Gas shielded flux core wire (GSFCAW) has revolutionized the realm of welding, integrating innovation and efficiency that appeal to professionals and hobbyists alike. This dual-purpose wire involves an intriguing fusion of the processes associated with flux-cored arc welding (FCAW) and gas metal arc welding (GMAW), promoting optimal welds with enhanced strength and durability. In an era focusing on quality and productivity, understanding the benefits and applications of gas shielded flux core wire is essential for any welding enthusiast or professional striving to meet industry standards and client expectations.
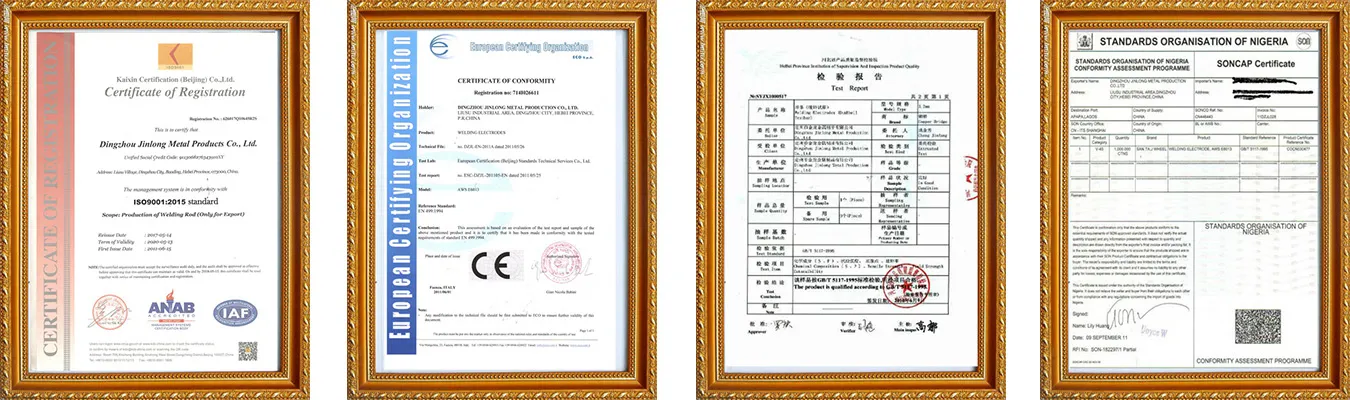
The chemical composition of gas shielded flux core wire serves as the foundation of its superior performance. Unlike traditional solid wires, GSFCAW comprises a hollow tubular section filled with flux and alloying agents. These compounds play a pivotal role in stabilizing the arc, protecting the molten metal from environmental contaminants, and ensuring uniformity in the weld's mechanical properties. The external shielding gas—commonly a blend of argon and carbon dioxide—enhances this protection further, minimizing the risk of porosity and other welding defects. Such a combination ensures that the welds not only meet but often exceed structural integrity requirements.
Professional welders often favor gas shielded flux core wire for its impressive versatility across various materials and thicknesses. Whether working with carbon steels, stainless steels, or even nickel-based alloys, GSFCAW proves its reliability and adaptability. The wire's unique formulation enables users to execute welds in diverse positions—from flat and horizontal to vertical up and overhead—without compromising quality or efficiency. This flexibility is crucial in industrial applications where time constraints and the need for precision collide, such as shipbuilding, construction, and heavy machinery manufacturing.
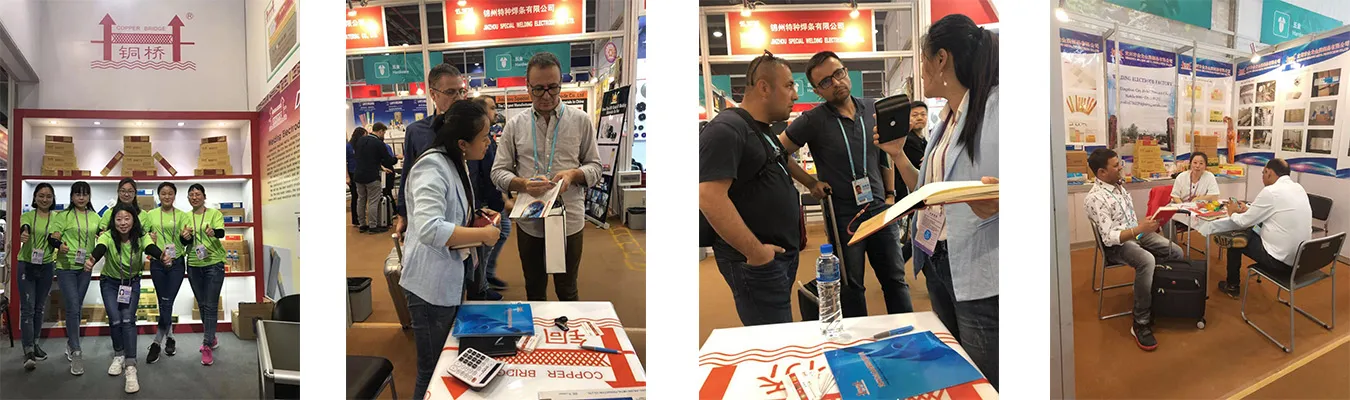
In terms of productivity, gas shielded flux core wire consistently demonstrates its value. The process supports higher deposition rates compared to solid wire alternatives, reducing the overall time required to complete a project. Furthermore, because the flux coating generates its protective atmosphere around the weld, it circumvents some of the setup complexities associated with entirely relying on external shielding gases. These attributes collectively contribute to a streamlined workflow, reducing downtime and maximizing output—key factors in competitive markets where cost efficiency is paramount.
Experience in the field reveals that the learning curve for GSFCAW can be considerably forgiving compared to other welding techniques. The stabilization provided by the flux core often results in a smoother and more controllable arc, a feature particularly beneficial for welders still honing their craft. This ease of use does not come at the expense of quality; even novices can achieve professional-grade results with minimal practice under guided supervision. Trust in this user-friendly aspect has seen GSFCAW gaining favor in educational settings, where the emphasis lies on skill development and foundational expertise.
gas shielded flux core wire
Numerous case studies emphasize the authoritative role of gas shielded flux core wire in welding. For instance, in large-scale infrastructure projects, GSFCAW welds consistently meet rigorous structural and safety standards, providing long-lasting joins that endure against environmental stressors and mechanical loads. The wire’s ability to perform under diverse conditions—integral to its reputation—assures project managers and inspection engineers of its dependability and efficiency.
In alignment with industry advancements, manufacturers continue to innovate gas shielded flux core wire designs, enhancing their performance attributes to align with evolving demands. Recent developments focus on refining the metallurgical properties of the wire to improve resistance against wear and corrosion, extending the functional lifespan of welds subjected to harsh environments. As industries strive for sustainability, this ongoing adaptation of GSFCAW further establishes its position at the forefront of efficient welding solutions.
Trustworthiness remains a cornerstone in assessing the viability of any welding wire, and gas shielded flux core wire commands confidence through consistency in results and regulatory compliance. Leading manufacturers maintain stringent quality control measures, ensuring each batch of wire meets the highest industry standards before reaching the end user. Welders across various disciplines recognize and respect the reliability inherent in GSFCAW, advocating for its continued use and development in professional circles.
As the demand for high-quality welding solutions rises, gas shielded flux core wire represents a fusion of experience, expertise, authority, and trustworthiness. Its continued evolution promises future advancements in welding technology, securing its place as an indispensable tool in the craftsman's arsenal.