rod is preferred for structural projects due to its all-position capabilities and high tensile strength, making it ideal for construction and general fabrication.
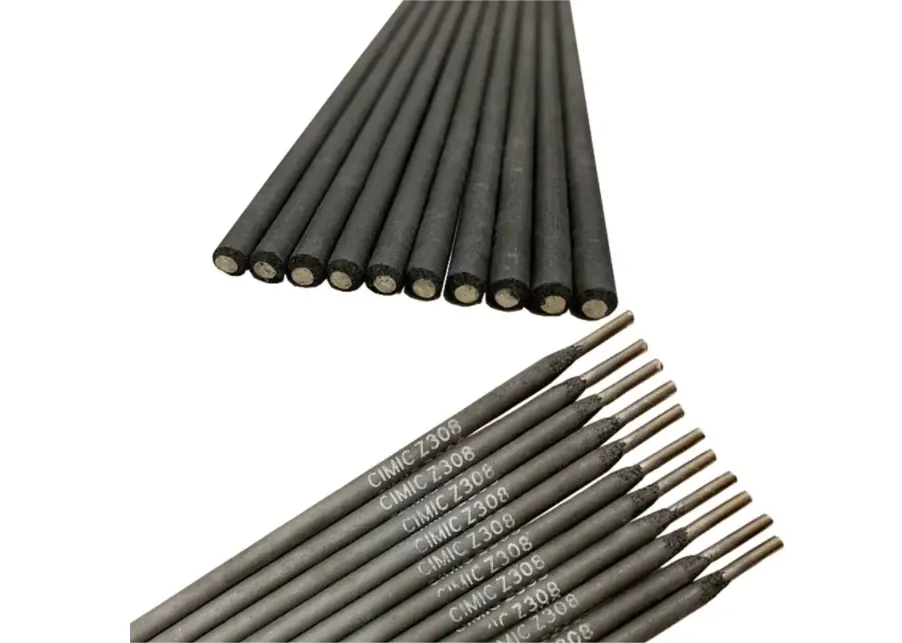
The welding process itself also determines the rod selection. Whether you are using shielded metal arc welding (SMAW), gas metal arc welding (GMAW), or tungsten inert gas welding (TIG), each process has compatible rods that optimize performance. For instance, SMAW, or stick welding, often uses rods like E6011 for deep penetration and E7018 for a smooth finish.
how to choose the right welding rod
Skill level and equipment availability should influence your choice as well. Some rods are more forgiving and easier to control, making them perfect for beginners. Conversely, advanced rods might offer superior results but require a skilled hand and sophisticated equipment to maximize their benefits. Beginners may find success with E6013 rods, which provide easy slag removal and smooth arc action.
Furthermore, the project specifications should guide your decision. Consider the environmental conditions your welded structure will face, such as humidity or exposure to corrosive substances. Certain rods come with coatings that enhance rust or corrosion resistance. The E7018 rod, for example, contains a low-hydrogen coating that's resistant to moisture-induced cracking.
Cost is a practical consideration, but it should never compromise quality. Investing in higher-quality rods ultimately saves time and money by reducing the need for rework. It's advisable to consult product reviews and industry forums for testimonials on rod performance to ensure trustworthiness in your selection.
Ultimately, selecting the right welding rod is about balancing several factors to match your specific welding needs. Also, adhering to manufacturer guidelines and industry standards can significantly enhance the results of your project. Leveraging technical expertise, user reviews, and continuous learning will guide you to make informed decisions that uphold the integrity and reliability of your work.