The versatility and reliability of the 7018 welding rod make it a staple in professional and hobbyist welding. Its unique characteristics make it indispensable for certain applications, enhancing the quality and durability of welds. In-depth knowledge and experience with the 7018 rod can significantly affect the efficiency and outcomes of welding projects.
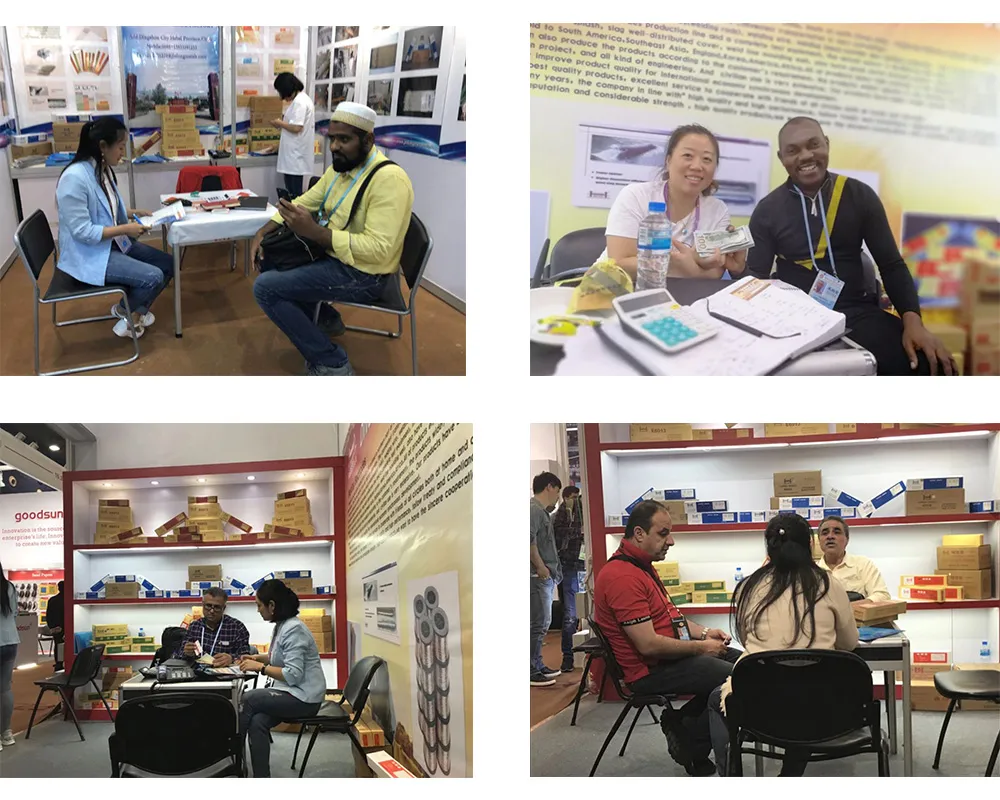
The 7018 welding rod, known for its low-hydrogen content, is particularly suited for structural welding projects where strength is paramount. Low-hydrogen electrodes like the 7018 are crucial in reducing the potential for hydrogen-induced cracking, especially in high-stress applications like bridges, skyscrapers, and pipelines. These rods are coated with a thick flux that provides a clean weld bead with minimal spatter, enhancing the aesthetic and structural quality of the weld.
In environments where the integrity of the weld is non-negotiable, such as pressure vessels, storage tanks, and other critical infrastructure, the use of the 7018 rod is recommended due to its superior mechanical properties. These rods are designed to produce a weld with a tensile strength of approximately 70,000 psi, providing ample toughness and resilience against dynamic and static loads.
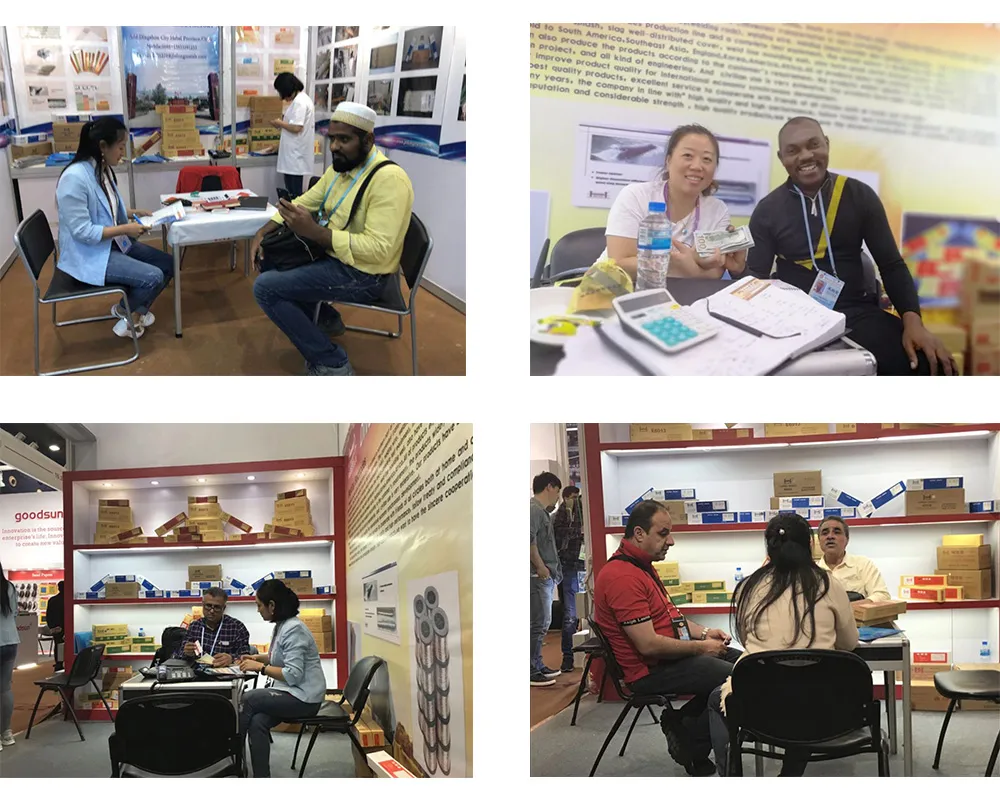
Another critical aspect of using the 7018 welding rod is its suitability for out-of-position welding. When welding vertically or overhead, the rod’s composition allows for better bead control and less slag dripping, making it easier for welders to manage the molten pool. This quality also makes 7018 rods ideal for maintenance and repair work, where the position of the weld cannot always be optimized.
Industry professionals appreciate the 7018 welding rod for its ability to bond with various metals, including carbon steel, low-alloy steel, and other ferrous metals. This adaptability simplifies inventory for welding operations across different sectors, reducing the need for multiple types of rods for different jobs. Furthermore, the 7018 rod provides high deposition rates, assisting in time-critical projects where efficiency is paramount without sacrificing quality.
when to use 7018 welding rod
However, the use of the 7018 rod isn't just about inherent rod characteristics. Successful application demands a controlled environment and precise technique. For optimum performance, it is crucial to keep these rods dry, as their low-hydrogen coating is sensitive to moisture, which can lead to poor weld quality and increased susceptibility to cracking. Proper storage in a rod oven or storage unit at specified temperatures extends their usability and ensures consistent quality.
Expert welders routinely emphasize the importance of pre-heating and post-heating treatments when working with thicker materials or in colder environments using the 7018 rod. Pre-heating helps minimize the risks of cracking in thicker sections by reducing thermal gradients, while post-heating can alleviate residual stresses, ensuring long-term durability of the weld.
In terms of setting and technique, welders should maintain a stable arc and a consistent travel speed. The arc length should be as short as possible, given that a longer arc can lead to increased spatter and a less stable arc, compromising the weld quality. Moreover, maintaining a slight angle (typically around 10 degrees from vertical) can enhance penetration and control during the welding process.
Professional training and certification play a pivotal role in effectively using 7018 rods. Continued education helps welders stay abreast of advancements in welding technology and techniques, ensuring they maintain high standards in quality and safety. Many welding courses and certifications specifically highlight the use of low-hydrogen electrodes, underlining their importance across various applications.
In conclusion, the 7018 welding rod is a vital tool in any welder's repertoire due to its robustness and adaptability. Whether working on structural projects, critical infrastructure, or intricate repairs, understanding when and how to use the 7018 rod optimizes weld quality and ensures the longevity of the welded structures. With proper handling and a keen understanding of technique, welders can leverage the full potential of the 7018 welding rod to meet and exceed industry standards, delivering results that are both reliable and enduring.