Welding cast iron to mild steel can be a challenging task that requires the right electrode and technique to ensure a strong and durable bond. When approaching this weld, one should consider the unique properties of both materials to avoid common pitfalls such as cracking, weak joints, or even complete structural failure.
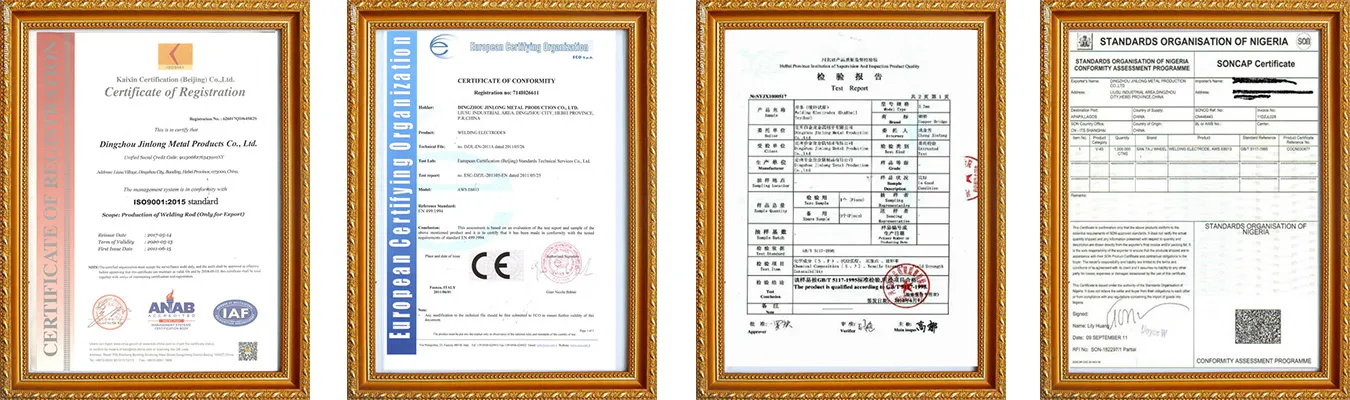
The choice of electrode is critical in this process. For the task at hand, nickel-based electrodes are often recommended due to their superior compatibility with both cast iron and mild steel. These electrodes, such as the Ni-Fe alloys, allow for better thermal expansion handling, reducing the risk of cracking typically associated with welding cast iron.
Before initiating the welding process, preparation of the materials is key. Cast iron surfaces are notorious for containing impurities and carbon that can interfere with the welding process. Thoroughly clean the surfaces to be welded, removing any oil, rust, or paint that could cause defects. Preheating the cast iron to a moderate temperature—typically between 500°F and 1200°F—can also alleviate stress during welding. However, when it comes to mild steel, preheating should be minimized as it can lead to increased brittleness.
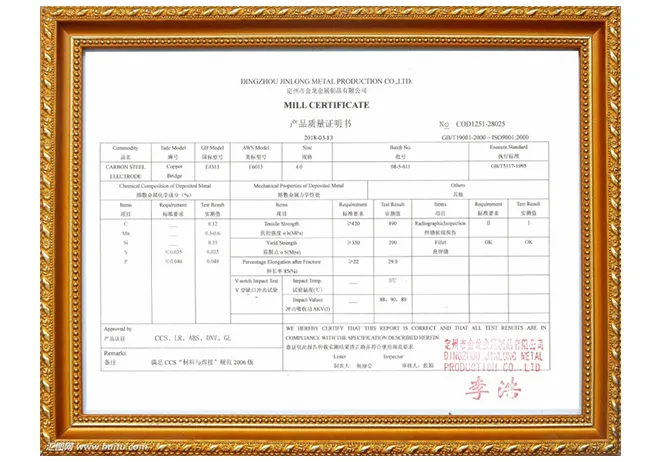
The methodology behind the weld also plays a crucial role. A technique that has proven successful is the use of short, intermittent welds, allowing the material to cool between passes. This intermittent approach minimizes heat buildup, reducing thermal stress and potential cracking. In critical applications, peening the weld bead while it is still hot can also help relieve stress.
In incorporating these materials together, a post-weld heat treatment is often necessary, especially if the welded component will be subject to thermal cycling or mechanical stress. Post-weld heat treatment can help in reducing residual stresses and enhance the overall tensile strength of the weld.
cast iron to mild steel welding electrode
Furthermore, working with reputable manufacturers for your welding supplies is crucial. Brands that have stood the test of time often back their products with research, testing, and quality assurances, ensuring your electrodes are designed with precision for specific applications like welding cast iron to mild steel.
For those who frequently engage in welding these two materials, understanding metallurgical reactions is valuable. Cast iron’s high carbon content can lead to carbide precipitation, which might affect the ductility of the weld area. Utilizing techniques that control cooling rates and carbon diffusion can help combat these challenges.
Finally, safety cannot be overlooked in this domain. Ensure that welding is done in a well-ventilated area to avoid the inhalation of harmful fumes, and always use protective gear to shield yourself from spatter, UV radiation, and intense heat.
In conclusion, while welding cast iron to mild steel is inherently challenging due to the differing properties of the metals, it is far from impossible. By selecting the appropriate nickel-based electrodes, meticulously preparing the materials, employing the right techniques, and opting for reputable products, it is feasible to create strong, reliable welds. Such endeavors not only require technical knowledge and skill but also an adherence to industry best practices. When these elements come together, the challenge of welding these materials turns into an opportunity to showcase craftsmanship and expertise in the field.