Cast iron is an essential material in many industrial applications due to its durability and strength. However, repairing or fabricating cast iron components can be challenging because of its brittleness and unique properties. One of the methods to address this is through TIG welding, which stands for Tungsten Inert Gas welding.
A critical component of successful TIG welding on cast iron is the selection of the right filler rod. Here's a comprehensive insight into choosing the best cast iron TIG filler rod to enhance your projects and extend component life.
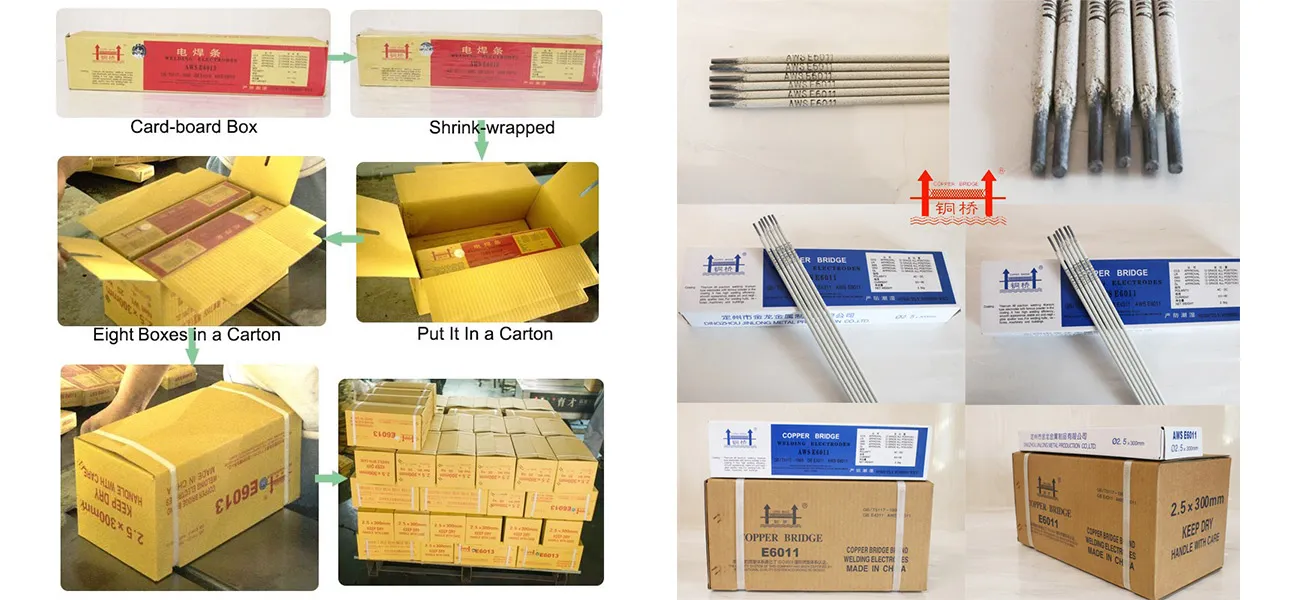
When choosing a TIG filler rod for cast iron, it's crucial to understand the nature of the material. Cast iron is highly carbon-rich, making it brittle and susceptible to cracking under stress or upon cooling. The ideal filler rod should mitigate these concerns by being compatible with the metallurgic composition of cast iron and offering flexibility once cooled. Nickel-based filler rods are often the top choice because they provide a higher degree of flexibility and reduce the risk of cracking.
For over two decades, professionals in the welding industry have trusted nickel-based rods for their ability to produce high-quality welds on cast iron. Nickel filler rods have several advantages they expand less than steel when heated, reducing stress during the cooling phase, and they offer superior elasticity, minimizing the risk of post-weld cracking. Their easy machinability makes repairing cast iron with these rods an efficient process, which is vital for reducing downtime in industrial operations.
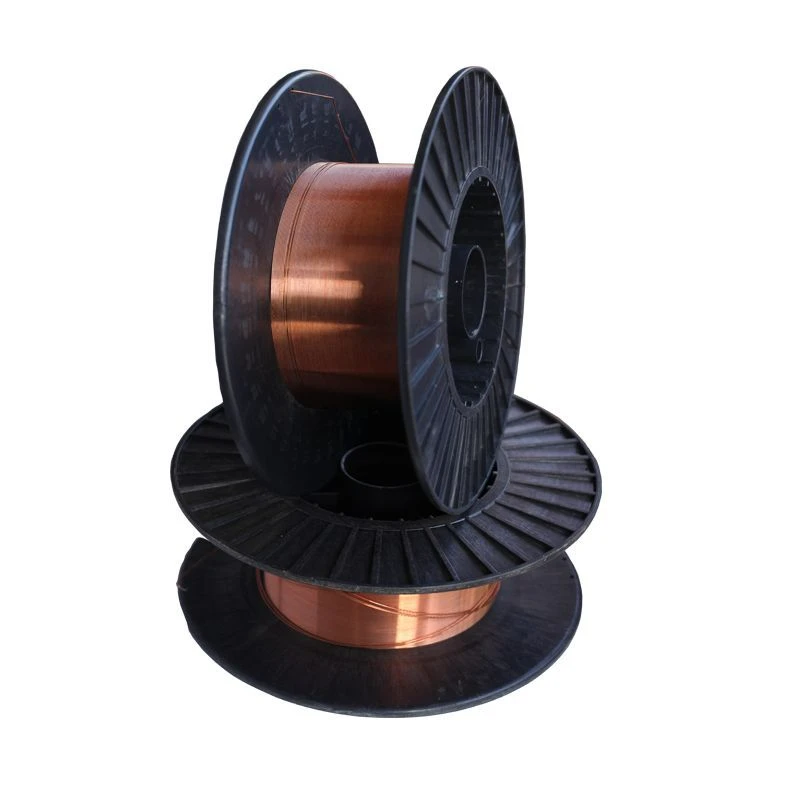
Among the available options, the ERNiFeCr-1 filler rod stands out for its adaptability to various types of cast iron, including grey cast iron and ductile iron. These rods have been shown to produce welds of exceptional strength and durability, attributes critical when dealing with load-bearing components. The ERNiFeCr-1’s composition ensures a stable austenitic microstructure that absorbs thermal expansion stress effectively.
cast iron tig filler rod
It's also important to consider preheating cast iron before welding and allowing it to cool slowly after the process to avoid thermal shock—another frequent cause of cracks. Optimizing these conditions, the right TIG filler rod not only guarantees structural integrity but also extends the longevity of cast iron parts significantly.
The experience of seasoned welders emphasizes the importance of thorough surface preparation for successful cast iron welding. Ensuring the cast iron surface is clean and free of contaminants like oil, rust, and paint helps the filler rod to bond better with the base material. This step is often underemphasized, but it can significantly affect the outcome of the welding process.
The expertise gleaned from decades of cast iron welding suggests that consistent practice and applying the latest techniques are crucial for mastering the use of TIG filler rods. The advancements in filler rod technology, combined with robust welding practices, underscore the reliability that consumers and industries can place in weld-repaired cast iron components. This makes welding a viable and cost-effective solution compared to casting anew.
In conclusion, choosing the right TIG filler rod for cast iron welding operations requires comprehensive knowledge of both the material and the welding procedure. Nickel-based filler rods, particularly ERNiFeCr-1, have demonstrated significant reliability and effectiveness. By aligning practical experience with authoritative knowledge, selecting the appropriate filler rod can result in consistent weld quality, extending the service life of cast iron components whilst maintaining structural integrity and operational safety.