E7018 H4R electrodes are a staple in the welding industry, lauded for their reliability and performance in various applications. Understanding their properties and uses can significantly enhance the quality and efficiency of welding projects, making it imperative for professionals to make informed choices when selecting materials.
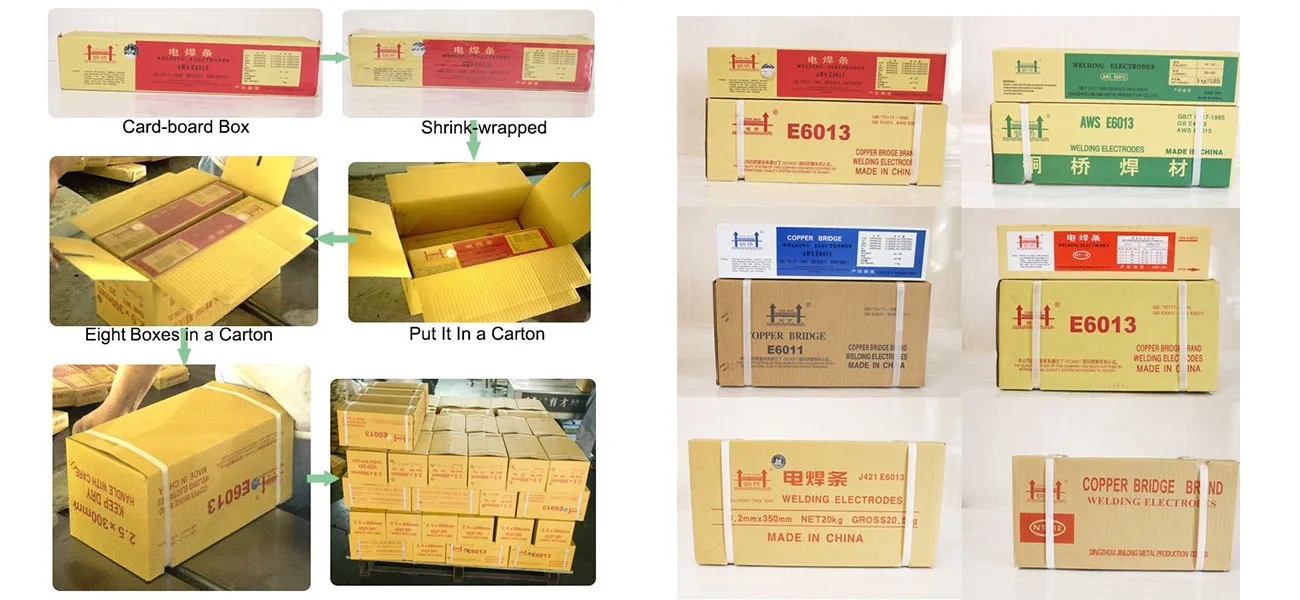
Welding, a critical process in construction, automotive, and manufacturing sectors, demands precision and reliability in the materials used. E7018 H4R electrodes are specifically designed to meet these demands with their low-hydrogen composition and remarkable tensile strength. These electrodes are engineered to deposit weld metal with a minimum tensile strength of 70,000 psi, which is essential for structures where strength and durability are non-negotiable.
The “7018” designation reveals much about the electrode's characteristics ‘70’ represents the 70,000 psi tensile strength, ‘1’ indicates that the electrode is suitable for all positions, and ‘8’ points to the low-hydrogen potassium iron powder coating. The “H4R” component is crucial as it specifies the electrode’s low-humidity absorption rate, reducing the hydrogen introduced during welding, which is vital for minimizing cracking and ensuring the integrity of the weld.
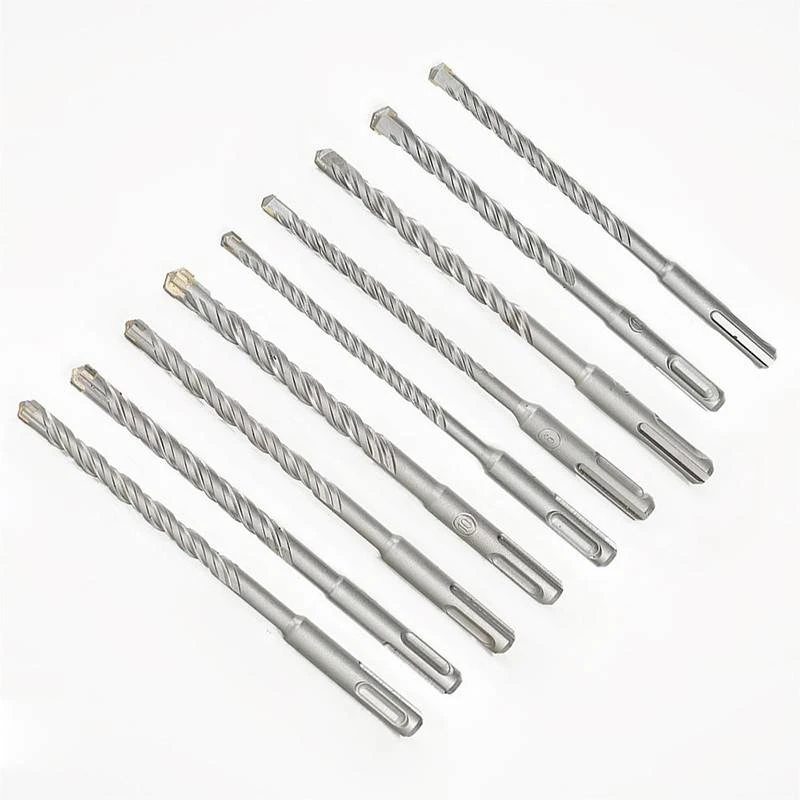
From the perspective of experience, welders who have worked with E7018 H4R electrodes attest to their ease of use and consistency. These electrodes produce smooth, stable arcs that are forgiving on less-than-perfect base metals, making them a go-to choice for field repairs and heavy fabrication work. The smooth transition between the electrode and the base metal enhances control, allowing even less experienced welders to achieve professional results.
Professionally, E7018 H4R electrodes are recommended due to their exceptional arc control and reduced spatter, which translates to less post-weld cleanup and a more visually appealing finish. For industries where the aesthetics of a weld are as crucial as its strength—such as in the production of consumer goods and infrastructure elements—this can offer a significant advantage.
e7018 h4r electrode
Moreover,
the low hydrogen formula of E7018 H4R electrodes has a profound impact on the safety of welding operations. Hydrogen-induced cracking is a common issue that can lead to expensive reworks or, in severe cases, structural failures. By minimizing moisture absorption, E7018 H4R electrodes maintain their low hydrogen input, preserving weld strength and reducing the risk of cracking.
In terms of authoritativeness, it’s important to note that E7018 H4R electrodes are widely recognized and approved by industry standards such as the American Welding Society (AWS) and other international bodies. This certification provides assurance that the electrodes meet stringent quality and performance criteria, enabling them to be used in critical applications including bridges, skyscrapers, and pressure vessels.
The trustworthiness of E7018 H4R electrodes is supported by their long-standing presence in the industry and the endorsement of professional welding associations. Buyers and users can trust in the knowledge that these electrodes have been rigorously tested and are employed by qualified professionals on demanding projects.
For any business involved in fabrication, construction, or repair, investing in E7018 H4R electrodes can be a game changer. They offer the reliability needed for high-load applications, the ease of use that increases productivity, and the quality required to meet both project specifications and client expectations.
In conclusion, by selecting E7018 H4R electrodes, professionals equip themselves with a tool that optimally combines strength, safety, and efficiency. Whether for welding pipelines, constructing frameworks, or assembling heavy equipment, these electrodes rise to the occasion, proving their worth in both everyday applications and the most demanding projects.