The E7018 low hydrogen electrode has become a cornerstone in modern welding projects demanding both reliability and precision. This premium welding rod stands out for its unique ability to produce clean, strong welds, critical in environments where safety and performance are paramount. This article delves into the specifics of the E7018 electrode, covering its expertise-driven development, real-world applications, and why it holds authoritative prominence in the industry.
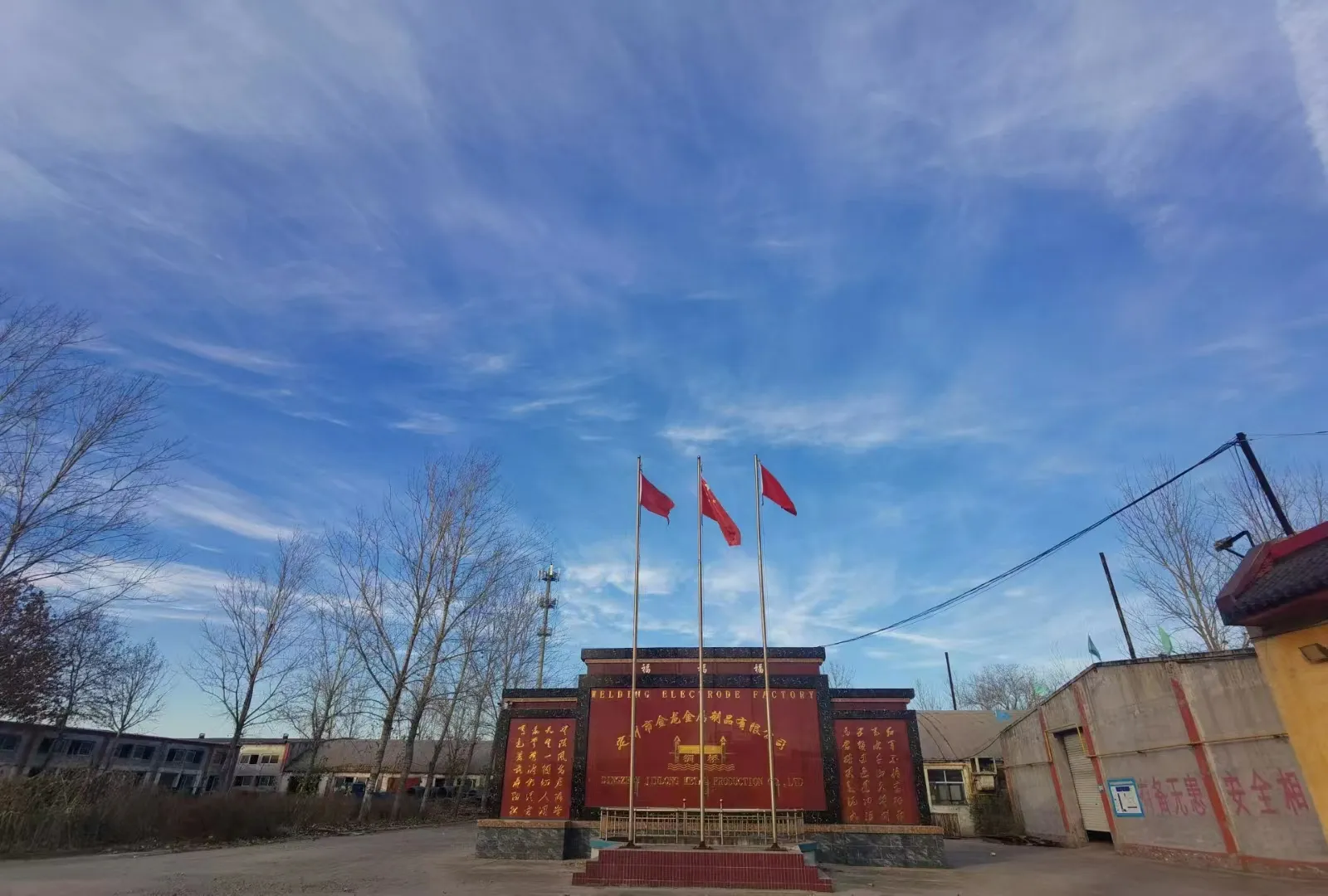
In the realm of welding electrodes, the classification of E7018 carries significant meaning embedded in its nomenclature. The 'E' denotes it as an electrode, with the subsequent numbers providing a wealth of detailed insight into its performance characteristics. The 70 indicates a tensile strength of 70,000 psi, suggesting robustness appropriate for challenging industrial tasks. The 1 signals its versatility in being usable in all positions - flat, horizontal, vertical, and overhead, enhancing its adaptability on complex projects. The final 8 encapsulates its low potassium hydrogen coating, signaling its core attribute as a low hydrogen electrode.
Why does low hydrogen matter? Hydrogen embrittlement has long haunted the world of welding, causing cracks and failures unseen until catastrophic failure. Reducing hydrogen content directly addresses this, enhancing the integrity of the welds. E7018 serves as a guardian against these defects, ensuring projects adhere to structural integrity and pass rigorous safety inspections. Its formulation minimizes the risks of cold cracking, providing a trusted solution in industries such as oil and gas, shipbuilding, and construction.
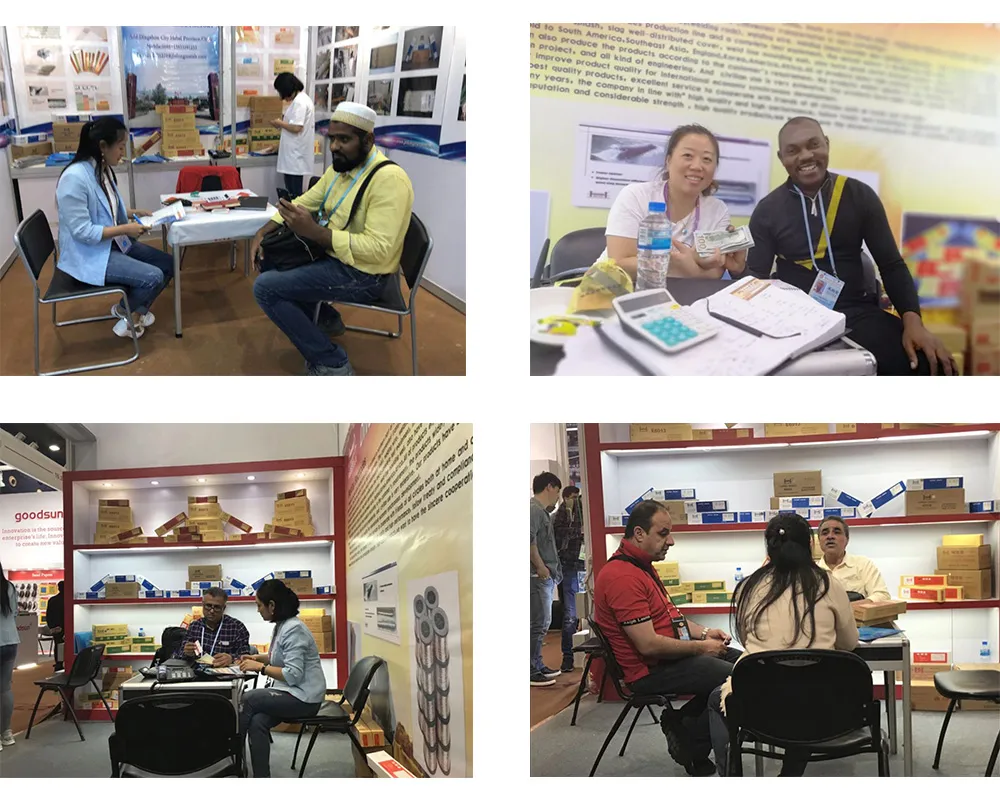
The expertise behind the E7018 involves rigorous testing and refinement. Manufacturers employ stringent protocols during production to ensure low moisture absorption in the electrode coating, as moisture is a potential hydrogen source. This meticulous production process elevates the E7018 above many alternatives, ensuring it is a trusted companion in critical welding tasks.
To appreciate the broad applicability of E7018 electrodes, consider their pivotal role in constructing bridges. Such projects epitomize structural demands where even minor flaws could translate into major dangers. E7018’s ability to deliver defect-free welds is crucial here, reinforced by field testimonials from certified welding inspectors who rely on its predictable performance under varying climatic conditions.
e7018 low hydrogen electrode
The instructional experiences of numerous welders provide further credibility to the E7018 electrode. Seasoned professionals often emphasize the smooth, stable arc and robust slag covering, which are instrumental in preventing weld contamination and boosting overall weld surface finish quality. These experts highlight the electrode's capability to unite a wide range of steel types, including high-strength steels, which often pose challenges to lesser electrodes.
Endorsed by professional bodies and educational institutions, the E7018 electrode serves not only in the field but also in teaching environments where future welders learn the trade's intricacies. Such usage further cements its authoritative status, as it sets a benchmark against which novices can perfect their craft and seasoned experts can continue to refine their techniques.
Trustworthiness, a critical attribute, is another reason the E7018 is favored, as it consistently delivers on its promises. From tackling unpredictable on-site welding scenarios to being a dependable element in high-stakes fabrication shops, this electrode’s consistency is well-documented. Thousands of project logs across industries show the E7018’s role in extending the service life of structures and minimizing maintenance needs, being a cost-effective choice for project managers.
The future of welding continues to evolve,
but the E7018 low hydrogen electrode remains a reliable constant. Its reputation is not just built on historical usage but is continually reinforced by ongoing innovation and a deep understanding of welding science. Manufacturers continue to fine-tune the composition and application techniques, ensuring it meets modern industry demands and environmental regulations.
In summary, the E7018 low hydrogen electrode embodies a blend of professional expertise, proven experience, authoritative endorsement, and unwavering trustworthiness. Its role in modern welding is backed by technical precision and a commitment to safety, making it an indispensable tool in every welder's arsenal. As industries progress, the E7018 will likely continue to adapt and thrive, continually setting standards for new generations of welding professionals.