TIG welding cast iron with silicon bronze offers a unique combination of properties that make it an excellent choice for specific applications. From an experience and expertise standpoint, understanding the intricacies of this technique can greatly enhance the quality and performance of your welds.
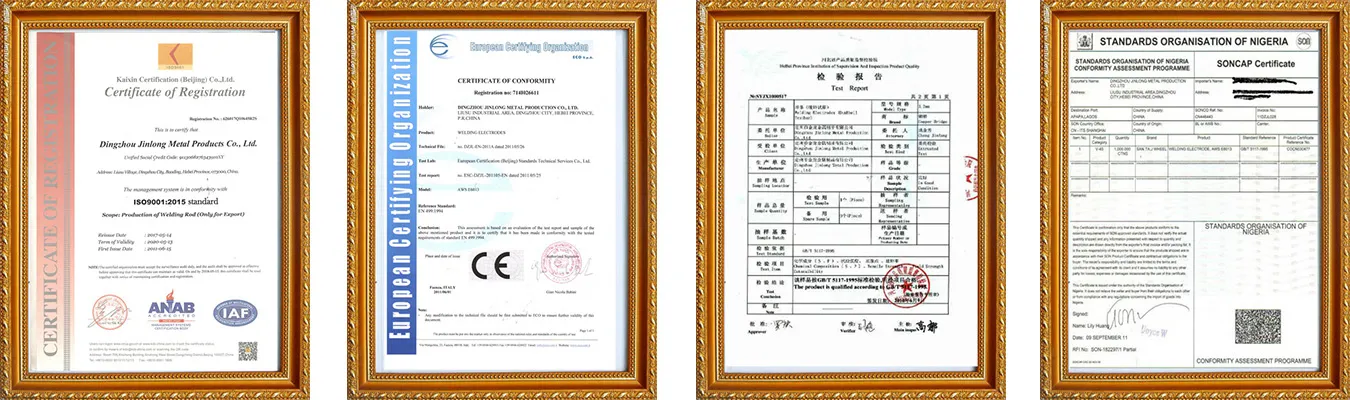
Traditionally, welding cast iron has been a challenging task due to its high carbon content, which can lead to cracking if not done correctly. The introduction of silicon bronze as a filler material in TIG welding significantly mitigates these challenges. Silicon bronze is highly regarded for its low melting point, ductility, and resistance to corrosion, which makes it particularly suitable for joining cast iron components in various industries, including automotive, construction, and artistic metalworking.
When using TIG welding for cast iron, the choice of silicon bronze filler rods is critical. These rods typically consist of about 3% silicon and the remainder copper, providing excellent mechanical properties and a lower melting point than cast iron, which helps to prevent undesirable thermal stresses and cracking. A common choice is the ER-CuSi-A rod, which provides excellent flow and wetting characteristics, ensuring a strong bond between the materials.
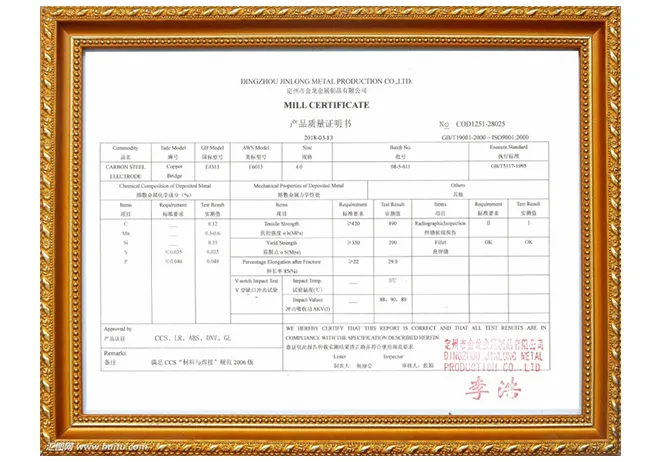
Preparation is key in TIG welding of cast iron with silicon bronze. Begin by thoroughly cleaning the cast iron surface to remove any contaminants such as grease, oil, or rust that could impair the weld quality. Preheating the cast iron to around 400°F to 600°F is highly advisable, as it helps to relieve thermal stress and reduce the risk of cracking. It’s essential to monitor the temperature closely to prevent overheating, which could lead to further complications.
The welding process itself requires a high level of expertise. Maintaining a shallow welding angle ensures better control over the weld pool. An AC welding power source with a high-frequency start is typically recommended to stabilize the arc, especially with silicon bronze due to its high conductivity. A key technique is to maintain a short arc length; this requires a steady hand and practiced skill to ensure the filler metal doesn’t excessively dilute into the cast iron base material.
tig welding cast iron with silicon bronze
Post-weld treatment is another important consideration. The cooling process must be closely controlled to prevent thermal shock. Slow cooling in a sand bed or using insulating blankets can be effective strategies. This gradual reduction in temperature minimizes the potential for residual stresses within the welded joint, thereby enhancing the durability of the repair or component.
One of the most compelling reasons to use silicon bronze is its versatility in applications beyond structural repairs. Automotive enthusiasts, for instance, value the aesthetic finish that silicon bronze imparts on custom exhaust components or artistic elements in vehicle restorations. In construction, it’s often employed to repair ornate architectural features, such as balustrades or fences, where an aesthetically pleasing finish combined with structural integrity is paramount.
Professionals and hobbyists alike must also be aware of safety considerations. TIG welding produces intense light and requires appropriate protective gear, including welding helmets with suitable shade filters, gloves, and flame-resistant clothing. Adequate ventilation is critical when working with silicon bronze due to the potential release of fumes that could be hazardous over prolonged exposure.
As an authoritative resource, this process benefits substantially from ongoing education and practice. Training sessions, collaborative workshops, and industry certifications are all valuable for those looking to refine their welding skills. Networking within professional circles and contributing to forums can provide insights and updates on best practices or new developments in the field.
TIG welding cast iron with silicon bronze truly combines the art and science of metallurgy and welding, creating opportunities for quality, reliable, and visually appealing welds. By mastering this process, welders expand their capabilities, opening doors to innovative applications and ensuring lasting results in crafted metalwork.