Selecting the right cast iron welding electrode is crucial for achieving reliable and high-quality welds, especially given the unique challenges posed by cast iron’s composition. Each welding situation demands attention to detail, expertise, and an understanding of various electrode specifications to ensure the best results, particularly in industrial and repair settings.
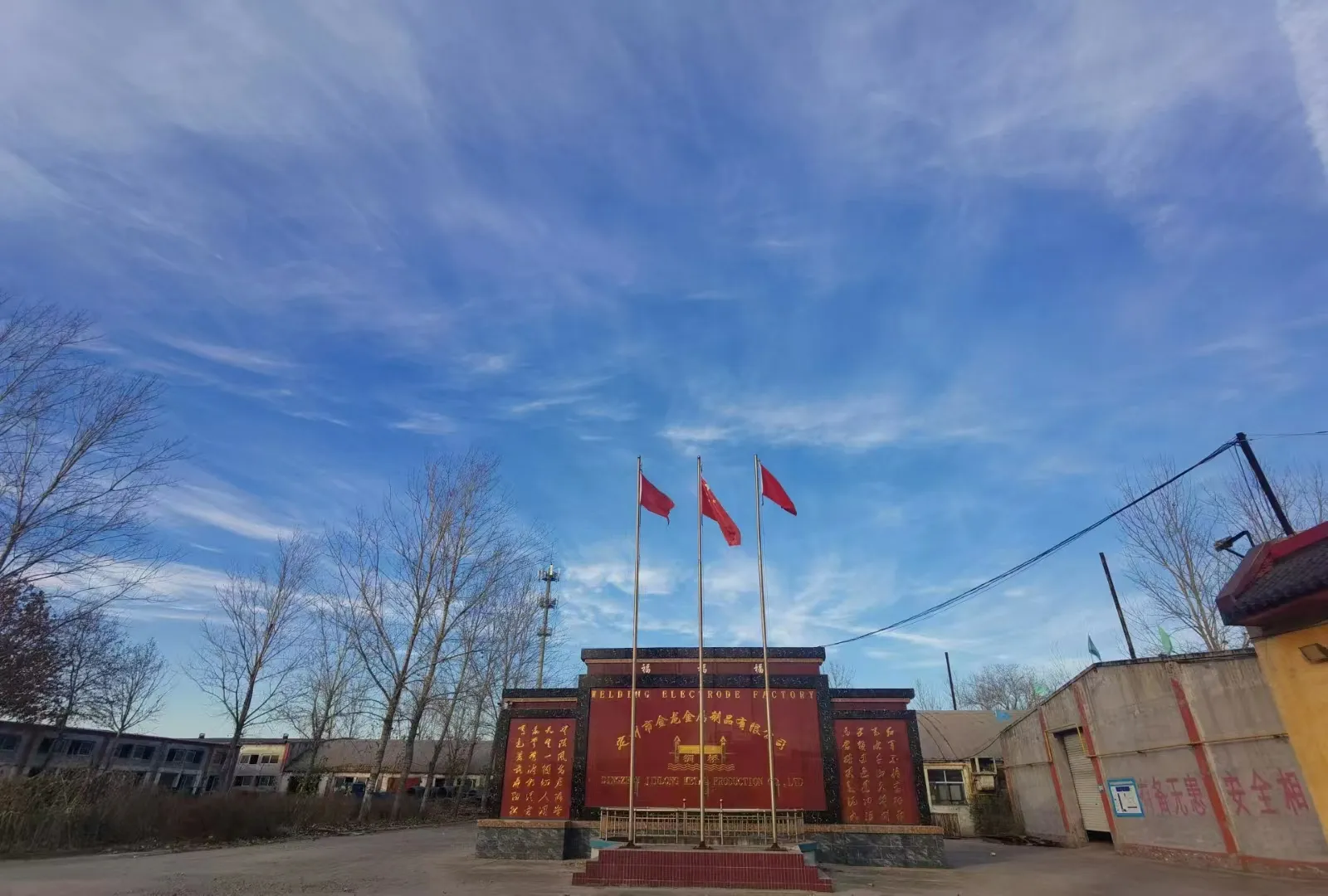
Cast iron, known for its high carbon content and brittleness, presents distinct challenges when welding. It is prone to cracking if cooled too rapidly, and its impurity levels can complicate welding processes. Consequently, choosing the right welding electrode is pivotal for overcoming these challenges. Therefore, a comprehensive understanding of electrode specifications will not only improve weld durability but also enhance structural integrity.
Nickel-based electrodes are a prominent choice for cast iron welding. Nickel’s ductility makes these electrodes less susceptible to cracking, which is a common issue with cast iron. The nickel content facilitates a more malleable weld, allowing for slight movements that occur as the material cools. It is essential to look for electrodes featuring high nickel content, typically around 55% to 99%, to ensure flexibility and strong bonding with cast iron surfaces.
The AWS specification AWS A5.15 ENi-CI is often used for pure nickel electrodes, which provides high machinability and strong crack resistance, making it ideal for welding gray cast iron, high-phosphorus iron, and repair of casting defects.
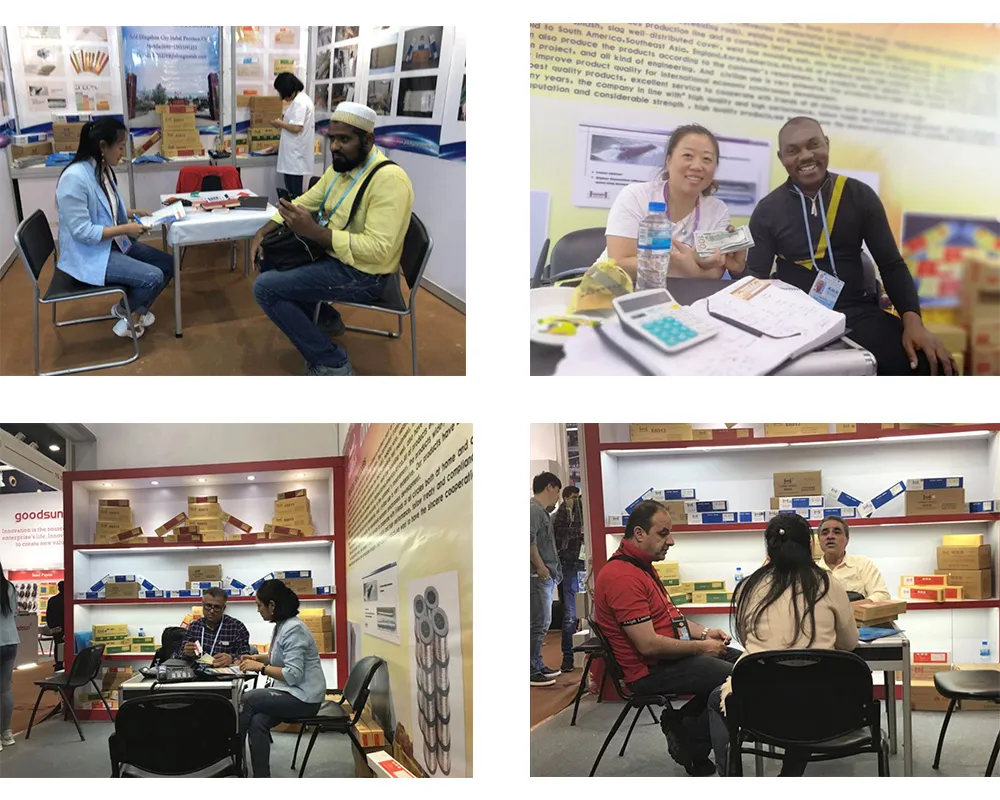
A second category is nickel-iron electrodes, which include a reduced nickel content but add iron to the mix. Commonly specified as AWS A5.15 ENiFe-CI, these electrodes typically contain 40% nickel and 60% iron. This composition results in a stronger yet tougher bond, making them well-suited for joining cast iron to other ferrous metals. They also match thermal expansion rates more closely to the base cast iron, reducing stress concentrations and elevating machinability after welding. Their use is particularly beneficial in structural applications where strength is as crucial as flexibility.
For applications where cost-efficiency is essential, such as large repair jobs or areas experiencing wear, steel or iron-based electrodes can be selected. These offer an economical solution with good mechanical strength but may require preheating and controlled cooling to avoid cracking due to higher hardness in the weld metal. AWS A5.15 ESt-CI is a common specification for these electrodes, offering good compressive strength, although they may need to be used alongside post-weld heat treatment to relieve stresses and reduce the occurrence of cracking.
cast iron welding electrode specification
The choice of electrode also involves considering the specific type of cast iron involved. For instance, ductile iron, due to its nodular graphite structures, requires more flexibility in the weld deposit, while white cast iron, known for its hardness and brittleness, demands a methodical pre-and post-weld treatment process irrespective of the electrode type chosen.
Always consider the thermal characteristics of cast iron. Preheating is an essential step when welding with all types of electrodes unless the electrode specifications suggest otherwise. Depending on the iron's composition and thickness, preheating temperatures can range from 200°F (93°C) to 600°F (316°C). Gradual heating reduces the thermal shock and stress that can lead to cracking.
In addition to the chemical composition, electrode diameter, and current requirements are significant factors that must be aligned with the weld's requirements to ensure precise penetration and deposition rates. Each electrode establishes its specifications in terms of these parameters, which will affect overall weld quality and need careful optimization.
With careful consideration of electrode specifications tailored to specific welding conditions, professionals can achieve optimal results. Always consult with manufacturers or welding specialists when in doubt, as their expertise often encompasses advanced understanding of nuanced specification changes, ensuring you maintain a high standard of quality and performance in your welding projects.