Selecting the right welding rod is crucial for achieving strong, durable welds and ensuring the overall success of any welding project. Welding rods, also known as electrodes, serve as a filler to join two pieces of metal and therefore must be chosen with care, as the quality of the weld largely depends on this choice.
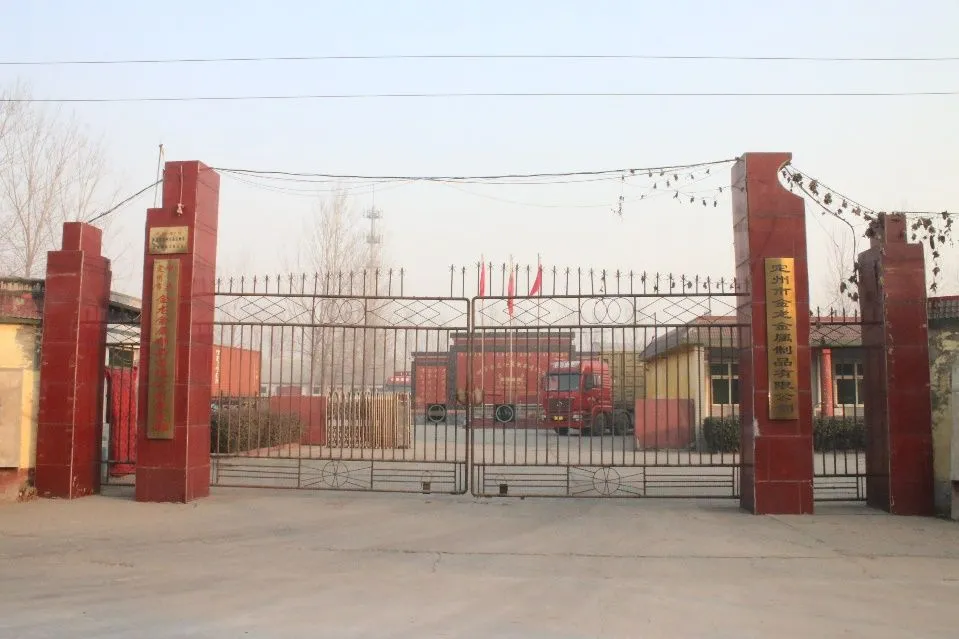
Understanding the Metal Type The first step in selecting the proper welding rod is identifying the type of metal you’ll be working with. Different metals require specific types of electrodes. For example, when welding steel, a rod with a higher iron content is preferable, providing a smooth transition and stable weld pool. In contrast, non-ferrous metals like aluminum or copper need rods with different chemical compositions to cater to their unique properties.
Consider the Welding Position Welding can be performed in various positions, and certain rods are designed for specific orientations. Whether you’re working on a flat, vertical, overhead, or horizontal position, the rod you choose must complement these working angles to ensure optimal penetration and weld quality. For instance, electrodes like the E6013 or E7018 are versatile choices known for better usability in various positions, making them excellent for multi-position projects.
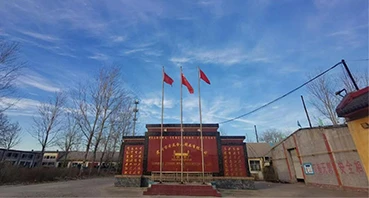
Match the Welding Current The choice of welding current can significantly impact the selection of a welding rod. Electrodes are generally categorized based on their usability with either alternating current (AC) or direct current (DC). Some rods are versatile, working well with both AC and DC; however, others may be specific to one type. E6010 rods, for example, are designed for DC and allow deep penetration necessary for root passes.
Analyze the Coating Types The coating on a welding rod not only influences its usability but also affects the mechanical properties of the weld. Coatings can be cellulosic, rutile, or basic, each providing different characteristics in terms of weld bead appearance and slag removal. Rutile-coated electrodes, for instance, offer easy slag removal, making them ideal for aesthetic welds, whereas basic-coated rods are preferred for applications requiring high strength and ductility.
how to choose a welding rod
Evaluate Environmental and Safety Conditions Environmental factors such as humidity and temperature can affect the storage and performance of welding rods. Low-hydrogen rods, like the E7018, need to be stored in proper conditions to prevent moisture pick-up, which could lead to hydrogen-induced cracking. Additionally, some rods produce more fumes than others, so proper ventilation and personal protective equipment (PPE) is a consideration to ensure safety.
Review Mechanical Properties Requirements Consider the mechanical properties like tensile strength, impact resistance, and ductility required for the completed weld. This requirement will guide your electrode choice, ensuring the weld can withstand the operational stresses it will encounter. For structural applications, selecting a rod that matches or exceeds the base metal’s mechanical properties is vital.
Account for Cost-Effectiveness While the technical specifications are paramount, the project budget also plays a role in electrode selection. High-quality rods might be more expensive, but they often offer better performance and lower post-weld repair rates, saving time and money in the long run. Balancing the costs with the advantages of higher-grade electrodes can lead to more efficient and cost-effective operations.
In conclusion, the intricate process of selecting a welding rod involves careful consideration of metal types, welding positions, electrical currents, coating materials, environmental conditions, mechanical properties, and budget constraints. Mastery in these areas not only enhances one’s skills but elevates the quality and professionalism of the welding projects undertaken. Through experience, expertise, and adherence to safety standards, welders can achieve impeccable results with the appropriate welding rod.