Unlocking the potential of the E7018 H4R welding rod requires a deep dive into its unique characteristics and applications. This welding rod is often chosen by industry professionals for its reliability and performance. Known for its low hydrogen content, the E7018 H4R welding rod effectively minimizes the risk of weld cracking, especially when dealing with high-stress applications. This feature makes it a top choice in structural work, bridges, and other critical engineering projects where safety and durability are paramount.
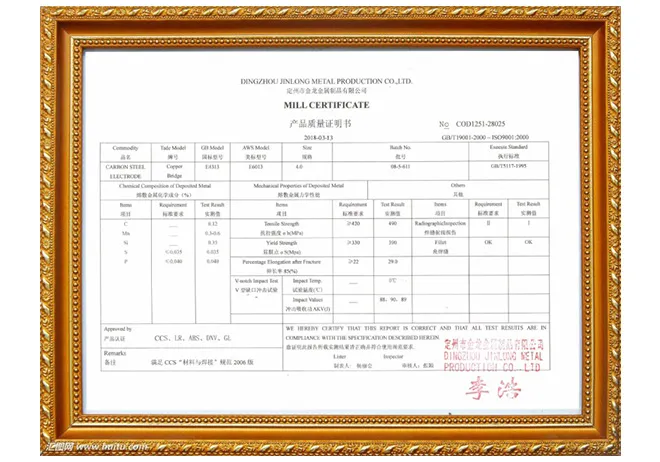
The primary strength of the E7018 H4R welding rod lies in its composition and usability. It is an iron powder, low-hydrogen electrode that provides excellent deposition rates. This attribute makes it particularly useful for situations where speed without sacrificing the quality of the weld is necessary. Professionals appreciate the smooth arc it produces, which translates to less spatter and easier clean-up, enhancing productivity in large-scale operations.
When considering the professional use of the E7018 H4R, its versatility stands out. It can be used in all positions, offering flexibility for various welding scenarios. This adaptability means it can handle both small repairs and extensive welding tasks with equal competence. Moreover, the E7018 H4R is often used in both AC and DC applications, further exhibiting its flexibility and effectiveness under different electrical conditions.
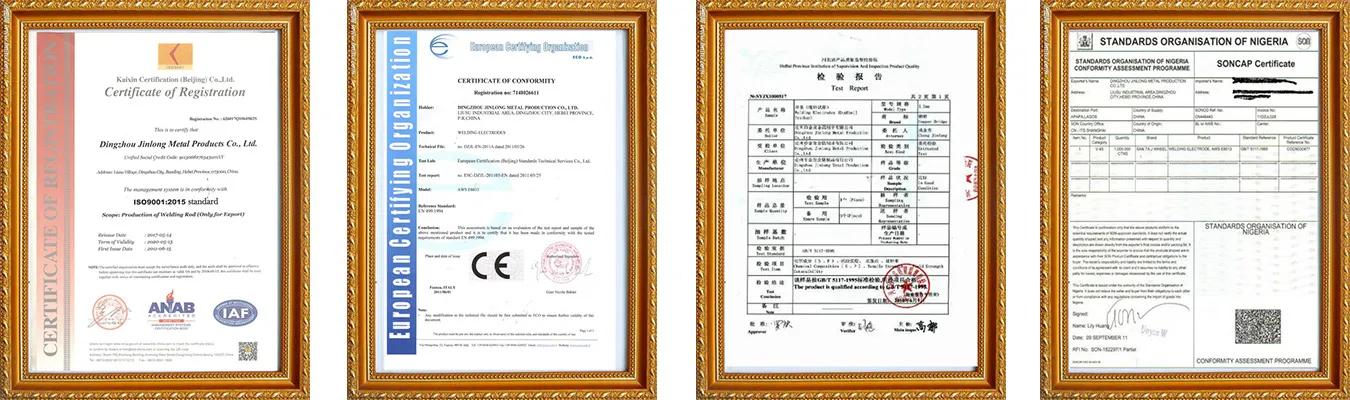
In terms of professional expertise, understanding the proper storage and handling of the E7018 H4R is crucial. The rod’s low hydrogen characteristics can be compromised if it is exposed to moisture. To maintain its integrity, it should be stored in a dry, heated environment, typically above 250°F. This precaution ensures that the welds produced will meet the highest standards of quality and safety, adhering to industry regulations and contractor specifications.
e7018 h4r welding rod
The expertise of seasoned welders also highlights the importance of pre-heating and post-weld heat treatment when using the E7018 H4R. These processes help reduce residual stress and the possibility of cracking in high-strength steels. In complex structures where multi-pass welds are required, understanding the intricacies of heat management is essential to preserving the properties of the weld and the base material.
Authoritativeness in the field is underscored by the widespread use of the E7018 H4R across high-stakes projects globally. This welding rod is trusted by engineering experts for infrastructure developments that require the utmost precision and reliability. Its role in such projects affirms its standing in the industry, earning it a place among the most recommended electrodes by professional welding associations and certification bodies.
Trustworthiness in the E7018 H4R’s performance is backed by numerous certifications and adherence to international welding standards. Its consistent track record in providing sound welds is documented in myriad job sites, from sprawling skyscrapers to intricate bridge constructions. Testimonials from seasoned welders and project managers often cite the reliability of E7018 H4R as a key factor in their successful project completions, reinforcing its reputation as a dependable choice for critical welds.
In conclusion, the E7018 H4R welding rod serves as more than just a tool in a welder’s arsenal; it is a testament to the blend of science and skill in modern construction and repair. Its composition, flexibility, and reliability make it an indispensable part of complex welding jobs. With the right handling and application techniques, this welding rod can foster success in projects requiring the utmost safety and durability. For any professional seeking to enhance their craftsmanship, understanding and utilizing the E7018 H4R effectively is a significant step towards mastering the art of welding. The consistent performance of E7018 H4R ensures that it remains a top recommendation for all levels of welding tasks, backed by proven reliability and widespread industry approval.