Welding is a precise art that necessitates a deep understanding of the materials involved, especially when joining two different metals like cast iron and carbon steel. The process can be quite challenging due to the different properties of these metals, which can lead to issues such as cracking if not handled properly. However, with the right electrode and technique, a successful and durable weld can be achieved.
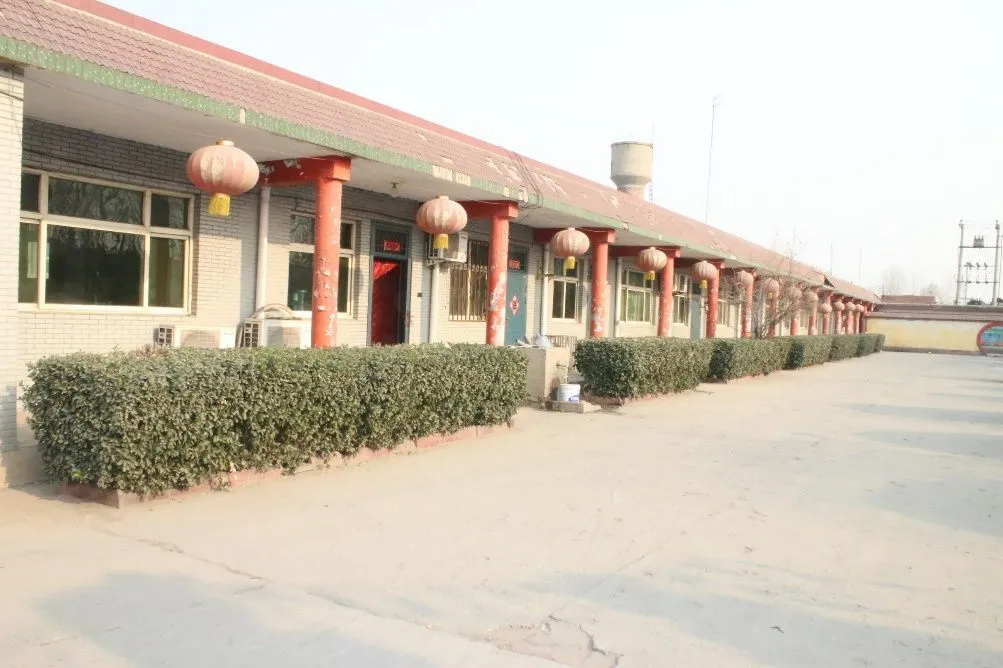
Cast iron, known for its excellent machinability and wear resistance, tends to be brittle and sensitive to thermal shock. On the other hand, carbon steel is valued for its strength, versatility, and ductility. The divergence in chemical composition and material characteristics between cast iron and carbon steel is substantial, and without the correct approach, welding these materials can result in structural weaknesses.
When embarking on welding cast iron to carbon steel, one critical component is the choice of electrode. The electrode serves as a filler material that must bridge the differences between the two metals. Metallurgically compatible electrodes, such as nickel-based electrodes, are often recommended due to their ability to absorb carbon and mitigate cracking. Nickel has excellent ductility and is less likely to crack when cooling, making it a preferred choice for this kind of weld.
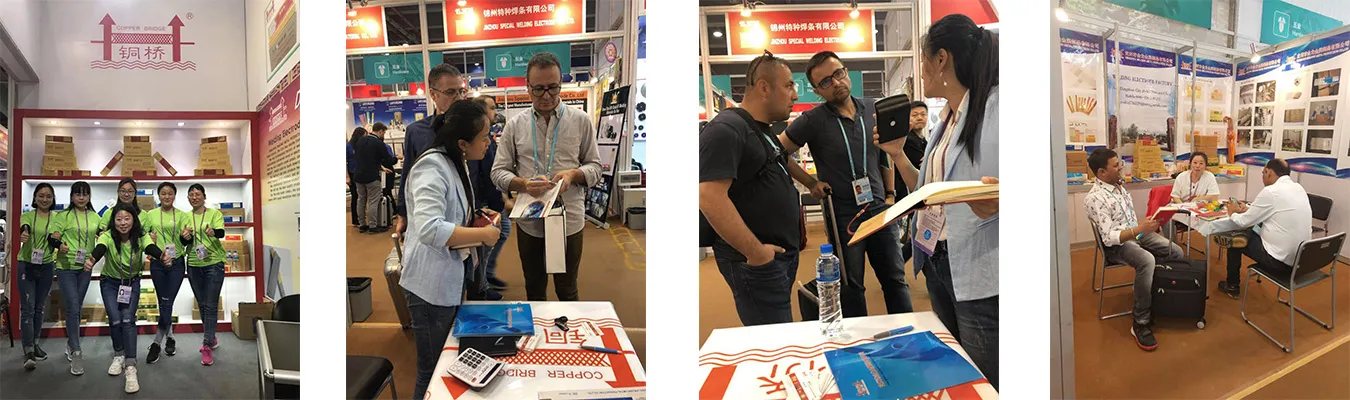
Experience-based recommendations often suggest preheating the cast iron before welding. This practice, known as preheat, serves to reduce the thermal gradient and minimize thermal shock, therefore preventing the development of cracks. The recommended preheat temperature for cast iron starts around 200°C (392°F) and can go up to 600°C (1112°F) depending on the thickness and complexity of the structure. It's equally important to maintain the heat during the welding process and implement a slow cooling method, often by wrapping the workpiece in an insulating material such as thermal blankets, to further reduce post-weld stresses.
cast iron to carbon steel welding electrode
Expertise in electrode manipulation and weld techniques also plays a crucial role. Welding with a stringer bead technique can help control the heat input and reduce the risk of overheating that could lead to cracking. Additionally, limiting the overall size of the weld bead and practicing intermittent welding can effectively manage the heat concentration and distribution.
Authoritative sources, including welding certification bodies and material science experts, stress the importance of using low-hydrogen electrodes and keeping them dry. Moisture leads to hydrogen inclusion in the weld, which is a common cause of cracks and defects. Storage of electrodes in a warm, dry environment or using portable electrode ovens ensures that hydrogen absorption from the atmosphere is minimized.
Trustworthiness in this specialized task also derives from the use of appropriate safety practices and equipment. Proper protective gear and adherence to safety standards prevent accidents and ensure the safety of both the welder and the integrity of the project. Consulting with welding professionals and following established welding codes and standards, such as those put forth by the American Welding Society (AWS), reinforces the quality and safety of the weld.
While the challenge of welding cast iron to carbon steel is significant, leveraging specialized knowledge, techniques, and the appropriate electrode can yield successful outcomes. The fusion of different metals requires not only technical skill but also careful planning, patience, and understanding of the materials involved. Whether for industrial applications or smaller-scale projects, mastering this welding process opens up new possibilities in metal fabrication and repair.