Understanding the intricacies of choosing the right 7018 rod sizes is vital for achieving optimal results in welding projects. This specific type of welding rod, known for its low-hydrogen iron powder coating and high tensile strength, is a standard choice among welders. It plays a pivotal role in the structural integrity and quality of the welds produced, making it essential to select the correct diameter to match the project requirements.
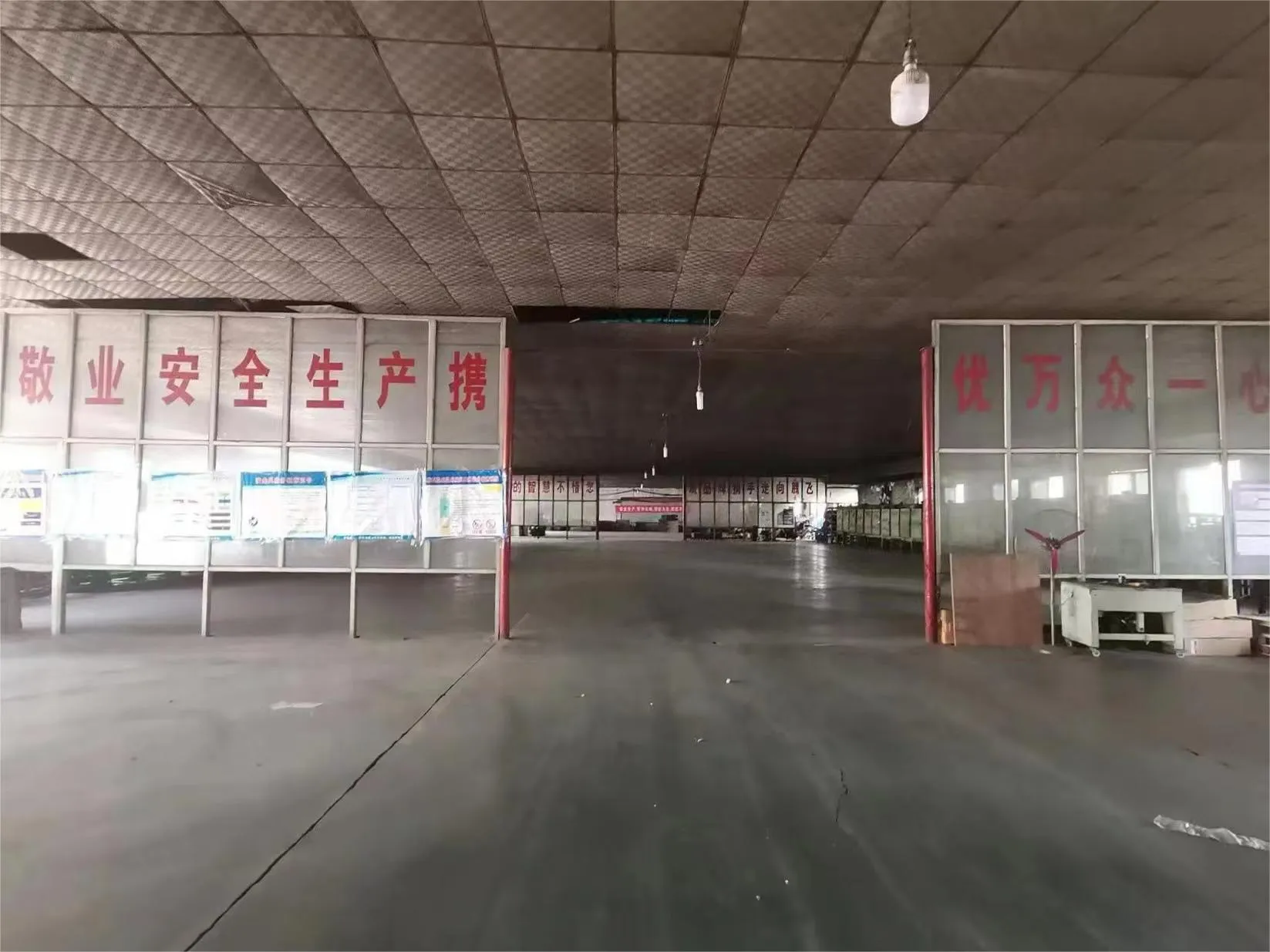
First and foremost, mastering the 7018 rod sizes entails acknowledging its usual diameters, which include 3/32 inches, 1/8 inches, 5/32 inches, and 3/16 inches. Each size caters to different welding needs, such as the thickness of the metal being welded and the precision required in the weld.
The choice between these sizes often hinges on the experience and expertise of the welder in assessing the specific project needs. For thinner materials and more intricate work, smaller diameters like the 3/32-inch rod are optimal. This size allows for detailed work without overwhelming the material, providing a smoother and more controlled arc that reduces the risk of burn-through. In contrast, the 1/8-inch size is slightly more robust, suited for medium-thickness metals and providing a balance between precision and strength, making it a versatile choice for a range of applications.
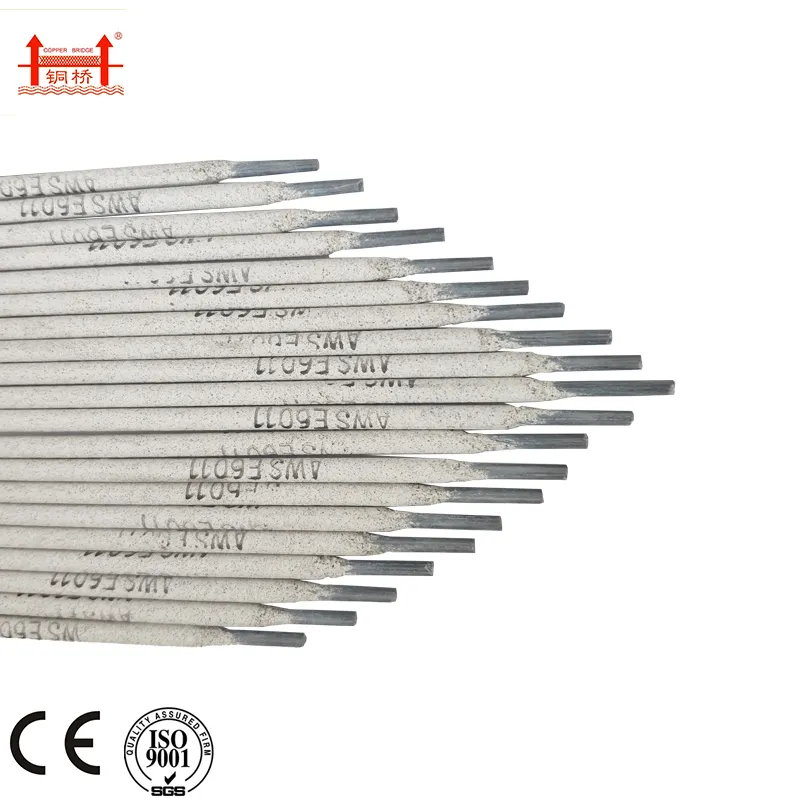
When the task involves thicker metals, larger sizes like 5/32 inches and 3/16 inches become necessary. These diameters are built to deposit more filler material quickly, ensuring complete penetration and strong joint formation. A welder's ability to adapt and select the right rod size based on the metal's thickness—whether working on construction equipment or heavy machinery repair—significantly impacts the project’s overall success.
Besides the metal's thickness, consideration of the welding position is crucial in determining the 7018 rod size to use. Lower diameters are often preferred when performing overhead or vertical welding, given their superior maneuverability and control. This tactic helps prevent gravity-related concerns such as weld puddle sagging, which can occur with larger rods in these positions.
7018 rod sizes
Trust plays a substantial role in deciding on the appropriate rod size.
A welder who understands the chemistry of the 7018 rod can maximize its benefits. The low-hydrogen properties reduce the risks of cracking over time, adding reliability to any weld. Therefore, effective drying of the rods is non-negotiable, typically using ovens set between 250-300°F (121-149°C) to keep them moisture-free, which is vital for maintaining their low-hydrogen characteristics.
Moreover, expertise involves understanding that correct amperage settings align with the chosen rod size. For example, a 3/32-inch rod typically runs on a lower amperage range, around 70-110 amps, while a 3/16-inch rod may require settings from 160-225 amps. Improper matching of rod size and amperage can lead to defects such as porosity or inadequate fusion, undermining the weld’s strength.
Therefore, true authority in selecting 7018 rod sizes is demonstrated by the depth of understanding displayed in balancing these various factors—metal thickness, position, rod condition, and electrical settings—all tailored to fit the specific demands of the task at hand.
Ultimately, welders who maintain a keen awareness of these parameters and continually refine their skill set will realize the full capacity of 7018 rods. This dedication not only enhances the quality and durability of their work but also establishes trust and credibility with clients who demand high performance and reliability from welding projects.