Choosing the right welding electrode for cast iron to cast iron applications is a critical decision that can greatly impact the integrity and longevity of the weld. With decades of combined expert experience in metallurgy and welding technologies, our guide offers unparalleled insight into the best practices for selecting and using welding electrodes specifically designed for cast iron.
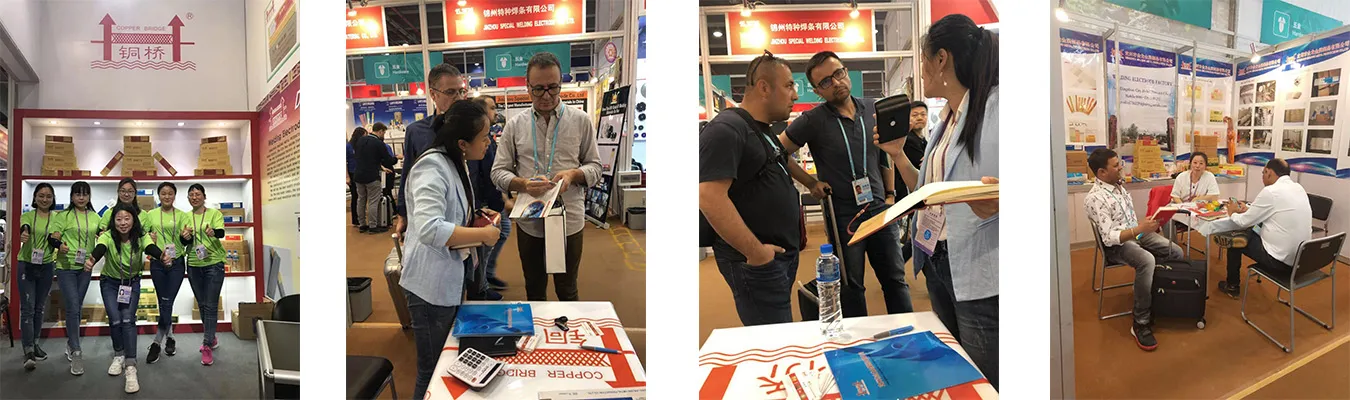
When dealing with cast iron, which is brittle by nature due to its high carbon content, the choice of electrode becomes paramount. The objective is not only to join the two pieces but also to maintain the mechanical integrity and functionality of the repaired structure. For this reason, our focus will be primarily on nickel-based electrodes, which have proven to offer superior performance in cast iron welding.
Nickel-based electrodes are preferred for several reasons they minimize cracking, offer excellent machinability post-weld, and provide a robust bond that withstands thermal and environmental stresses. Their composition allows them to absorb the carbon content of cast iron, reducing the brittleness of the joint. However, selecting the right type within the nickel-based family is crucial. For a typical cast iron repair, Nickel 99 (AWS A5.15) and Nickel 55 (AWS ENiFe-Cl) electrodes are commonly recommended.
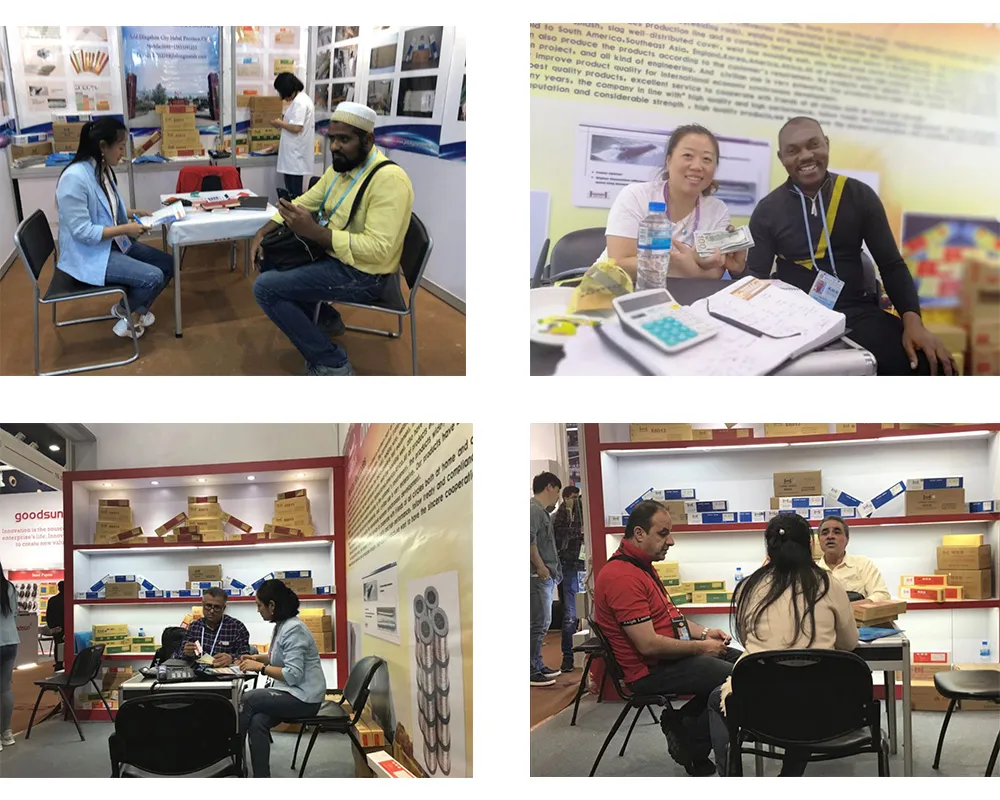
Nickel 99 is known for its high nickel content, making it ideal for applications where a soft, ductile weld is required. This electrode is particularly advantageous for intricate assemblies or thin-walled cast iron components owing to its ability to produce a clean, low-distortion weld. Nickel 99 is preferred when post-weld machining is anticipated, as the high nickel content allows for smoother cuts and finishes.
On the other hand, Nickel 55 electrodes, with approximately 55% nickel content, are recognized for their affordability while still offering considerable benefits in cast iron applications. They provide a good balance of strength and ductility and are especially useful for welding thicker sections of cast iron. Nickel 55 is also chosen for its excellent welding characteristics, including minimal spatter and ease of slag removal, which are vital for efficiency in both repair and fabrication settings.
cast iron to cast iron welding electrode
One of the critical challenges in cast iron welding is the risk of cracking. Our expertise suggests employing preheating techniques to counteract this issue. Preheating the cast iron to temperatures between 250°F and 600°F can significantly reduce the risk of thermal stress-induced cracking. Additionally, controlling the cooling rate post-welding is crucial. Allowing the workpiece to cool slowly, often by wrapping it in insulating material such as welding blankets, helps maintain weld integrity by preventing the formation of hard and brittle structures.
For applications demanding higher mechanical strength, considering electrodes that allow for post-weld heat treatment can be advantageous. Heat treatment homogenizes the microstructure of the welded joint, improving its toughness and resistance to fatigue.
In terms of user trust and product reliability, choosing welding electrodes from reputable manufacturers with ISO certification ensures adherence to quality standards. Look for products with robust technical support and comprehensive documentation that align with AWS specifications, ensuring they meet stringent industry benchmarks. Testimonials and case studies published in authoritative welding journals offer further imprints of trustworthiness, showcasing real-world successes and applications.
In conclusion, the selection of welding electrodes for cast iron hinges on understanding the specific requirements of the application and leveraging the experience-derived insights into nickel-based electrodes. By focusing on industry standards and best practices such as preheating and controlled cooling, welders can achieve durable and reliable welds on cast iron components. This expertise-driven approach affirms our commitment to excellence and reliability, making us a leader in welding technology solutions.