In the realm of metal fabrication, the selection of appropriate consumables is crucial. Among these, MIG (Metal Inert Gas) solid wire holds an esteemed place. An understanding of its utility can significantly enhance the welding experience, optimize production, and ensure structural integrity.
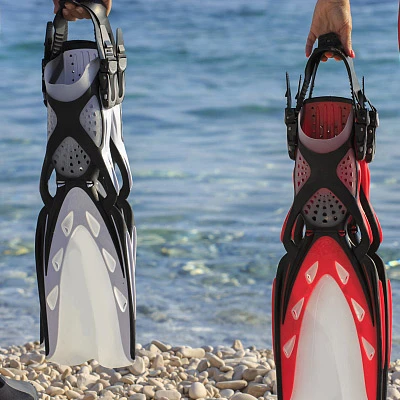
MIG solid wire, at its core, is a consumable component used extensively in welding processes. Its primary role is to act as a filler material that fuses with the base metals to form a strong joint. However, to truly leverage its capabilities, one must delve into the intricate facets of its application.
One distinguishing factor of MIG solid wire is its versatility. Available in different compositions, the wire is tailored to suit various materials, including carbon steel, stainless steel, and aluminum. The selection of the appropriate type is critical; for instance, ER70S-6 is highly favored for mild steel applications due to its excellent deoxidizers which allow welding over rust and mill scale.
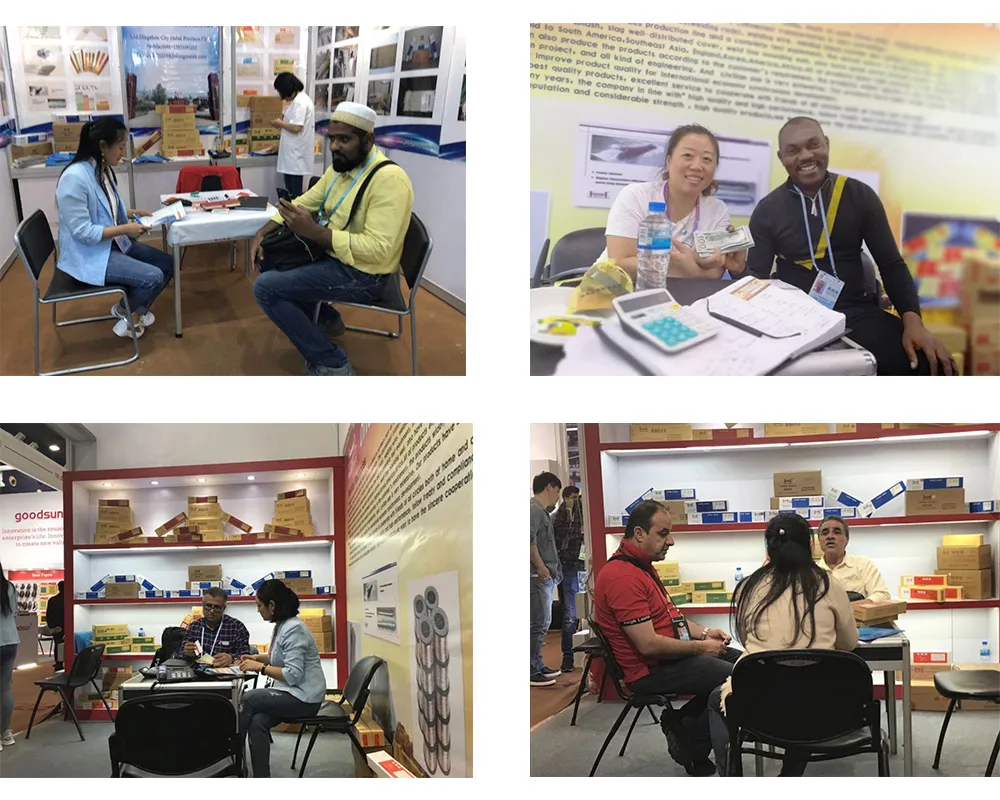
Expertise in utilizing MIG solid wire necessitates a profound comprehension of its diameter. Typically, wires range from 0.023 inches to 0.045 inches. The smaller diameters are advantageous for thin metal welding, minimizing the risk of burn-through, while thicker wires are suitable for heavier components and ensure deeper weld penetration.
The surface condition of MIG solid wire also plays a pivotal role. A clean, rust-free wire guarantees uniform feed and consistent arc stability, crucial for achieving superior weld quality. Experienced welders understand that proper storage and handling are vital to maintaining wire cleanliness, thereby enhancing consumable longevity and weld quality.
The authoritative use of MIG solid wire extends into its interplay with shielding gases. The selection of gases, such as 100% CO2 or a mix of Argon and CO2, impacts the arc characteristics, penetration, and overall cleanliness of the weld. For instance, a higher Argon content promotes smoother arc action and reduces spatter, offering a cleaner weld finish.
mig solid wire
Trustworthiness in the context of MIG solid wire involves relying on reputable manufacturers who comply with industry standards and certifications. Brands that invest in quality control measures ensure consistent wire diameter, chemical composition, and surface finish. This reliability is paramount in high-stakes industries such as automotive, aerospace, and structural engineering.
Moreover, the process parameters, including voltage, amperage, and travel speed, must be calibrated with precision. An optimal setup ensures efficient wire melting, minimized spatter, and a robust weld. Skilled operators often perform trial welds to fine-tune these parameters, tailoring them to the thickness and material type, ensuring the highest joint integrity.
Beyond technical proficiency, an exploration into the environmental and cost impacts of MIG solid wire is essential. High-quality wires not only enhance efficiency and reduce waste but also decrease the frequency of rework, offering substantial cost savings. Additionally, utilizing environmentally sustainable wires and recycling practices further solidifies the responsible use of resources in metal fabrication.
Continual professional development and training in the nuances of MIG welding and solid wire applications underline the journey from competence to expertise. Engaging in workshops and becoming familiar with the latest advancements in wire technology—notably those enhancing feedability and deposition rates—ensures welders remain at the forefront of this ever-evolving field.
In summary, MIG solid wire stands as a testament to the intricate balance between technology and art in modern welding. Its application is deeply rooted in a welder’s expertise and a meticulous approach to process optimization. From selecting the correct wire type and diameter to mastering the influence of shielding gases and parameters, the journey with MIG solid wire is one of precision, authority, and trust. Each weld crafted with this wire narrates a story of skilled artisanship and cutting-edge engineering, embodying quality and reliability forged in metal.