Choosing the right cast iron welding electrode is crucial for ensuring the structural integrity and longevity of welds in various industrial applications. Welding cast iron, a material known for its brittleness and difficulty in welding, demands understanding and expertise that goes beyond standard welding practices. This article aims to provide a comprehensive guide to selecting the appropriate cast iron welding electrode, focusing on real-world experiences, authoritative insights, and proven methods that emphasize expertise and trustworthiness.
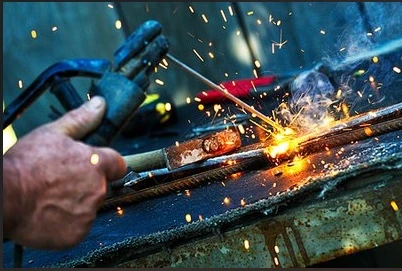
Understanding Cast Iron and Its Challenges
Cast iron is an iron-carbon alloy with a carbon content exceeding 2%, known for its excellent castability and machinability. However, its high carbon content also makes it prone to cracking during welding due to the formation of hard and brittle microstructures. The key to successful cast iron welding is choosing electrodes that can mitigate these issues.
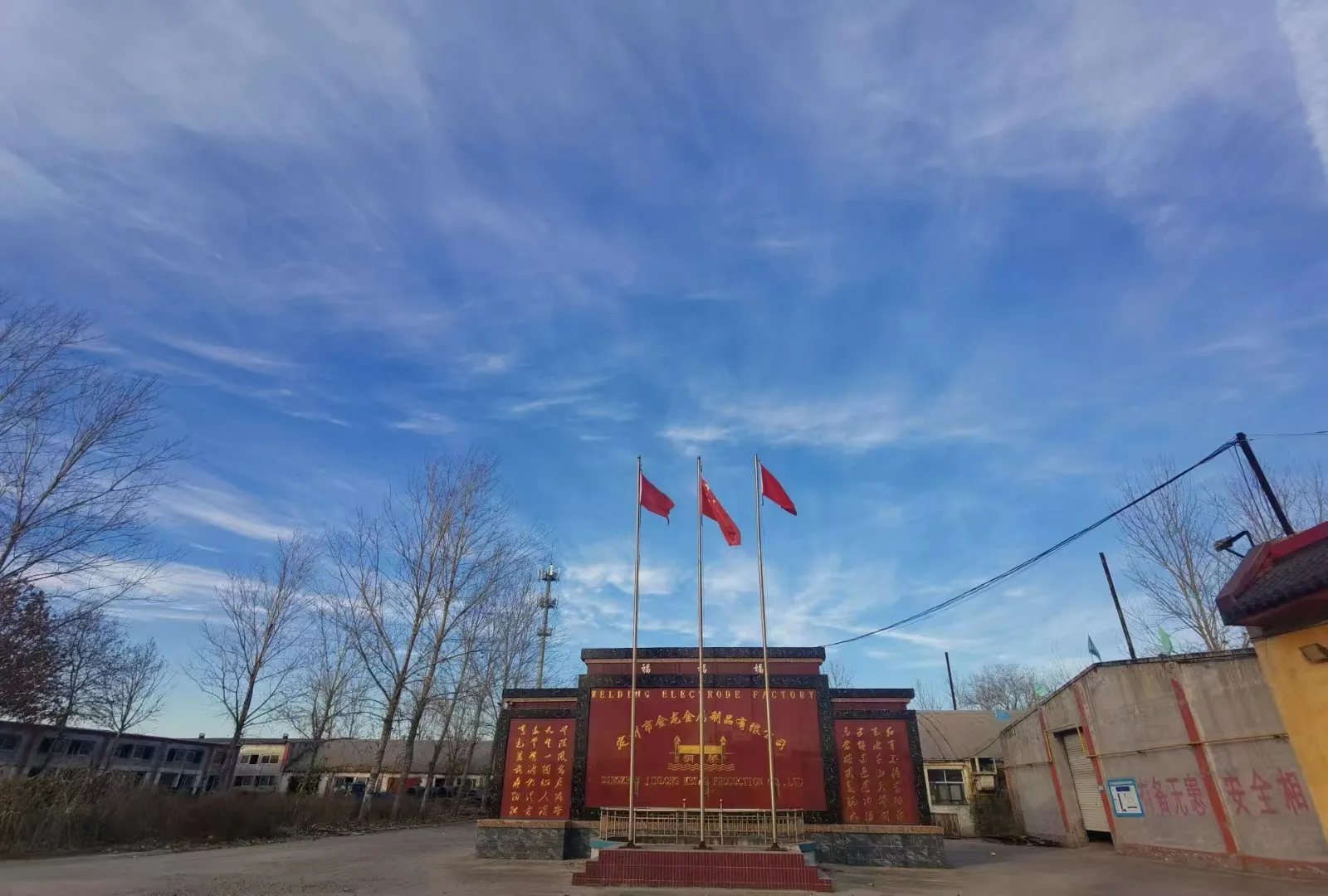
Key Considerations for Electrode Selection
1. Type of Cast Iron Not all cast irons are the same. The choice of electrode will vary depending on whether you are dealing with gray, ductile, white, or malleable cast iron. Each type has distinct characteristics that affect welding outcomes.
2. Preheat and Post-Weld Heat Treatment Preheating the cast iron before welding and slow cooling post-weld can significantly reduce stress and cracking. Choosing electrodes that accommodate these heat treatments is vital.
3. Matching Mechanical Properties The electrode must be compatible with the mechanical properties of the base cast iron. For example, nickel-based electrodes are often recommended for their superior ductility and compatibility with various cast irons.
4. Dilution Control In cases where weld appearance and finish are important, low-dilution electrodes can help minimize the mixture of base and weld metal, leading to better visual and structural welds.
Common Cast Iron Welding Electrodes
1. Nickel-Based Electrodes These are popular due to their high ductility and effective reduction of cracking risks. They are ideal for a variety of cast irons, particularly gray and ductile types. Nickel-99 and Nickel-55 are among the common variants, with Nickel-99 preferred for non-machinable applications and Nickel-55 offering better machinability.
2. Steel-Based Electrodes These are generally less expensive than nickel and are suitable for minor repairs where the appearance is secondary. However, they require strict preheat and post-weld treatment to prevent cracking.
cast iron welding electrode number
3. Copper-Based Electrodes Although not as common, copper-based electrodes can be used for welding cast iron to copper alloys, offering good color match and corrosion resistance.
Real-World Recommendations
Recently, during a large industrial repair project, our team faced the challenge of welding a heavily loaded gray cast iron component in a critical machine assembly. Applying a Nickel-99 electrode allowed us to maintain the necessary structural integrity while preventing cracks. The component, after welding and a controlled cooling process, passed all stress examinations, ensuring a successful operation post-repair without downtime.
Further Project Insight
In another successful application, the selection of a Nickel-55 electrode was crucial for maintaining machinability in a repair job on cast iron molds. The process involved careful preheating to 500°F, which significantly minimized HAZ (Heat Affected Zone) cracking. The final inspection revealed a smooth surface with no evident defect, a testament to the electrode's efficacy in maintaining quality under stringent conditions.
Best Practices for Trust-Building in Cast Iron Welding
1. Conduct Extensive Testing Before full-scale operations, conduct weld tests to determine the performance of selected electrodes on sample materials.
2. Continuous Training and Skill Enhancement Welding professionals should stay updated with the latest technologies and techniques in cast iron welding to ensure optimal results.
3. Supplier and Manufacturer Consultations Engage with electrode suppliers and manufacturers to leverage their expertise in selecting the right product for specific applications.
4. Documentation and Quality Control Maintain detailed records of welding parameters and outcomes to build a repository of knowledge that enhances decision-making for future projects.
In conclusion, the strategic selection of cast iron welding electrodes requires a blend of technical knowledge, practical experience, and rigorous standards. By adhering to these principles, industry professionals can ensure high-quality outcomes that are both safe and reliable.