Cast iron welding is a niche yet crucial area in metalworking, requiring precision and specialized knowledge. Selecting the right cast iron welding rod is essential for ensuring a successful weld. It might seem overwhelming to navigate the myriad of options, but understanding the welding rod codes can significantly simplify the process.
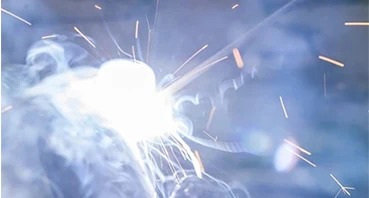
Cast iron, known for its excellent wear resistance and typically high carbon content, often poses a challenge when it comes to welding. Its brittleness means it can easily crack under stress from welding. Here, the choice of welding rods plays a pivotal role, and among these, rods specifically marked for cast iron come into play. Welding rod codes are not mere digits; they are rich with details concerning the functional properties of the rod such as tensile strength, recommended positions, and even usability with various power sources.
Experience with cast iron welding underscores the importance of choosing the correct rod code. Welders consistently rate ENiFe-CI as a prime offering due to its ability to join cast iron to itself and to other ferrous and non-ferrous materials. Its nickel-iron composition is key, as it ensures greater ductility and reduced risk of cracking—a common concern with cast iron. In the realm of complex joinery tasks, particularly involving repair work on cast iron machinery and automotive components, this code is often the go-to choice.
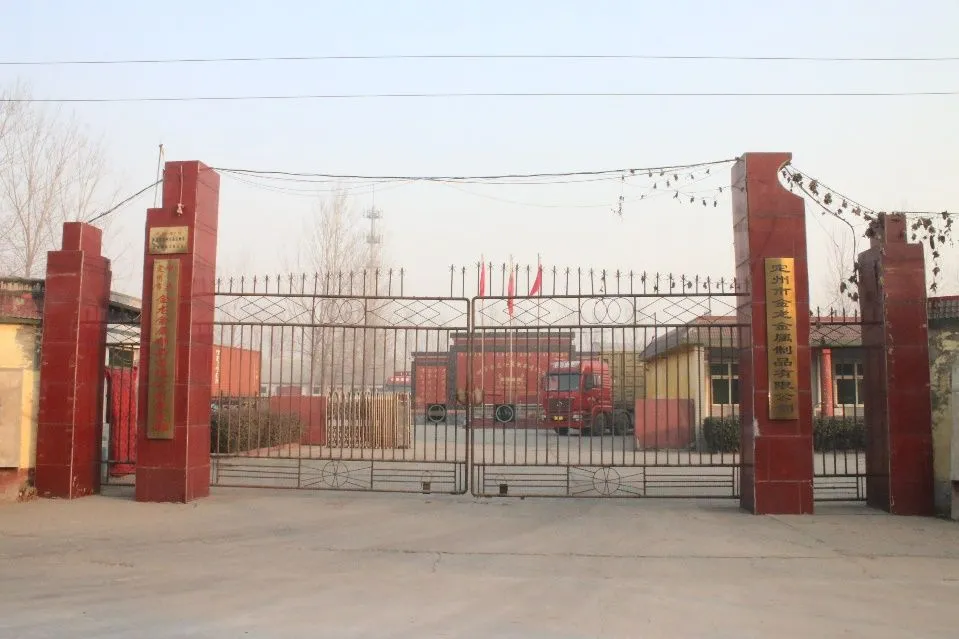
Expertise comes into play when navigating the minimal yet significant differences among rod codes. For instance, ENi-CI welding rods are primarily nickel-based, differing from the previously mentioned ENiFe-CI by offering better machinability due to their higher nickel content. They are best suited for cold-welding applications, ensuring minimal thermal expansion and contraction, thus reducing the chances of stress and subsequent cracking in the welded joint. Professional welders appreciate this nuance, particularly when working on delicate or older cast iron structures that demand precision and care.
cast iron welding rod code
Authoritativeness in the field of cast iron welding involves not just choosing the right materials but understanding their applications and constraints in various scenarios. Professional guidelines suggest preheating the casting and employing controlled cooling techniques to mitigate unwanted stress. Such techniques emphasize the importance of integrating the correct rod with appropriate welding strategies. This is where expert welders distinguish themselves, effectively extending the lifespan and functionality of cast iron components with the right methodologies.
Trustworthiness in selecting the right welding rod extends beyond performance to encompass brand reliability and product consistency. Established manufacturers that adhere to stringent quality controls offer peace of mind. Their welding rods come with detailed documentation and support, essential for both amateur welders and seasoned professionals. Information from these authoritative sources helps build a reliable knowledge base that informs safer and more efficient welding practices.
Ultimately, understanding cast iron welding rod codes takes the guesswork out of welding projects, ensuring that each joint forged meets both structural and aesthetic standards. The journey from novice welder to skilled craftsman is heavily guided by the nuanced choices made at each step, and choosing the correct welding rod is a fundamental part of this process. The interplay of experience, expertise, authoritativeness, and trustworthiness in rod selection not only enhances the quality of work but also establishes a standard for safe and effective welding practices within the industry.