When working with cast iron,
one of the trusted tools in a welder's arsenal is the oxy-acetylene welding rod. Known for its robustness and versatility, the cast iron oxy-acetylene welding rod is specifically designed to tackle the intricacies of welding cast iron components, combining the expertise of metallurgy and the experience of seasoned welders.
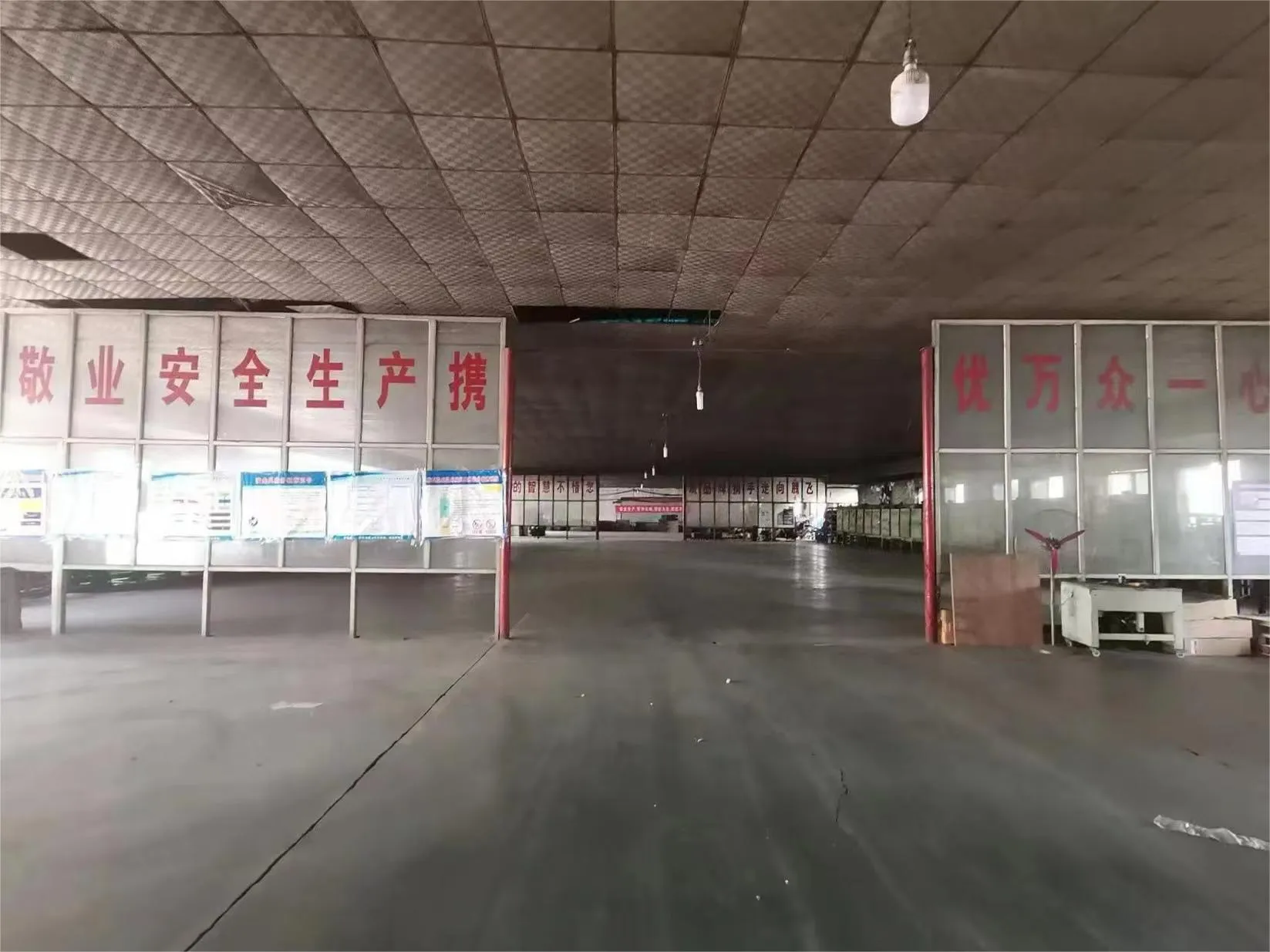
Cast iron, with its high carbon content, poses unique challenges during welding, such as cracking and distortion. The oxy-acetylene method, utilizing a specialized welding rod, addresses these issues effectively. Here, we delve into how the expert application of this tool achieves optimal results.
Experience indicates that pre-heating the cast iron piece is essential. This step reduces thermal shock, a common culprit of cracking. Using an oxy-acetylene setup allows for precise control of heat application. The welder, leveraging years of hands-on practice, adjusts the flame to pre-heat the area gradually. This gradual approach is paramount in maintaining the integrity of the cast iron.
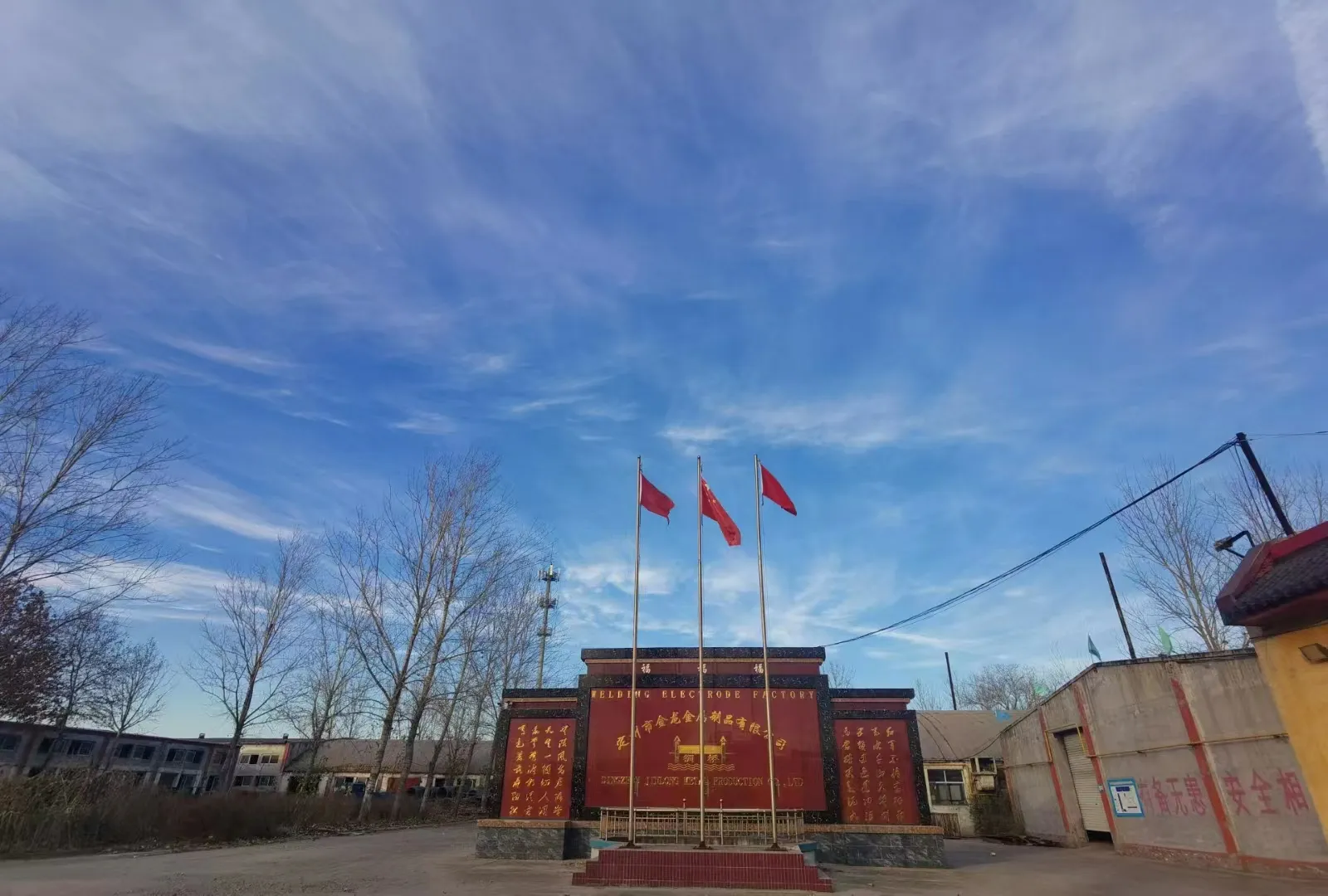
Expertise in the composition of the welding rod is another critical factor. These rods typically comprise a nickel-based alloy, which is conducive to forming a strong bond with the cast iron. The unique formulation caters to the thermal expansion properties of cast iron, which is more pronounced than other metals. A skilled welder recognizes the importance of selecting the right rod composition, as this ensures the weld’s durability.
cast iron oxy acetylene welding rod
When it comes to authoritativeness, reliance on these rods showcases adherence to industry standards. Professionals follow guidelines recommending an included angle of preparation between 60 to 90 degrees for better penetration. An authoritative approach also includes employing the 'walking the cup' technique that enhances weld strength by ensuring even distribution across the joint.
Trustworthiness stems from the welder’s commitment to meticulous post-weld processes. Cooling must be as gradual as the heating. To achieve this, experienced welders use heat blankets or slow cooling in ventilated sand beds, demonstrating their dedication to preventing the formation of stress fractures.
Also noteworthy is the role of the flux coating on the welding rod. It is instrumental in counteracting impurities inherent to cast iron surfaces. The flux cleans the weld area, minimizing oxidization, which could otherwise compromise weld quality. Trust is built by educating clients about the necessity of periodic inspection of welds on stress-bearing cast iron structures, a practice proven to prolong the life of the welds.
In summary, the combination of these elements—thorough pre-heating, expert selection of welding rod materials, adherence to authoritative welding techniques, and diligent post-process care—exemplifies the reliable use of cast iron oxy-acetylene welding rods. By employing them, professionals ensure structural integrity, demonstrating their prowess in a field that demands precision, knowledge, and an unwavering commitment to quality assurance. This comprehensive understanding illustrates why the cast iron oxy-acetylene welding rod remains a staple in the welder’s toolkit, trusted for delivering results that not only meet but exceed industry expectations.