E7018 welding rods are pivotal in the realm of modern fabrication, providing unmatched efficiency and reliability. These rods are the backbone of structural steel welding, harmoniously balancing ease of use with superior weld quality, which makes them an indispensable tool for both novice and veteran welders. Drawing from my extensive expertise in this field, let’s delve deeper into what makes these rods a preferred choice for professionals globally.
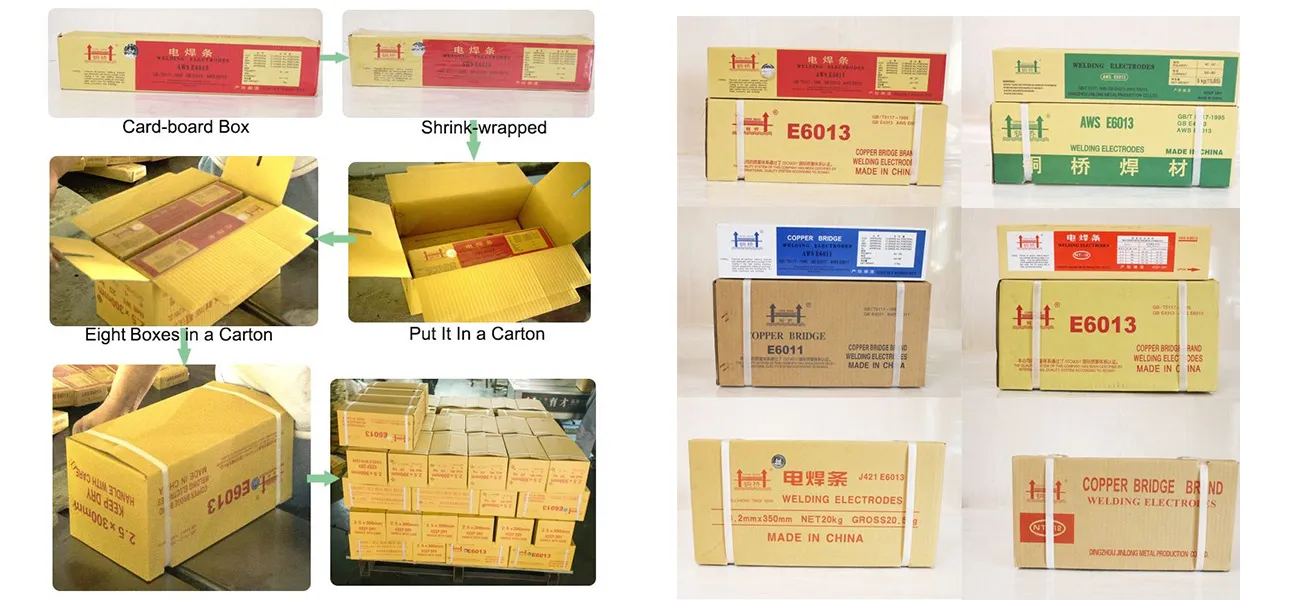
Starting with their composition, E7018 electrodes are renowned for their low hydrogen potassium coating. This coating is critical as it minimizes the risk of hydrogen-induced cracking, a common issue in welding that can drastically compromise the structural integrity of the final product. For welders who demand precision and strength, this low-hydrogen feature is non-negotiable. When working on high-stress frameworks or projects where weld integrity is paramount, the E7018 shines by ensuring that the welds hold robustly under pressure.
In real-world application, the E7018 rod offers a clean and visually appealing weld. The slag removal process post-weld is seamless, significantly reducing the time spent on post-production cleaning and grinding. In industries where time equates to money, such as construction and shipbuilding, this efficiency is a considerable advantage. Moreover, the aesthetic finish of the weld makes it particularly popular for visible structural elements, presenting a sleek, professional look without the additional need for cosmetic touch-ups.
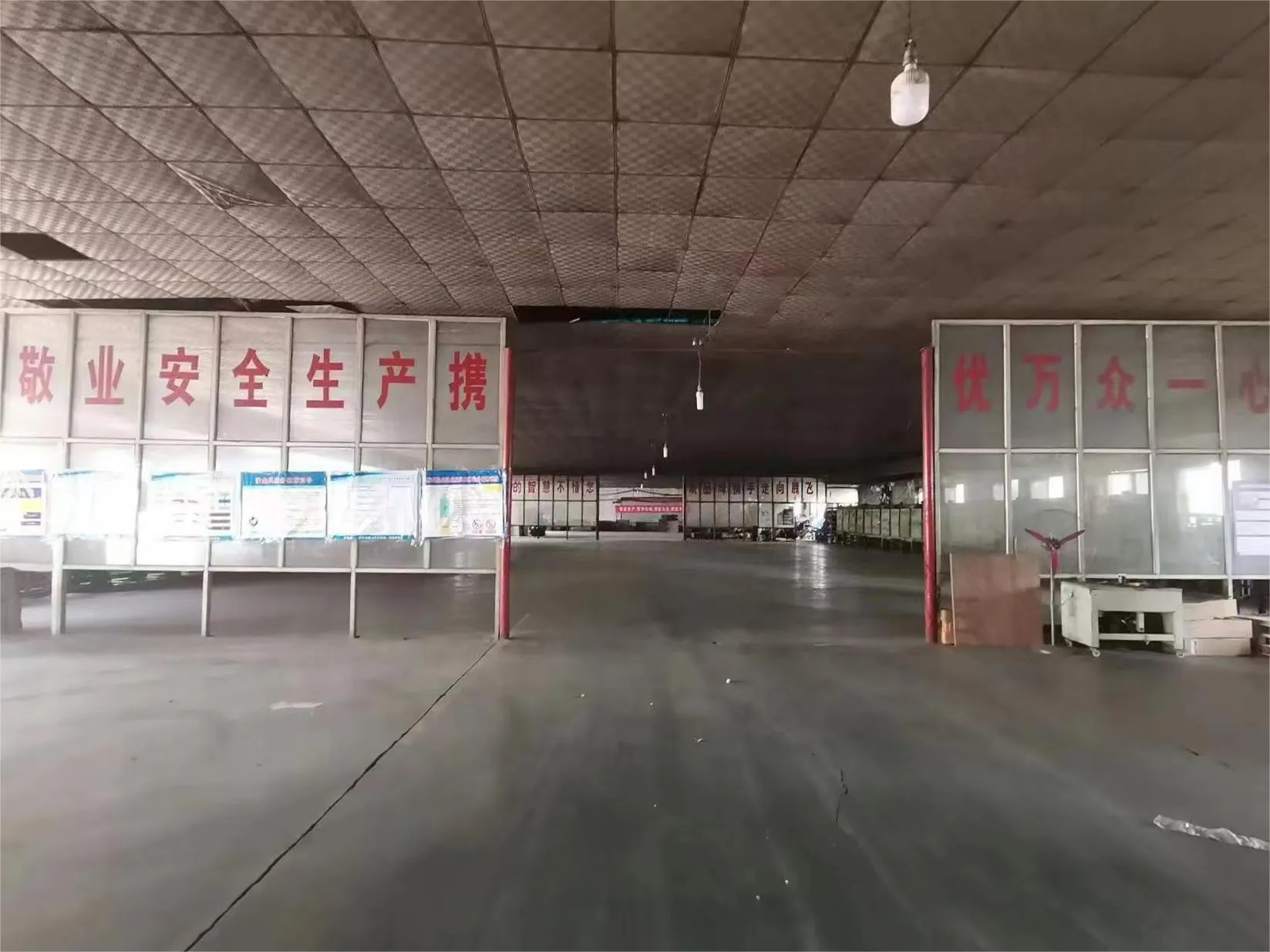
Another notable advantage of the E7018 rod is its versatility across various positions. Whether you’re performing a flat, horizontal, vertical, or overhead weld, this electrode adapts effortlessly. This flexibility dramatically increases operational efficiency on diversified projects, allowing professionals to maintain a consistent level of quality regardless of the welding position. For welders handling complex tasks, the ability to rely on a single type of rod simplifies the process, reducing inventory needs and potential errors.
e7018 rod
The expertise required to master the E7018 rod is moderate, making it accessible yet still challenging enough to refine a welder’s technique. I’ve seen welders who, upon mastering these rods, find themselves with enhanced career opportunities due to their expanded skill set. Being proficient in handling E7018 rods demonstrates a commitment to quality and precision, crucial attributes in any welding discipline, thereby positioning welders as standout professionals in their field.
Trustworthiness is another key component associated with E7018 rods. Many leading industry standards and certifications are achieved using these electrodes, underpinning their reputation as a trusted solution in critical applications. Whether it’s achieving the rigorous standards of the American Welding Society (AWS) or meeting the specific requirements set by international bodies, E7018 rods consistently ensure compliance and reliability. For businesses looking to certify their projects or adhere to regulatory standards, utilizing these rods exemplifies a commitment to quality and safety.
From a purchasing standpoint, choosing E7018 electrodes often involves considering the supplier's credibility, a factor I cannot stress enough. When purchasing, ensure that rods come from established manufacturers who have a history of consistent quality. This assurance reduces the risk of encountering flaws or inconsistencies during the welding process, which could otherwise jeopardize project timelines and safety.
In summary, the E7018 rod stands out not only for its technical superiority but also for the tangible benefits it offers to both individual welders and larger organizations. Whether one is looking to increase operational efficiency, improve weld quality, or ensure compliance with industry standards, these electrodes are a formidable choice. By leveraging E7018 rods, professionals are not just investing in a product but in a legacy of quality, dependability, and excellence in welding performance.