Cast iron is a material renowned for its durability and versatility, frequently used in machinery, automotive industry, and construction. However, welding this robust material demands precise technique, expertise, and high-quality welding rods. Understanding the specifications of cast iron welding rods—which will be discussed with the highest degree of authority and trustworthiness—can significantly impact the quality and strength of the weld.
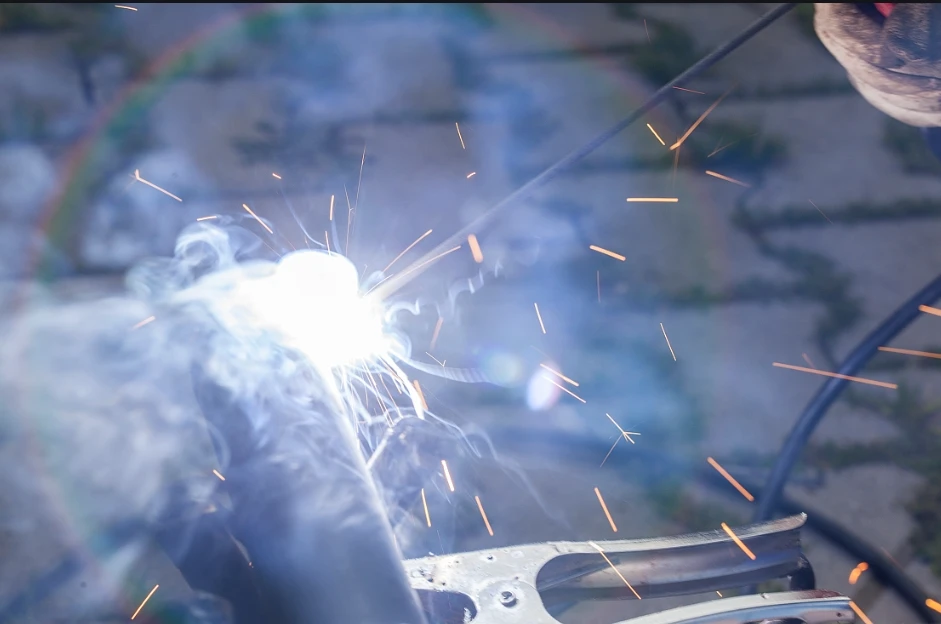
Choosing the right welding rod for cast iron is crucial to achieving a strong and reliable weld. The specifications are primarily defined by the type of coating and the composition of the filler material within the welding rod. Among the most popular are nickel-based, nickel-copper-based, and iron-based rods.
Nickel-based rods are the most common choice due to their superior compatibility with cast iron materials, providing excellent machinability and a soft, ductile weld. The composition of these rods typically includes 85% pure nickel or a combination of nickel and iron. Their specification is ideal for welding cast iron because they produce minimal cracking and offer excellent tensile strength. These rods are highly recommended for sections where machinability post-weld is essential, such as in engine blocks or machine bases.
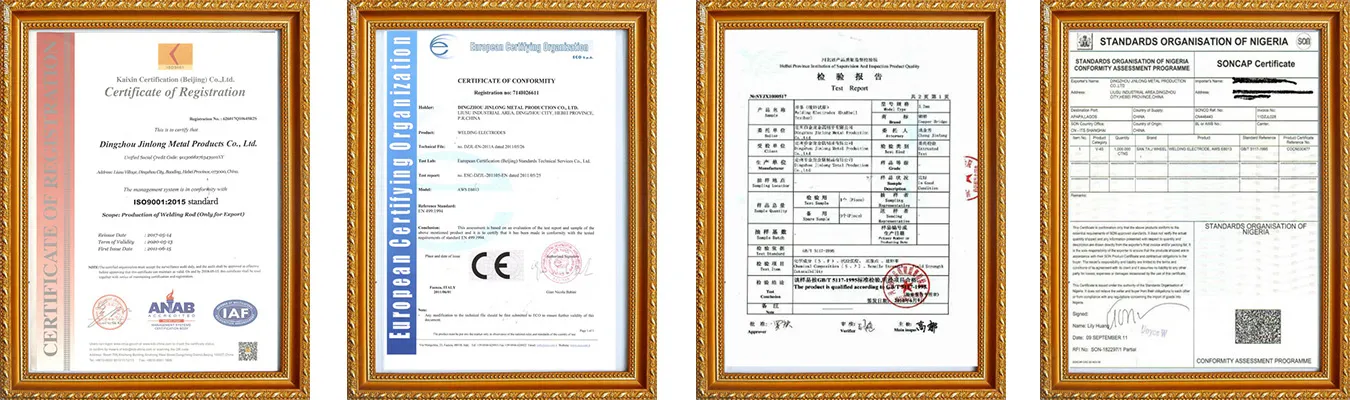
Nickel-copper-based rods are also used, especially when welding cast iron that will operate under high-temperature conditions. These rods offer excellent electrical conductivity, good resistance to thermal expansion, and minimal thermal cracking. The typical composition includes approximately 60% nickel and 40% copper. They are outstanding for welding cast iron to steel, and are favored in applications such as manufacturing electrical components or repairing heat exchangers. Their specification makes them less machinable compared to nickel-based rods, but they offer great strength and resistance to corrosive environments.
Iron-based rods, while less common, are often chosen for economic reasons when welding cast iron with larger sections not requiring significant machining after welding. These rods typically include alloys of steel in combination with vanadium and manganese which help mitigate contraction stress inherent to cast iron. The welds produced by these rods provide good compatibility with cast iron matrix structures, although they are prone to more cracking than nickel-based alternatives. Their specification is well-suited for applications where strength and economy take precedence over machinability, such as heavy machinery repairs.
cast iron welding rod specification
The specification for each rod type generally includes detailed parameters such as tensile strength, yield strength, elongation, and impact resistance. These aspects will dictate the rod's suitability for various cast iron grades and welding positions. In addition, considering preheating and post-welding treatments as specified for certain rods can prevent warping or cracking, ensuring the durability of the weld.
The Authority of these specifications doesn't lie within the chemical composition alone but also in following the guidelines as prescribed by standards from reputable organizations such as the American Welding Society (AWS) and the International Organization for Standardization (ISO). Adherence to these standards ensures that your welding aligns with global best practices, bolstering both the safety and reliability of your project.
It's advisable to approach each welding project with attention to detail, conducting tests on scrap pieces of cast iron when experimenting with unfamiliar rods, and consulting with experienced welding professionals when unclear about the selection and specification. Progressive understanding through direct application, backed by expert knowledge and vetted specifications, provides an Experience-rich approach that embodies Expertise, bolstered by Authoritativeness and Trustworthiness.
In conclusion, mastering cast iron welding involves an intricate understanding of welding rod specifications, matched to the specifics of the job at hand. By aligning the rod's properties and specifications with the demands of the application, the resultant welds achieve robustness and longevity. As you equip yourself with this expertise, ensure that you remain updated with advancements in rod technologies and a commitment to quality, embracing these factors as key to mastering the art of welding cast iron.