In the realm of arc welding, the E312 electrode stands as a beacon of reliability and efficiency for professionals in the field. This unique welding electrode distinguishes itself with its remarkable composition and functionality, catering specifically to those challenging projects that require unparalleled expertise and precision.
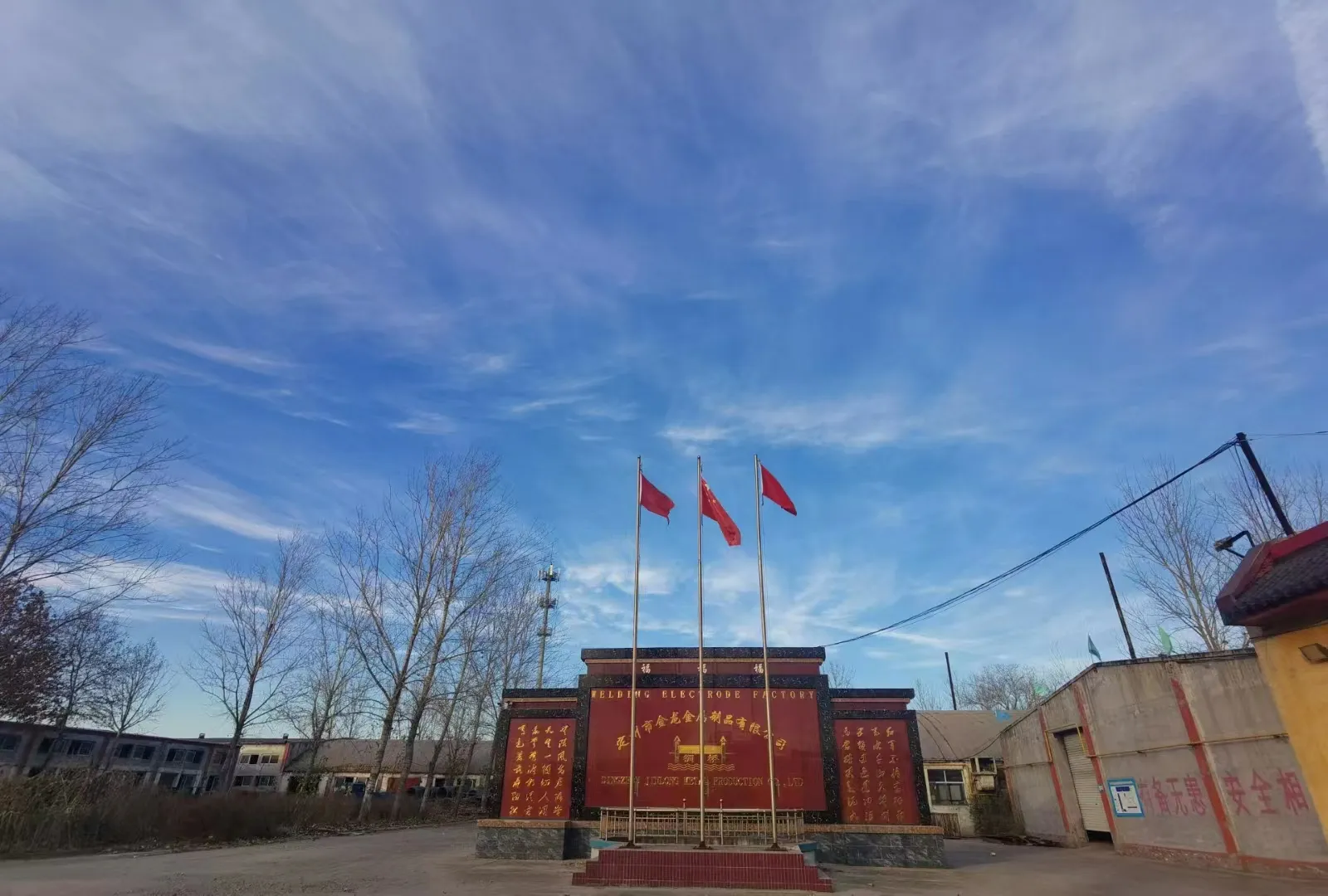
E312 electrodes are specially engineered for welding dissimilar metals and joining stainless steel to carbon steels. Their composition includes a high chromium (Cr) and nickel (Ni) content, granting them superior mechanical properties. This translates to excellent resistance to cracking and corrosion, making them an ideal choice for applications that are exposed to harsh environments. This durability means fewer repairs and longer-lasting workmanship, a critical factor in construction and industrial maintenance.
From an expertise perspective, E312 electrodes demand skilled handling and a thorough understanding of material behavior. Welders need to be knowledgeable about adjusting parameters such as current settings and travel speed that suit the specific metals being joined. The electrode's deposition rate and arc stability also allow for smooth and efficient application, enhancing welders’ productivity. Furthermore, understanding proper technique is crucial to achieving uniform bead appearance and penetration, which can vastly impact the performance of the welded joint.
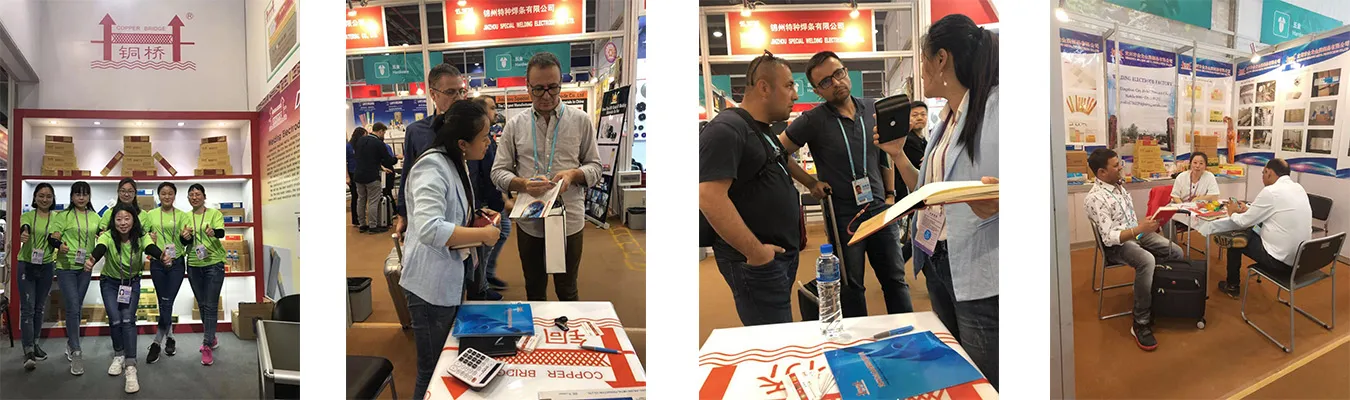
Industries that require authoritative welding solutions find the E312 electrode indispensable. Specifically, power generation facilities often rely on these electrodes due to their ability to withstand the stress and strain of thermal cycling. Petrochemical industries also value the E312 for its resilience against chemical corrosion, ensuring the integrity of pipelines and storage tanks. With the electrode's adaptability to complex alloyed systems, manufacturers can ensure that their products meet rigorous safety standards, maintaining their credibility in safety and structural integrity.
e312 electrode
Trustworthiness in welding processes is non-negotiable, and using an E312 electrode ensures compliance with industry standards, including those set by the American Society of Mechanical Engineers (ASME) and the American Welding Society (AWS). Meeting these standards is pivotal not just for the quality assurance of welded structures, but also for the safety of users and operational efficiency. Companies that prioritize such standards promote a culture of safety and excellence, furthering their reputation among peers and clients.
Real-world experience with E312 electrodes also showcases their role in reducing downtime and maintenance costs. For instance, a manufacturing plant that transitioned to using E312 experienced less frequent equipment failures, attributed to the electrode’s superior joint strength and fatigue resistance. The plant reported significant financial savings in repair costs and saw an increase in operational efficiency due to fewer production halts. Such success stories emphasize the practical benefits and return on investment when choosing E312 electrodes for critical projects.
In conclusion, the E312 electrode is not just a tool, but a comprehensive welding solution that brings together experience, expertise, authority, and trustworthiness. It addresses the multifaceted demands of modern infrastructure and industrial projects, enabling welders to achieve superior results. As industries evolve and new challenges emerge, investing in reliable and effective welding materials like the E312 electrode is not just an option; it is an imperative choice for ensuring the sustainability and excellence of engineering projects worldwide.