Choosing the right welding rod material is crucial for successful welding projects, particularly when working with complex materials or environments. The 7018 welding rod, often recognized for its dependable performance and versatility, is a staple in various industrial applications. Understanding the material composition, strengths, and recommended usages can significantly improve your welding outcomes.
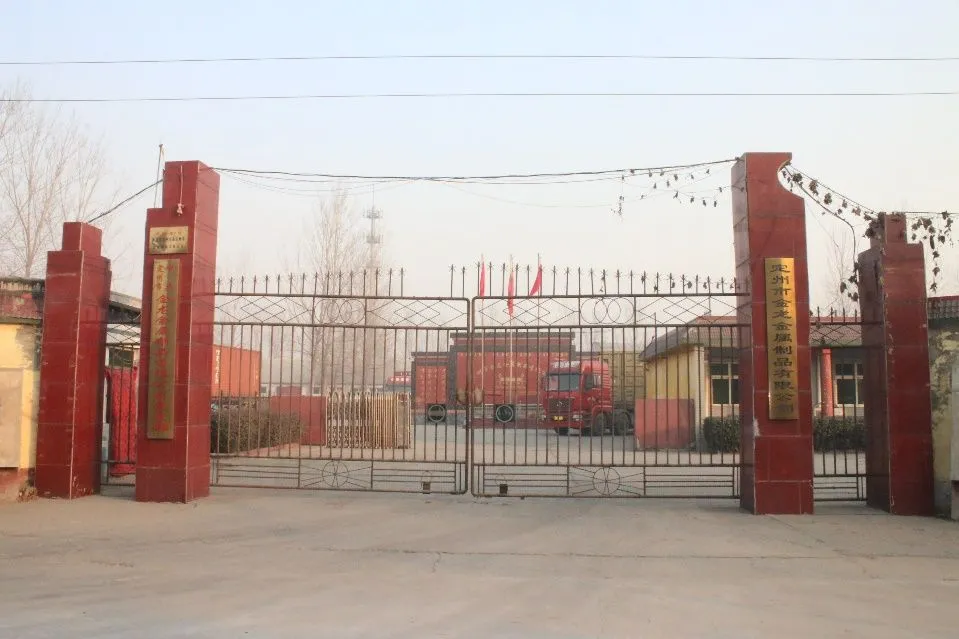
The 7018 welding rod is best known for its low-hydrogen iron powder coating. This feature contributes to a highly stable arc and minimized spatter, which are crucial for achieving clean and strong welds. A key attribute of the 7018 rod is its excellent tensile strength and ductility, typically rated at 70,000 psi. This makes it suitable for applications where weld integrity is critical, such as in construction, pipelines, and heavy machinery repairs.
Expertise in using the 7018 rod begins with understanding its composition. The mild steel core is enveloped in a flux coating designed to release hydrogen slowly. This low hydrogen content reduces the risk of weld cracking, particularly in steels prone to hydrogen embrittlement. As such, the 7018 rod is frequently used with structural steels and situations demanding high toughness and ductility.
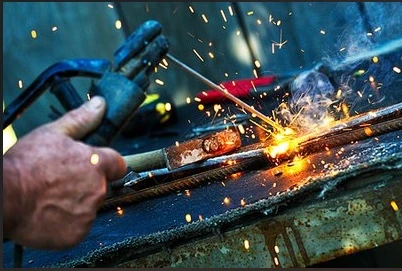
From an experienced welder’s perspective, one of the defining features of the 7018 rod is its necessity for a specific preparation and handling technique. It requires one to maintain it in a dry environment to prevent moisture absorption, which can compromise weld quality. Therefore, many professionals use electrode ovens to keep the rods at optimal conditions, ensuring the integrity of the weld.
Authoritative sources in the welding industry, such as the American Welding Society, recommend the 7018 rod due to its ability to work effectively in all positions while producing a smooth weld bead with very little clean-up required. The rod is also praised for its simplicity in producing a consistent and visually appealing weld, making it a favorite among both novices and seasoned welders.
7018 welding rod material
Building trustworthiness in your choice of using the 7018 welding rod involves recognizing its adaptability across various electrode types and current settings. It can be used in both alternating current (AC) and direct current (DC), though many professionals prefer DC for its more stable arc. Adapting the current settings to the material and thickness is crucial for achieving the best penetration and aesthetic finish.
The richness of experience shared by countless welders using 7018 welding rods is a testament to its reliability. Many welders have shared experiences where the 7018 rod stood out in repair projects, particularly in damp or outdoor conditions where low hydrogen is essential. Its capability to produce welds with exceptional strength and minimal defects makes it a preferred choice for maintenance teams dealing with critical infrastructure repairs.
In terms of expertise, those mastering the 7018 welding rod develop an understanding of the intricacies of its applications. For structural welds, maintaining precise movement and appropriate heat settings is pivotal for crafting sound joints. Welders refine these skills over years, often emphasizing the importance of a steady hand and attention to detail.
For anyone looking to enhance their welding outcomes, incorporating 7018 welding rods can be a defining factor due to their enhanced strength, flexibility, and ability to perform under demanding conditions. The combination of high tensile strength, low hydrogen properties, and ease of use yields a level of professionalism sought after in many critical applications. The 7018 welding rod is more than just a tool; it represents a mastery of skill and a commitment to craftsmanship in the welding community.